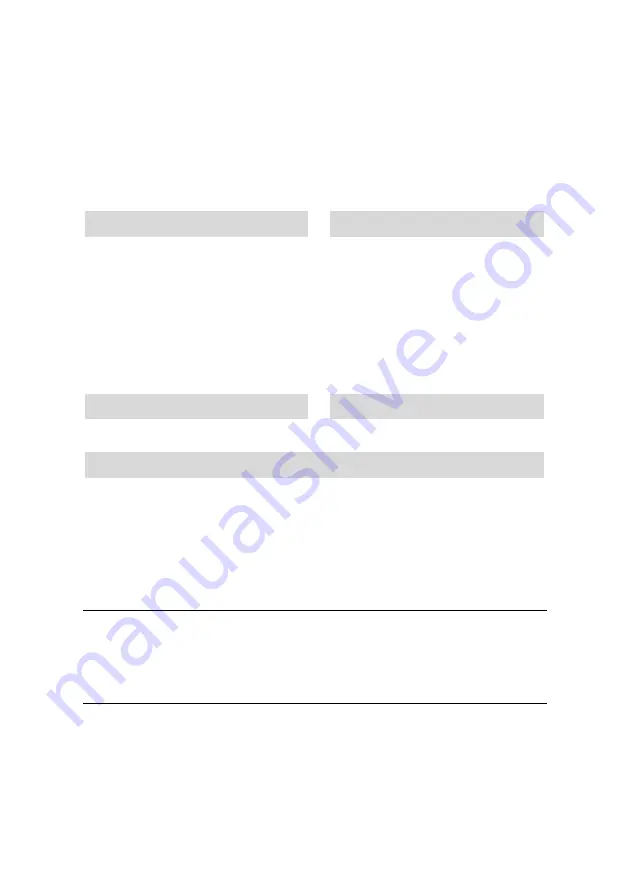
4
3
Getting Started
This part mainly introduces the basic operation and use of the BUNKER MINI platform, and introduces how to carry
out the secondary development of the vehicle body through the external CAN port and the CAN bus protocol.
3.1
Use and operation
Check
Start up
Check the vehicle body condition. Check whether
there is any obvious abnormality in the vehicle
body; if so, please contact after-sales support;
Check the emergency stop switch status. Confirm
that the Q1 emergency stop button at the rear is in
a released state;
When using for the first time, confirm whether Q2
(power switch) in the rear electrical panel is
pressed; if so, please press and release it, and it
will be in a released state
Press the power switch (Q2 in the electrical
panel), under normal circumstances, the light of
the power switch will be on, and the voltmeter
will display the battery voltage normally;
Check the battery voltage. If the voltage is
greater than 24V, it indicates that the battery
voltage is normal. If it is less than 24V, the
battery is low, please charge it;
Power off
Emergency stop
Press the power switch to cut off the power;
Press the emergency stop switch at the rear of
the BUNKER MINI body;
Basic operation process of remote control
After the BUNKER MINI robot chassis is started normally, turn on the remote control and select the
control mode as the remote control mode, so that the motion of BUNKER MINI platform can be
controlled by the remote control.
3.2
Charging
BUNKER MINI products are equipped with a standard charger by default, which can meet the charging
needs of customers.
The specific operation process of charging is as follows:
Make sure that the BUNKER MINI chassis is in a power-off state. Before charging, please confirm that Q2
(power switch) in the rear electrical console is turned off
;
Insert the plug of the charger into the Q4 charging interface in the rear electrical control panel
;
Connect the charger to the power supply and turn on the charger switch to enter the charging state.
When charging by default, there is no indicator light on the chassis. Whether it is charging or not depends
on the status indication of the charger.
3.3
Development
BUNKER MINI products provide a CAN interface for users’ development, through which users can
command and control the vehicle body.
BUNKER MINI products adopt CAN2.0B standard for the CAN communication standard, with the
communication baud rate of 500K and the message format of MOTOROLA. The moving linear velocity and
Содержание BUNKER MINI
Страница 1: ......
Страница 6: ......
Страница 22: ...16 6 Product Dimensions 6 1 Illustrations of product outline dimensions...
Страница 23: ...17 6 2 Illustrations of top expansion bracket dimensions...
Страница 24: ...Official distributor WORLDWIDE david denis generationrobots com 33 5 56 39 37 05 www generationrobots com...