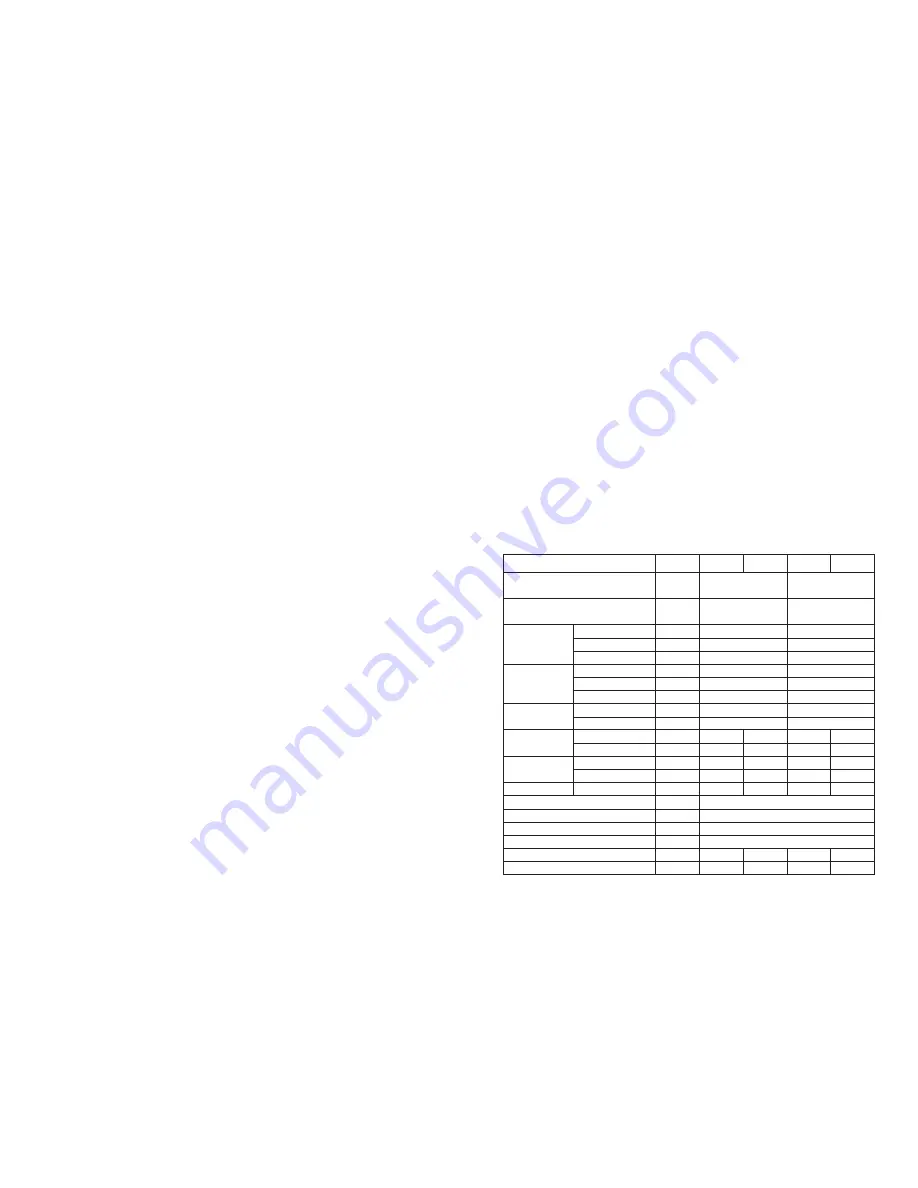
page 7
WARNING! It is important to verify that the
installation is in compliance with current
regulations and that it is approved, wherever
necessary, by the competent inspection
authorities.
1.8 THE USE OF DUCTS WITH THE WD
VERSION
The technical, functional, and aesthetic
characteristics of the W and WR air heaters
have been researched to achieve their optimal
use inside the rooms where heating is required.
The experience we have acquired in these types
of applications has resulted in further possible
solutions for the WD version, which was
specifically developed for installation on the
ceiling with ducts.
This version has a galvanized steel casing and
was designed to be connected to intake and
delivery ducts. Since the WD air heaters were
designed exclusively for installation on the ceiling,
they come complete with a remote-control panel.
This makes it possible to use a single unit to
serve several rooms or to install the air heater in
a separate room.
Typical examples of these situations could be:
- Efficiency apartments.
- Tourist accommodations, bungalows, etc.
- Doctors’ offices, offices.
- Bars, stores, etc., with the system installed in
a service room.
Using ducts to distribute the air provides a
solution that satisfies most current installation
requirements, with the distribution of the treated
air at a low noise level. However, it is advisable
to contact a qualified heating technician to
evaluate specific installation problems.
