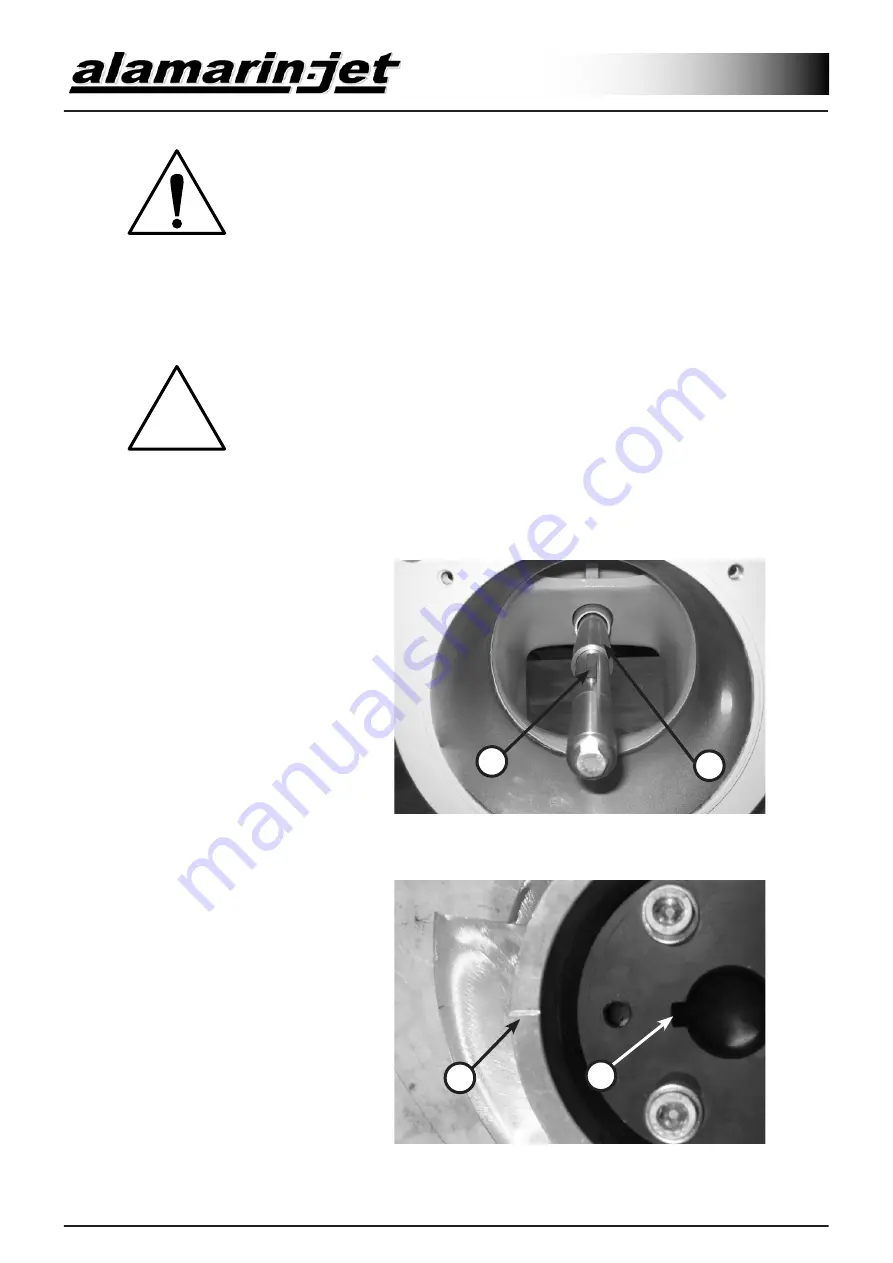
Repair Manual 1
1
Version 1.00
Version 1.00
Welding can create heat stress, which may cause the impeller to bre-
ak when used. This is why the manufacturer is not responsible for the
breaking down of a repaired impeller.
Impeller material: GTp10
Filler metal: EL-CuSn7 (ESAB OK 94.24).
If the impeller has been repaired with filler metal, it is to be machined
if necessary and it is imperative that it be balanced!
3.3. Installation
Screw the adjuster sleeve (A)
and the possible additional ring
on the shaft. The sleeve has a
left hand thread, but the additio-
nal ring is unthreaded.
Place the wedge (B) in its groo-
ve (figure 3.3-1).
Figure 3.3-1
A
B
The place for the wedge groo-
ve (A) on the mounting cone
is marked on the impeller with
a line. Set the cone so that the
wedge groove is aligned with
the line (B) as in figure 3.3-2.
Figure 3.3-2
B
A