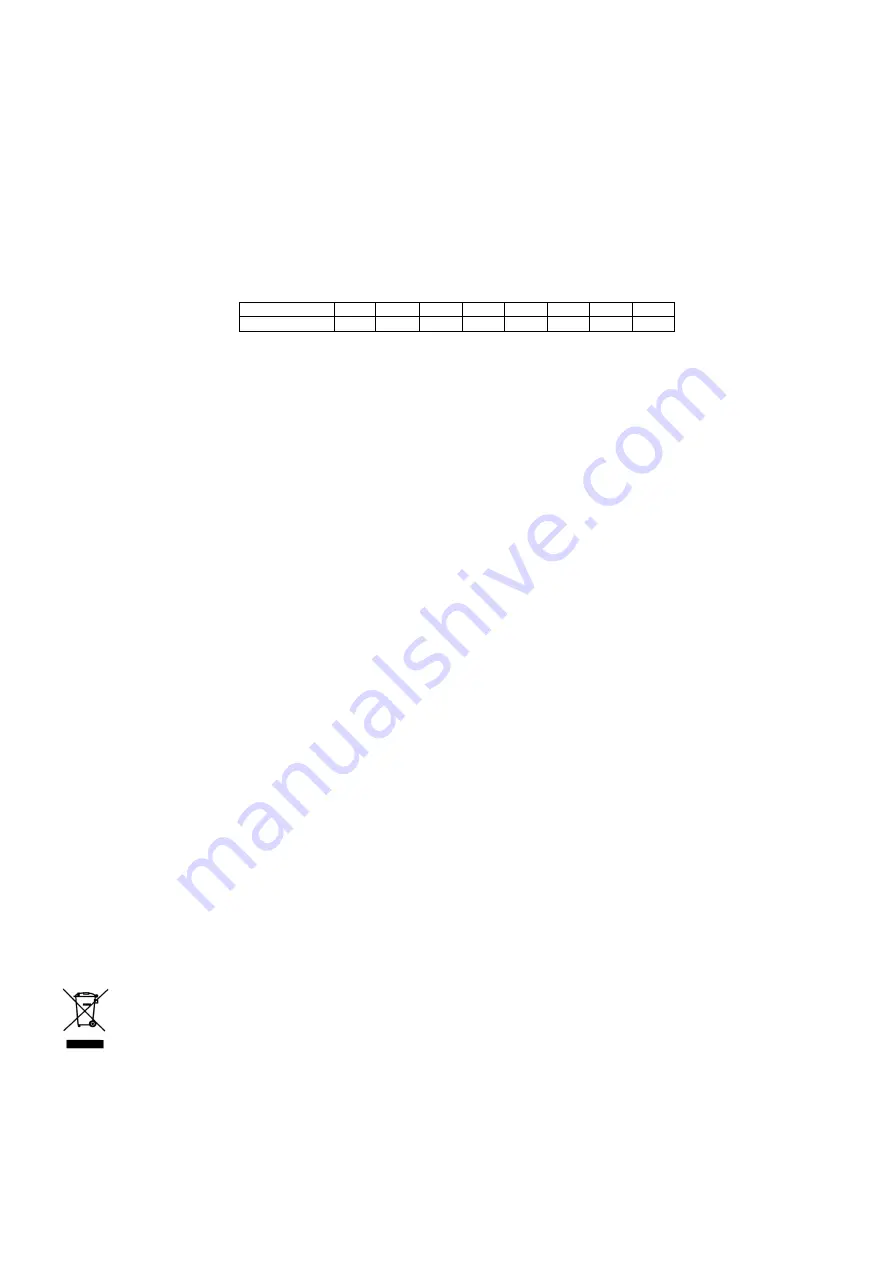
18
If the pump is equipped with WD detector and evaluation device is signalizing leakage into the mechanical
seal oil bath, is necessary to check the mechanical seal condition and eventually change mechanical seal and
pour new oil refill into chamber. Although it is not serious defect needs to quick switch off operation, but
mechanical seal must be changed as soon as possible, that will not worn-out upper couple of mechanical seal
and leakaging water into the motor.
At the pumps equipped with WD detector must be routine checked oil refill of mechanical seal chamber, when
already small volume of water in oil show on mechanical seal worn-out.
We recommend entrusting the checking or replacement of the oil refill to a service centre.
Take the pump out of the sump, clean it and submerge it at least for one hour into a disinfecting solution or
neutralizing agent. After that put the pump on a levelled base and check it.
7.2.1
The pump – Make sure that the bolts are tightened, check the conditions of the guide rail system (if being part
of the pump) and hanger, electric cable, terminal, and wear and tear of the impeller wheel.
When tightening the bolts, the following tightening torques must be applied:
Bolt
M8
M10
M12
M16
M20
M24
M30
M36
Moment [N.m]
12
25
40
90
175
300
500
700
7.2.2
Cutting device (GF) – check wear and tear range of the radial cutter and the cutter ring in the GF series. The
working edges of radial cutter and cutter ring must be sharp.
Otherwise there will be a clogging the pump. If
the cutting device is worn, it must be replaced. Inspection or replacement of the cutting equipment should be
entrusted to a service center.
7.2.3
Lubricant inspection – for pump power:
≤
0,75kW every 3000 working hours or 12 months (whichever comes first)
≥
1,5kW every 6000 working hours or 12 months (whichever comes first). Loosen the oil plug screw and check
the colour of lubricant. If lubricant looks unclear, change mechanical seal and lubricant immediately.
Lubricant change – for pump power:
≤
0,75kW ever 4500 working hours or 24 months (whichever comes first)
≥
1,5kW every 9000 working hours or 12 months (whichever comes first)
Oil level must reach about 10 mm under low edge of oil plug bore (measured in horizontal pump axis position
with oil plug bore in top).
Sealing faces of oil plug and the bore must be clean, and the gasket must be entire. Apply adhesive before re-
securing the iol plug screw to strengthen the screw against leakage.
It is recomanded to provide oil inspection or change in authorized local HCP service. Used oil – turbine oil ISO
WG 32.
7.2.4
Mechanical seal inspection – every 24 months. Abrasive wear of ring sealing faces is inspected.
Only qualified mechanics with proper tools and knowledge should be attempting to service this pump or
contact authorized local HCP service.
7.3
SERVICE, REPAIRS, SPARE PARTS
Any possible repairs and servicing in the guarantee period perform in an authorized service centre only. We
recommend entrusting also after-guarantee repairs to service centres.
All the spare parts used for repair must be original parts and any additional spare parts must be approved by
the importer.
7.4
SERVICE CENTRES
7.5
PUMP DISPOSAL
In operation or disposal of the equipment it is necessary to observe the respective national regulations on
environment and waste disposal. In case that the equipment will have to be scrapped, it is necessary to
proceed in the disposal thereof according to the differentiated waste rules, which means that differences in the
materials and their composition must be respected (e.g. metals, plastics, rubber etc.). When applying the rules
of the differentiated wastes it is necessary to contact specializes companies dealing with collection of these
materials while respecting the local rules and regulations in force.
8.0 CONTENT OF SHIPMENT
•
Pump assembled with cable and a packaging. Pump AS, AG, IC series with discharge branch (C52, B75,
A110) depend on size of pump.
•
Pump AS, AG, IC series with cca 10 m fire-hose (C52, B75) depend on pump size (with the exeption of
pump with A110 discharge branches and hose conections).