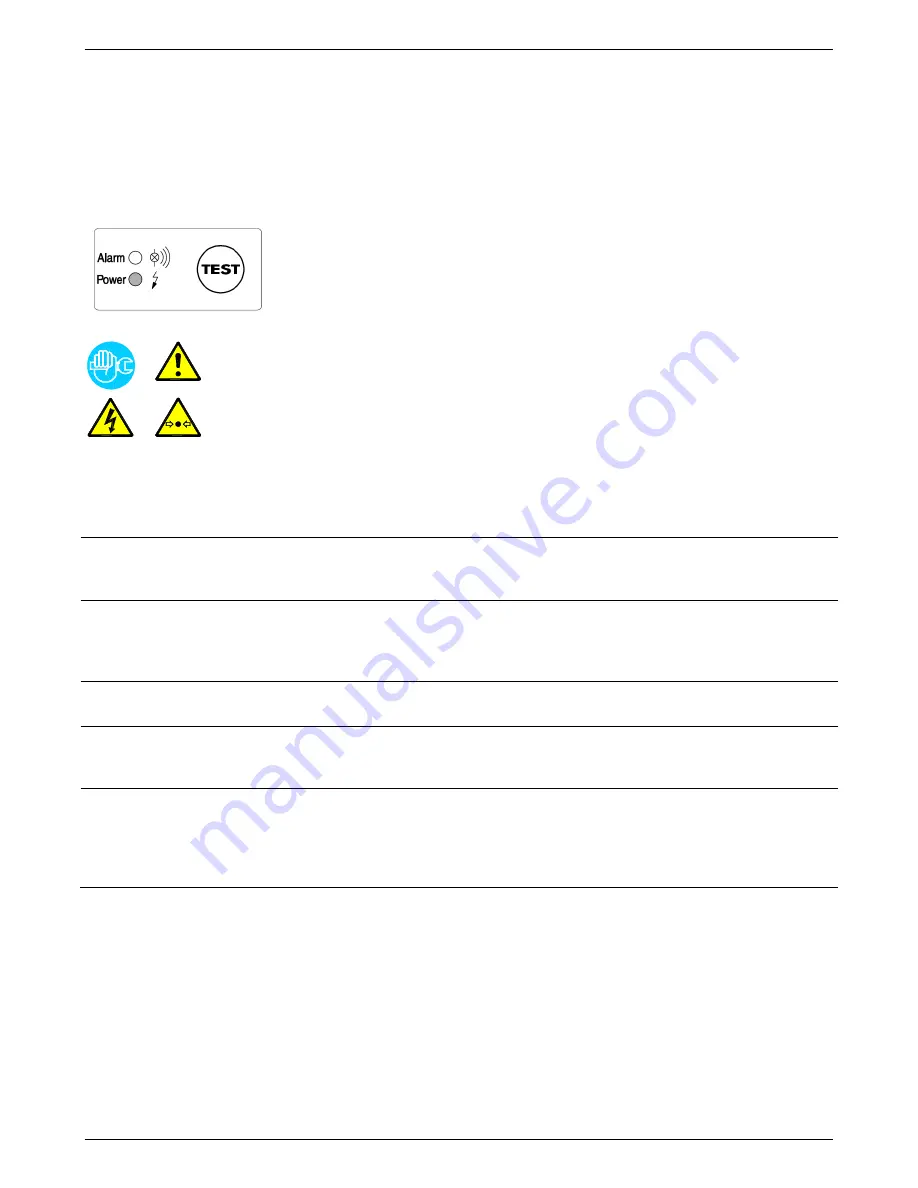
Technical description
30 – EN
ACT 600 – 5000
7.16 Electronic drainer
This drain consists of a condensate accumulator where a capacitive sensor continuously checking liquid
level is placed: as soon as the accumulator is filled, the sensor passes a signal to the electronic control and
a diaphragm solenoid valve will open to discharge the condensate. For a complete condensate discharge
the valve opening time will be adjusted exactly for each single drain operation. No condensate strainers are
installed. No adjusting is required. A service valve is installed before the electronic drain in order to make
check and maintenance easily.
