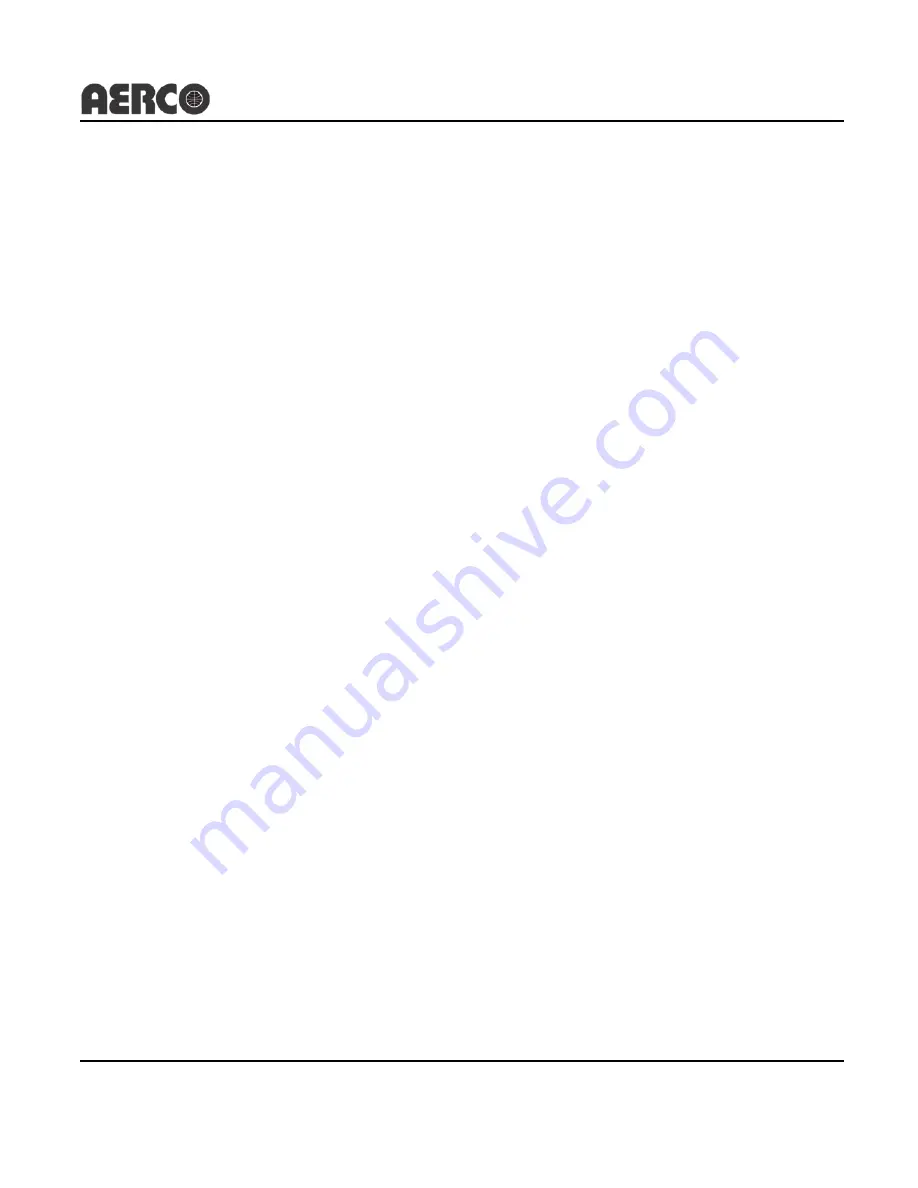
MC2: 10/03/12 Page
33
of
90
GF-115-H
TAG-0083_0B
AERCO International, Inc.
•
100 Oritani Dr.
•
Blauvelt, NY 10913
•
Ph: 800-526-0288
CHAPTER 7:
BOILER OPERATION
7.1 Introduction to Boiler Operation
The Modulex is a cast aluminum body boiler consisting of mutually connected combustion chambers,
each having its own burner, blower and air pressure switch, gas valve, igniter and flame detection.
Each group of these components is referred to as a module.
The boiler has supply and return temperature sensors that the System (E8) Manager uses to monitor
total outlet temperature from each module and the system return water temperatures before being
redistributed to each module. These sensors are negative temperature coefficient (NTC) sensors and
are designated the Global Flow Sensor for the supply sensor and the Global Return for the return
sensor.
Each module has its own temperature sensor called the Local Flow NTC, which monitors the
water temperature of each module. The water temperature measured by the Local NTC sensor is
compared to the return supply water temperature. If for any reason the temperature difference between
the Local Flow and the Global Return temperatures becomes greater than 54°F (30°C), the module or
modules will begin to modulate as follows:
•
0°F to 54°F (0°C to 30°C)
Normal Operation
•
54°F to 63°F (30°C to 35°C)
Burner will begin Modulating down
•
63
o
F to 72
o
F (35°C to 40°C)
Burner will stay at 45,500 BTU’s
•
Above 72°F (40°C)
Burner will shut off
The variable speed fan's pressure drives the gas valve to allow gas to enter into the pre-combustion
chamber where it mixes with the combustion air. The mixed air and gas pass thru the check valve on to
the burner surface for ignition. Combustion gases pass thru the heat transfer surfaces. Flue gases and
condensate then exit the heat exchanger entering into the condensate tray.
7.2 Modulation Theory
One of the operating principles for this boiler is to have as many modules as possible operate
simultaneously at minimum load to reach the maximum efficiency. This is maintained by the System
Manager (E8) which determines a percent of modulation based on the difference between the set point
temperature and the actual supply water (global flow) temperature. This operating principle provides
efficiencies much higher than those obtained in traditional groups of small boilers installed in cascade.
Each of the boiler’s modules represents a maximum output of 151.5 MBH (44.4 kW). The number of
modules x 100% determines the maximum output expressed in percent. For example, if a four module
boiler is requested to operate at its max output, this shall be 400%, i.e. 151.5 MBH (44.4 kW) x 4
modules = 606 MBH (177.6 kW) = 400%.
If the required percentage is 200%, each module will operate at 50% output. This equals a total of 303
MBH (88.8 kW) out of a possible 606MBH (177.6 kW), and each module will be operating at 75.75
MBH (22.2 kW) out of a possible 151.5 MBH (44.4 kW).
When the output shared on each module is less than approximately 30%, one module after the other is
automatically turned off and the remaining output is shared on modules having the smallest number of
operation hours (by the automatic operation-time calculating system).
7.3 Ignition Sequence
The ignition sequence may be described as follows: The Ignition Burner Management Module (BMM) is
powered on and, after 5 seconds, the fan starts at minimum speed. The fan remains running, actuating
the air pressure switch and pre-purging the combustion chamber for 10 seconds. Actuating the air
pressure switch toggles it from normally open (NO) to normally closed (NC). This energizes the ignition