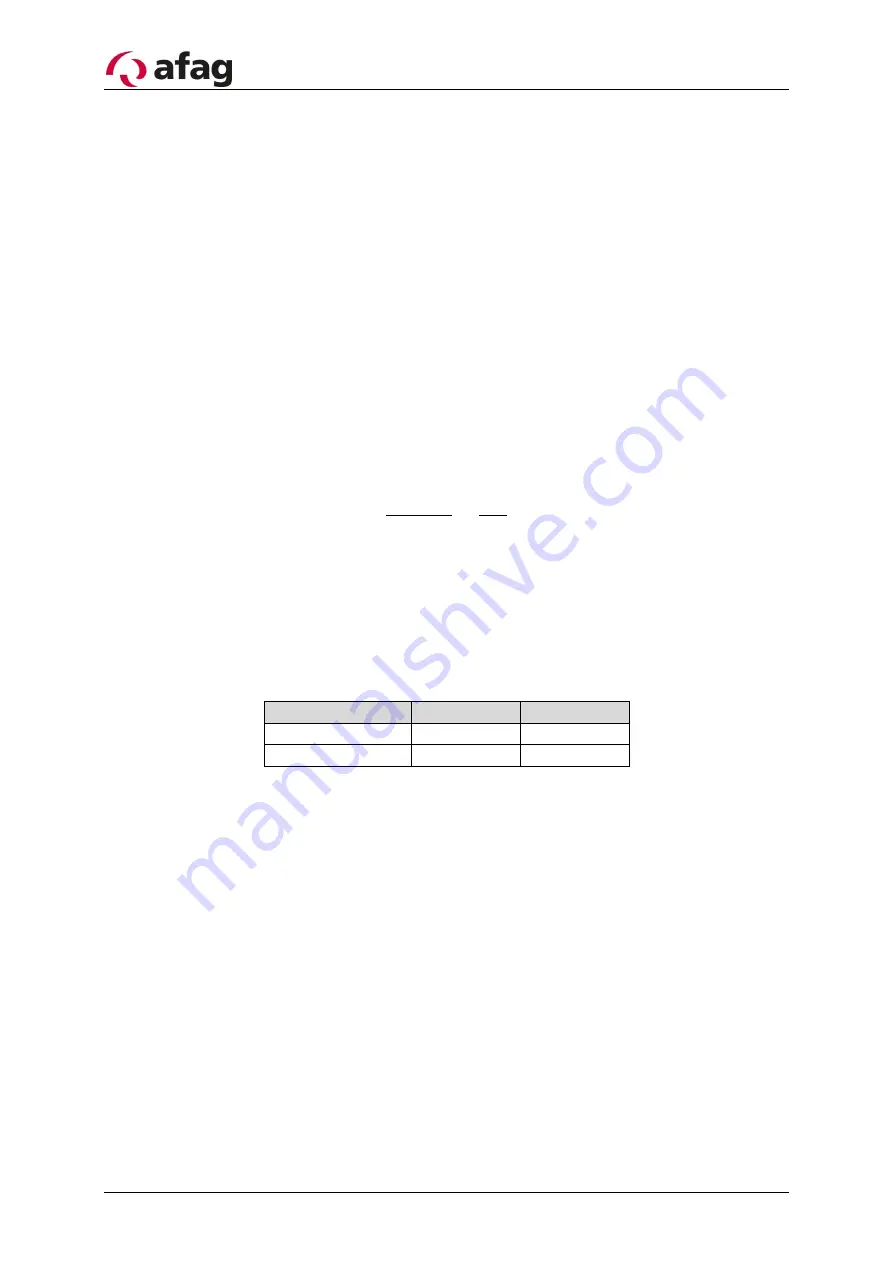
Page 14
16/05/2019
R03.0
4
Operating instructions
The first step in adjusting the linear feeders is always to balance the masses and
then to adjust the natural frequency.
4.1
Feeder track design
The linear tracks must be unyielding so that the transport pulses generated by the
unit are fully transferred to the work pieces and no superimposed natural vibration
can adversely affect the transport process. This requirement has priority over mass
reduction measures. The preferred material for linear tracks is tool steel (e.g. 1.2842,
90MnCrV8). Linear track design should adhere to the useful masses specified in
chapter 2 Table 1: Technical data and Table 4: Obligatory values for the working
weight
The following size ratio should be aimed for with regard to the feeder track cross-
section:
𝐻𝑒𝑖𝑔ℎ𝑡
𝑊𝑖𝑑𝑡ℎ
=
2,5
1
The recommended dimensions are listed in
. The di-
mensions are for one vibrating section and can be applied to each of the two vibrat-
ing sections.
Table 3:
Linear track dimensions
HLF07
-P
HLF12
-P
Height [mm]
400
500
Width [mm]
17
17
4.2
Balance of weights
The oscillating forces in the base plate of the Afag Linear Feeder are compensated
almost completely due to the principle of opposing oscillations (push-pull). This bal-
ance of oscillating forces is however only achieved if:
1.
The working weight and the counterweight are balanced as closely as possi-
ble.This means that the working weight and the counterweight are equal. The work-
ing weights specified for respective sizes are listed in
below. The working
weight is the total weight of all components attached to the mounting plate including
the side plate. The balance of weight is verified by simply weighing the working
weight.
2.
The centre of gravity of the working weight is located in the range represented in
Both conditions have to be taken into consideration at the construction stage of the
feeder track. An optimal balance of weight is achieved when almost no residual vibra-
tions can be detected in the substructure.