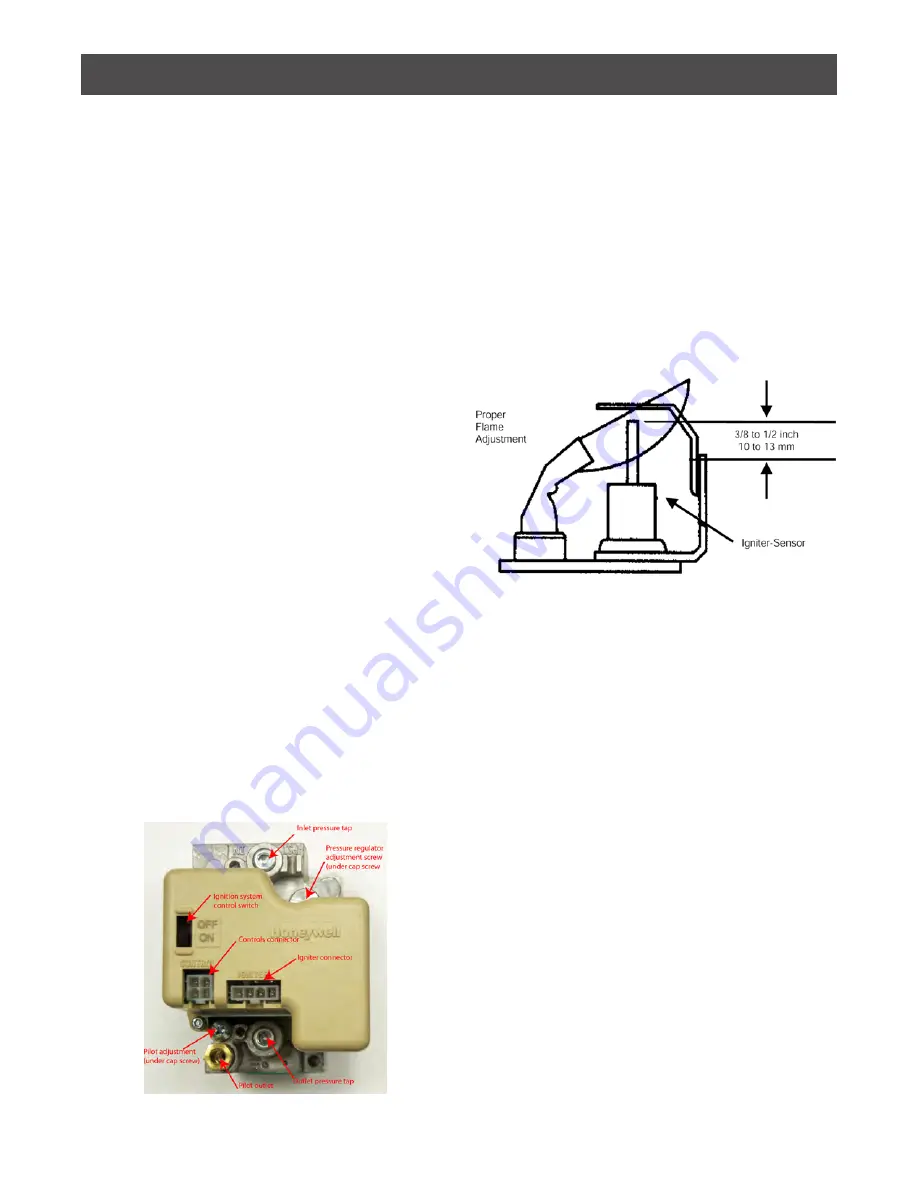
Section III: Service and Maintenance
Gas Control System
Fig. 3.3: SV9501 / 9502 Gas Control
When to Replace the Gas Control:
√ The gas control does not perform properly on checkout
or troubleshooting.
√ The gas control knob is hard to turn.
√ The gas control is likely to have operated more than
200,000 cycles.
√ The control is wet or looks as if it has been wet.
B) Adjusting the Pilot Flame
The pilot flame was adjusted at the factory. Should it ever
need adjusting, follow the instructions below.
Fig. 3.4: Pilot System for the SV9501/9502
SmartValve™ Gas Control
Proper Setting: The flame should envelope 3/8” to 1/2”
(10 mm to 13 mm) of the igniter sensor tip.
1. Turn off the thermostat dial.
2. Disconnect the lead to the MV terminal on the gas
control.
3. Re-light the pilot by turning up the thermostat to call
for heat.
4. Remove the pilot adjustment cover screw from the gas
control (see Fig. 3.3).
5. Turn the inner pilot adjustment screw clockwise to
decrease or counterclockwise to increase the pilot flame.
When done, replace the cover screw and tighten it firmly.
A). Maintenance of the Gas Control System
Your equipment came with an intermittent pilot gas
control system. The systems is as follows:
The SV9501/9502 SmartValve™ System Control combines
gas flow control and electronic intermittent pilot
sequencing functions into a single unit. The Q3450
SmartValve™ System pilot burner provides pilot flame
ignition and sensing for the SV9501/9502 Systems. It
consists of a replaceable igniter-flame rod assembly,
bracket assembly, pilot target, ground electrode, orifice
assembly, compression fitting and spring clip. The igniter
lights the pilot burner. The flame rod proves the pilot
flame and the pilot flame lights the main burner.
Control Knob Settings:
OFF.
Prevents pilot and main gas flow through the
ignition system control.
ON.
Permits gas flow into the control body and, under
control of the thermostat, to the pilot and main burners.
Frequency of Maintenance Required:
Cycling Frequency. Appliances that may cycle 20,000
times annually should be checked monthly.
Intermittent Use. Appliances that are used seasonally
should be checked before shutdown and again before
the next use.
Consequence of Unexpected Shutdown. Where the cost
of an unexpected shutdown would be high, the system
should be checked more often.
Dusty, Wet, or Corrosive Environment. Since these types
of environments can cause the gas control to deteriorate
more rapidly, the system should be checked more often.
16
Содержание EDGE ALTLGB
Страница 26: ...Section VI Parts List Actuator Parts List Assembly Fig 6 1 Actuator Assembly Diagram 24...
Страница 30: ...Wiring Diagram 120V 1PH 28...
Страница 31: ...Wiring Diagram 240V 1PH 29...