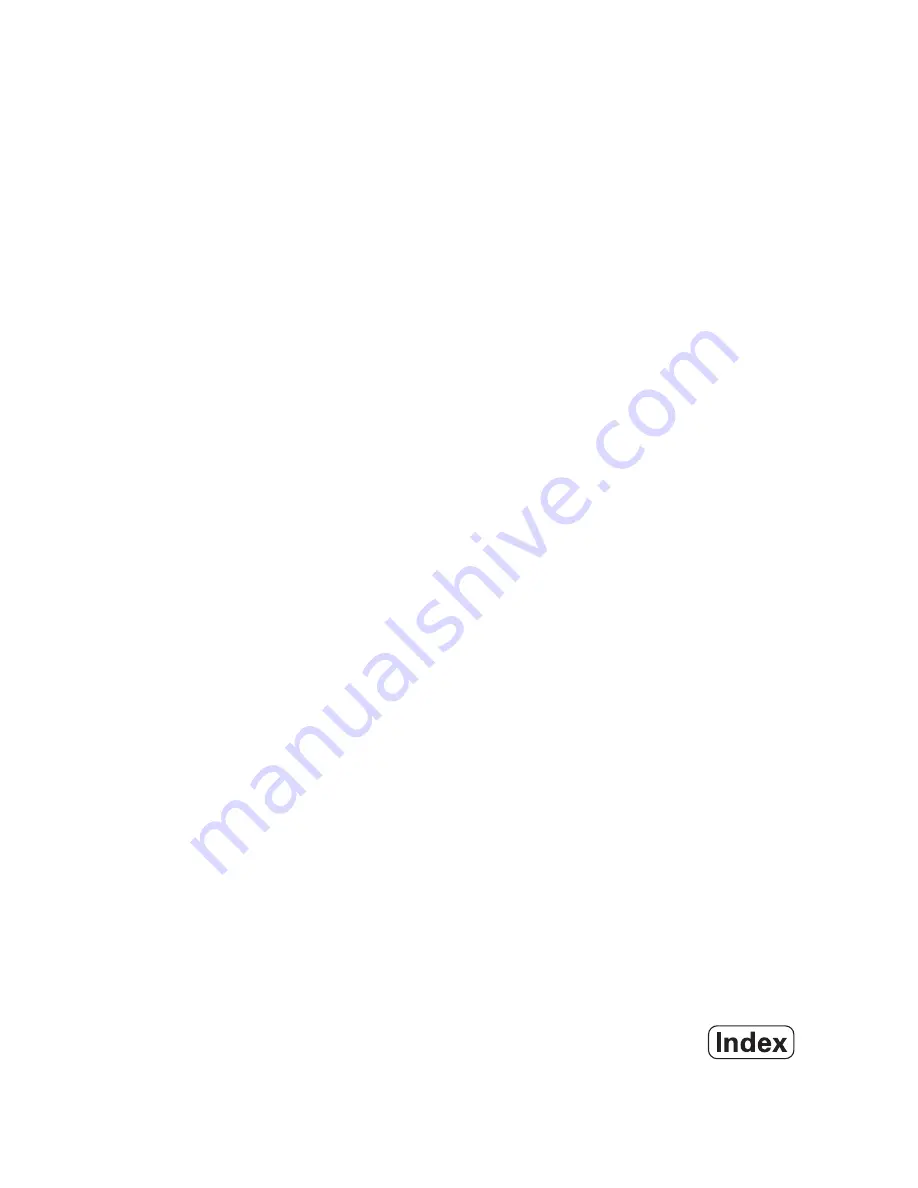
A
absolute coordinates
3
Absolute Distance Preset
23
Absolute Workpiece Positions
3
Actual Position, Nominal Position, and Distance-
To-Go
2
Actual Value/Distance-To-Go soft key
10
Arc Milling
33
Axis Labels
6
B
Backlash Compensation
51
C
Calling a Tool from the Tool Table (Turning)
36
Circle, and Linear Pattern Table Entry
28
,
31
Circle, and Linear Patterns
27
Console adjustment
15
Counter Settings
52
D
Datum Soft Key - Turning
38
Datum soft key (Milling)
20
Datums
2
Diagnostics
53
Diameter Axes (Milling)
13
Disabling Z0, and Z Coupling
43
Display Area
6
Display configuration
48
Distance-To-Go (incremental)
10
DRO Dimensions
63
E
Edge Finder (milling applications only
12
Edge Finder (milling applications only)
12
Electrical Requirements
55
Enable Ref soft key
9
Enable/Disable Ref Function
9
Enabling Z0, and Z Coupling
43
Encoder Reference Marks
5
Encoder Setup
46
Environmental Specifications
55
Error Compensation
48
F
Fundamentals of Positioning
2
G
General Navigation
7
General Operations for 200S
6
Grounding (Earth)
55
I
Import/Export (setting)
15
Incline, and Arc Milling
30
incremental coordinates
3
Incremental Distance Preset
25
Incremental workpiece positions
3
Installation Setup Parameters
46
J
Job Clock
14
Job Setup menu
11
Job Setup Parameters
11
L
Language
15
Linear Error Compensation
49
M
Measured Value Output
13
,
58
Milling Specific Operations
18
Mirroring a part
12
N
Near Zero Warning
13
No Ref soft key
9
O
Operating Instructions
1
Operating Modes
10
P
Position Recall
53
Power Up
7
Preset
23
Preventative Maintenance
55
Probing Functions for Datum Setting - Mill
20
R
Radius/Diameter
41
Reading head position
4
REF indicator
8
Ref Symbols
6
Remote Switch
14
Содержание 200S READOUTS
Страница 1: ...200S READOUTS REFERENCE MANUAL ...
Страница 2: ......
Страница 6: ...iv ...
Страница 8: ...vi ...
Страница 10: ...viii ...
Страница 15: ...1 Operating Instructions ...
Страница 58: ...44 I I 4 Turning Specific Operations ...
Страница 59: ...45 Technical Information ...
Страница 78: ...64 I II 6 Dimensions ...
Страница 81: ......