At dryer start-up verify that this valve is open.
Control panel
Power Led On - drainer ready to work / supplied
Alarm Led Blinking - drainer in alarm condition
TEST Button Discharge test (keep pushed for 2 seconds)
Troubleshooting
Only qualified personnel should perform troubleshooting and or
maintenance
operations.
Prior to performing any maintenance or service, be sure that :
no part of the machine is powered and that it cannot be connected to the mains
supply.
no part of the machine is under pressure and that it cannot be connected to the
compressed air system.
maintenance personnel have read and understand the safety and operation
instructions in this manual.
SYMPTOM
POSSIBLE CAUSE - SUGGESTED ACTION
No led lighting up.
Verify that the system is powered.
Verify the electric wiring (internal and/or external).
Check internal printed circuit board for possible damage.
Pressing of Test button, but
no condensate discharge.
The service valve located before the drain is closed - open it.
The dryer is not under pressure - restore nominal condition.
Solenoid valve defective - replace the drain.
The internal printed circuit board is damaged - replace the drain.
Condensate discharge only
when Test button is pressed.
The capacitive sensor is too dirty - open the drain and clean the sensor
plastic tube.
Drain keeps blowing off air.
The diaphragm valve is dirty - open the drain and clean it.
The capacitive sensor is too dirty - open the drain and clean the sensor
plastic tube.
Drain in alarm condition.
The capacitive sensor is too dirty - open the drain and clean the sensor
plastic tube.
The service valve located before the drain is closed - open it.
The dryer is not under pressure - restore nominal condition.
Solenoid valve defective - replace the drain.
NOTE : When the drain is in alarm condition, the diaphragm solenoid valve will open 7.5 sec every 4
min.
Содержание 1500-2500
Страница 17: ...Technical data ACT 600 5000 17 EN 6 Technical data 6 1 Technical data ACT 600 5000 3 460 60 ...
Страница 18: ...Technical data 18 EN ACT 600 5000 6 2 Technical data ACT 600 5000 3 575 60 ...
Страница 38: ...Maintenance troubleshooting spare parts and dismantling 38 EN ACT 600 5000 ...
Страница 41: ...Attachments ACT 600 5000 41 EN 9 1 Dryers dimensions 9 1 1 ACT 600 1250 ...
Страница 42: ...Attachments 42 EN ACT 600 5000 9 1 2 ACT 1500 2500 ...
Страница 43: ...Attachments ACT 600 5000 43 EN 9 1 3 ACT 3000 3750 ...
Страница 44: ...Attachments 44 EN ACT 600 5000 9 1 4 ACT 4000 5000 ...
Страница 45: ...Attachments ACT 600 5000 45 EN 9 2 Exploded views 9 2 1 ACT 600 1250 Air Cooled ...
Страница 46: ...Attachments 46 EN ACT 600 5000 9 2 2 ACT 600 1250 Water Cooled ...
Страница 47: ...Attachments ACT 600 5000 47 EN 9 2 3 ACT 1500 2500 Air Cooled ...
Страница 48: ...Attachments 48 EN ACT 600 5000 9 2 4 ACT 1500 2500 Water Cooled ...
Страница 49: ...Attachments ACT 600 5000 49 EN 9 2 5 ACT 3000 3750 Air Cooled ...
Страница 50: ...Attachments 50 EN ACT 600 5000 9 2 6 ACT 3000 3750 Water Cooled ...
Страница 51: ...Attachments ACT 600 5000 51 EN 9 2 7 ACT 4000 5000 Air Cooled ...
Страница 52: ...Attachments 52 EN ACT 600 5000 9 2 8 ACT 4000 5000 Water Cooled ...
Страница 66: ...Blank pages 66 EN ACT 600 5000 10 Blank pages ...
Страница 67: ...Blank pages ACT 600 5000 67 EN ...
Страница 68: ...Original instructions are in ENGLISH Subject to technical changes without prior notice errors not excluded ...