1.9 TECHNICAL DATA TABLE
Unit
W-WR 8
WD 8
W-WR 10
WD 10
Rated thermal capacity
kW
8,90
10,50
kcal/h
7.650
9.030
Rated thermal power
kW
8,05
9,50
kcal/h
6.900
8.150
Gas flow rate
G20 Methane
m³/h
0,94
1,11
(15 °C - 1.013 mbar)
G30 Butane
kg/h
0,70
0,83
G31 Propane
kg/h
0,69
0,81
Gas pressure
G20 p 20 mbars
mbar
14,5
12,0
at the burner
G30 p 28-30 mbars
mbar
27,0 - 29,0
27,0 - 29,0
(15 °C-1.013 mbars)
G31 p 37 mbars
mbar
36,0
36,0
Diameter of the
G20
mm/100
240
280
gas injector
G30 / G31
mm/100
150
170
Ventilation
Minimum speed
m³/h
720
750
850
900
air capacity
Maximum speed
m³/h
850
860
1.040
1.040
Noise level
Minimum speed
dBA
42
41,5
43
46,5
at 3 meters
Maximum speed
dBA
43
44,6
45,5
49
Effective pressure
Maximum speed
Pa
/
40
/
40
Gas supply diameter
in.
G 1/2 A
Flue gas discharge / air supply diam.
mm
60
Electric power supply
230 V ~ / 1 / 50 Hz
Fuse (rapid type)
A
2
Power absorbed
W
170
180
180
190
Net weight
kg
56
54
58
56
page 30
b) The ignition electrode is no longer connected
to the equipment connector.
-
Restore the connection or replace the
electrodes. Do not make any connections so
as to avoid reducing the cable insulation level.
c) The ignition electrode(s) is (are) not correctly
positioned or the ceramic insulation is
damaged, with a subsequent leakage of the
ignition discharge.
-
Replace the ignition electrode(s).
7.2.4 At the end of the preventilation phase,
the ignition discharge takes place, but
the flame does not ignite and the
control equipment shuts down within
the safety time
a) There is no gas supply or there is air inside
the piping.
-
Determine the reason why there is no gas
supply by first checking the on-off valves on
the delivery line. Completely bleed off any
residual air and restart the unit.
b) The gas solenoid valves do not open because
the coils are malfunctioning or their electrical
connection has been interrupted.
-
Check that the connection cable and the
corresponding terminals are in good condition.
Use a special tool to verify if the coils have
failed and replace them, if necessary (see
point 8.3).
c) The safety thermostat is malfunctioning and
does not allow the solenoid valves to open.
-
Replace the safety thermostat (see point
8.6).
7.2.5 At the end of the preventilation phase,
the ignition electrode sparks and the
flame ignites correctly, but the control
equipment shuts down within the safety
time
a) The phase-neutral electric power supply is
not correctly connected to the respective
terminals, marked as “L” and “N”, and
reversing the polarity may deactivate the
flame detection device.
-
Check using a multimeter or phase detector
and correctly connect the cables to the
corresponding terminals.
b) The flame detection electrode is not correctly
positioned and is not in contact with the flame.
-
Check if the electrode is properly connected
and if there are any deformations. Comply
with what is indicated in figure 30.
c) The flame detection electrode electric
connection has been interrupted.
-
Check the electrode connection to the control
equipment. If the cable or ceramic insulation is
damaged, replace the electrode in accordance
with the positions shown in figure 30.
7.2.6 The control equipment locks out during
normal operation
a) The gas supply was cut off and the equipment,
after repeating the ignition cycle, and without
detecting the flame within the safety time
period, entered the lock out mode.
-
Determine why the gas supply to the air
heater was interrupted. Restart the appliance
using the Reset button on the control panel.
b) The incorrect positioning of the external intake
and exhaust terminals has caused combustion
products to return and this prevents the flame
from igniting properly and from being detected
by the electrode.
-
Change the positions of the outside terminals,
keeping in mind that the exhaust terminal
must stick out farther than the intake terminal
(see fig. 19 and fig. 20). Check that the
terminals are not installed inside niches or
recesses in the walls and that there are no
obstructions that prevent the air from
circulating freely.
c) The safety thermostat cuts off the supply to
the gas solenoid valve because overheating
has occurred due to incorrect operation or a
failure of the convection fan(s).
-
Check for obstructions or dust deposits on the
filter and/or on the fan. Replace the
malfunctioning fan, if necessary (see point 8.9).
d) The safety thermostat cuts off the supply to
the gas solenoid valve because overheating
has occurred due to incorrect operation of the
fan control thermostat.
-
Replace the fan control thermostat (see point
8.5).
7.2.7 The burner stops while it is operating,
even though the room temperature does
not require it
a) The control panel’s room thermostat is
defective or the panel (in the versions to be
installed on the ceiling) is not correctly
positioned in the room to detect the tempera-
ture properly.
-
If you believe that the panel’s position is
correct, but there is still a defect, it will be
Содержание W
Страница 2: ......