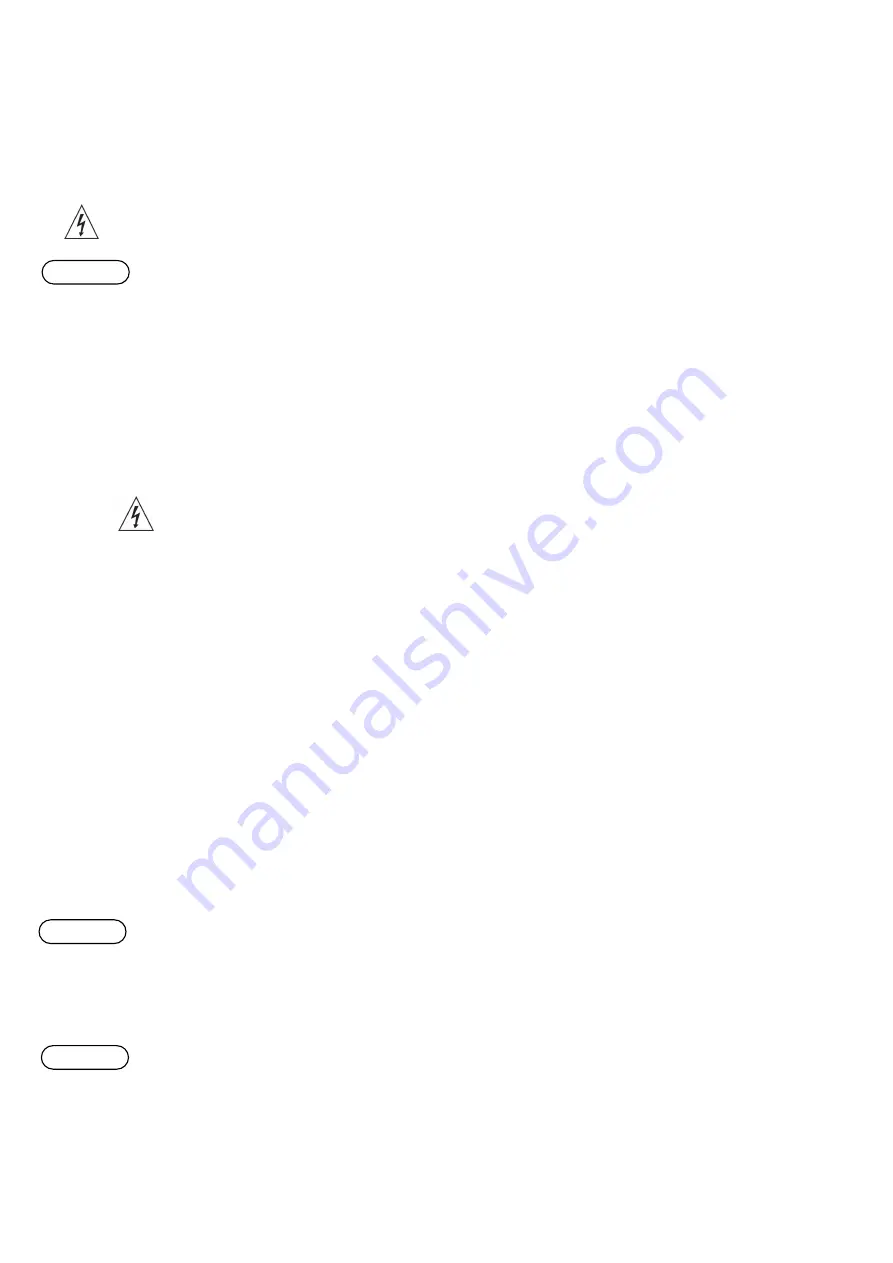
14
5.3
COMMISSIONING
Before commissioning it is necessary to carry out inspection of the electric part, particularly:
•
To check whether the pump supply cable, float switch or water detector cable is not damaged
•
To check the correct setting of the current protection
•
To check the protection against risky contact voltage
5.4
OPERATION AND MAINTENANCE OF ELECTRIC DEVICES
In any handling of the pump it is necessary to disconnect the pump from the power supply and to
make sure that the pump cannot be re-connected accidentally.
Submersible pump may not be carried if the electric motor is switched on.
Should a defect of electric equipment or the submersible pump be found during maintenance, the pump
must be switched off immediately and the defect must be reported to a person with electro-technical
qualification.
5.5
MAINTENANCE OF ELECTRIC DEVICES
In more frequent use the electric equipment must be checked at least 1x per month, in occasional use 1x per six
months and before any commissioning by a person having electro-technical qualification according to the
national standards and regulations in force.
It is necessary to check the protection against a risky contact voltage and integrity of supply cable or the pump.
Cable replacement and repairs of other parts of the pump where the sealing faces are being loosened must be
carried out by a service centre or repair shop as it is necessary to make sure that the sealing parts being
disassembled are waterproof tightened again.
Warning: Any works on the pump involving disassembly of the cable box enclosure, electric
connection, disconnection of the motor and replacement of the cable must be carried out by
an expert with an appropriate qualification observing the national standards and regulations
on connecting electric connections in force.
The supply cable MUST NOT be connected by ignorant and incompetent person.
6.0 PUMP OPERATION
6.1
GENERAL REQUIREMENTS
Before commissioning the pump it is necessary to make the operating personnel acquainted with the
instructions contained herein that are necessary for proper and safe operation. An emphasis is laid on the
necessity to observe this requirement as the product works in wet environment, which represents an extra risk
regarding the risk of injury by electric current.
6.2
PREPARING PUMP FOR COMMISSIONING, ASSEMBLY OF PUMP AND
GUIDE RAIL SYSTEM
6.2.1
After having the pump connected to the power supply it is necessary to verify the proper direction of rotation.
This can be done by putting a small pump (up to 1.1 kW) on the ground, tilting it a bit on a side (so that the
pump stands on the circumference edge of the frame), gripping by the handle and turning the motor on for a
moment. If the direction of rotation is wrong, proceed according to chapter 5.0 – electric connection. In case of
AL, AS, IC, SS, L pumps is necessary to remove strainer.
6.2.2
In case of big pumps you can check the direction of rotation as follows:
- Hang the pump on a rope or chain and turn the motor on for a moment.
- If the pump jerks opposite the direction of the "ROTATION" arrow placed on the pump box, the
direction of rotation is correct.
- If the pump jerks in the opposite direction, the direction of rotation is wrong and it is necessary to proceed
according to chapter 5.0 – electric connection. In case of big pumps the jerk can be very powerful.
6.2.3
Warning – the pump must be installed in vertical position ONLY. If the pump is installed in different position, it
is not possible to file a claim.
6.2.4
Is necessary to have free space arround pump equipped with float switch to ensure that float switch does not
catch on the sump surface or another things.
If the sump is small is possible to reduce free length of float switch in fixing point to pump handle. Reducion
free length of float switch cable changes switch-on and switch-off level – is necessary to check out.
Is necessary to fix the pump in sump against moving or rotating.
WARNING
WARNING
WARNING