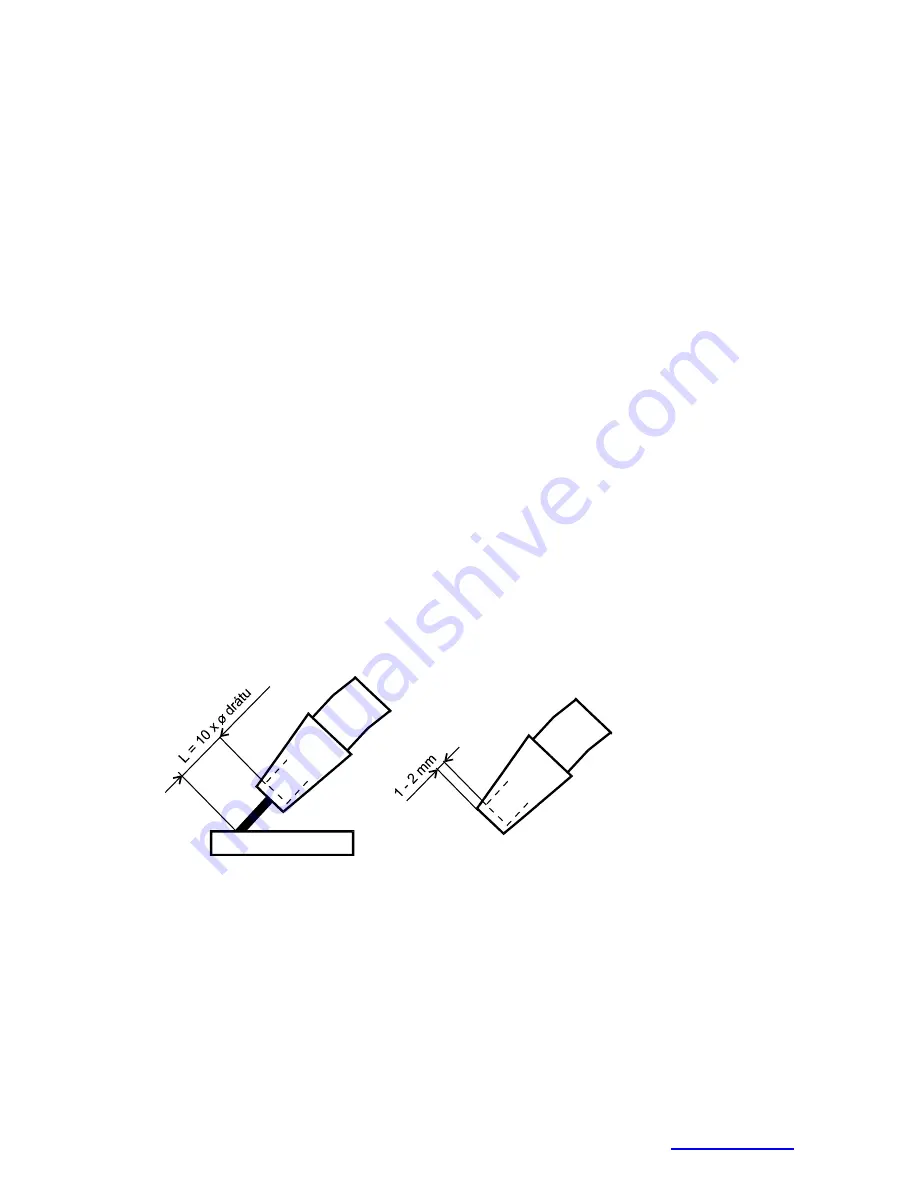
26/33
ALFA IN a.s. ©
www.alfain.eu
8. After the welding is finished, the measured values remain on the displays
(
HOLD
) for 6 s.
9. If a torch with remote control is connected, its display shows the machine
power (wire feed speed, tension) and the choke or JOB value. Use the
UP/DOWN
buttons to adjust the displayed value, use
the MODE button
to switch between functions.
WELDING FLOW - GENERAL INFORMATION
The amount of welding current depends on the wire feed speed and the amount
of tension. The arc characteristic ("hardness/softness") can be controlled by
correction of the choke.
The empirical relation U2 = 14+0,05I2 corresponds to the approximate setting of
welding current and voltage by MIG/MAG methods. According to this
relationship, we can determine the required voltage. When adjusting the voltage,
we must take into account the voltage drop when the welding load is applied.
The voltage drop is about 4.5-5.0 V per 100 A.
Adjust the welding current by adjusting the desired welding current for the
selected welding voltage by increasing or decreasing the wire feed speed until
the arc burns optimally.
Please note that the actual settings for optimum arc burn may vary slightly
depending on the position of the weld, the material and the fluctuations in line
voltage.
In order to achieve good weld quality and optimum welding current setting, the
distance of the feed line from the material should be approximately 10 x the
diameter of the welding wire (Fig. 11).
Figure 10 - Distance of the tube from the material
11 MMA WELDING (ELECTRIC WELDING - ELE)
1. Select the
MMA
method according to SELECTION OF THE WELDING
METHOD.
2. Disconnect the connecting cable
A2
, connect the electrode holder to the
quick connector
A8.