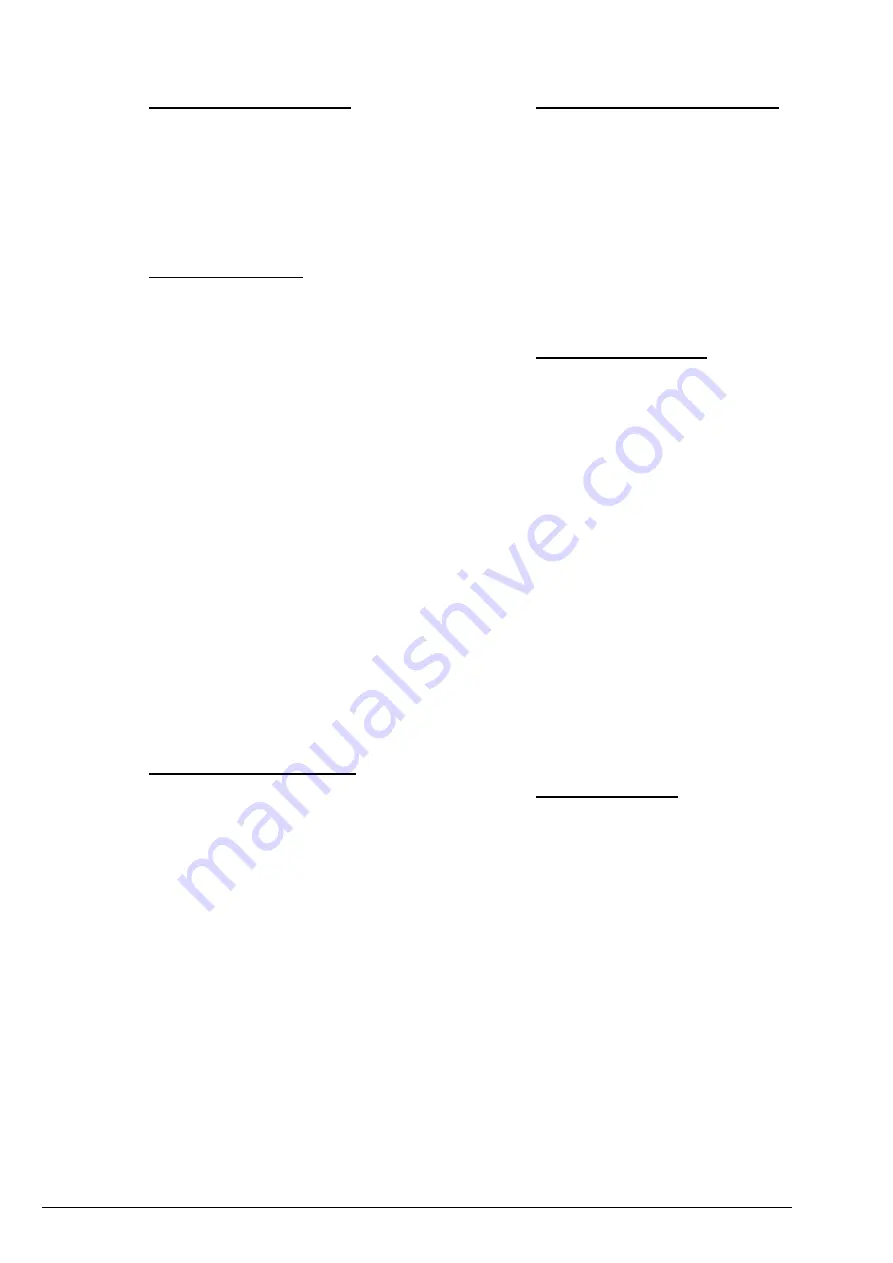
Page 16
Data : 01.03.2016
Parameter:
P 0.1
Load capacity of hoist
1
This parameter defines the load capacity of the hoist.
About 200 load capacity values are stored in the LIS–
SE, in steps of 100 kg up to a value of 10 t and in steps of
500 kg for values above 10 t.
Adjustment:
The rated load capacity of the hoist must always be ent-
ered.
Parameter:
P 1.1
Enter motor type
This parameter defines the motor data: the values in the
list ”Current measurement modules for GM hoists”
must be entered. The table only applies to the latest ge-
neration of ABUS motors, voltage range 380- 415 V,
star circuitry
Adjustment:
The value in the motor type column for the current ge-
neration of ABUS hoists must be entered.
In this case, it is not necessary to enter parameters P
1.2 and P 1.3. The unit sets these parameters automati-
cally as the values for current–generation hoists are
stored in the unit.
For older ABUS hoists, non–ABUS hoists and hoists
with a supply voltage other than 400 V, ”0” must be ent-
ered.
In this case, parameters P 1.2 and P 1.3 must also be
set.
In order to prevent unintentional deletion of the preset
data with motor type ”0”, the code must be entered be-
fore making any changes.
To enter the code, keep the
Enter
key pressed until
Code
appears on the display. After you have entered
the code number
1443
, the unit automatically switches
to parameter 1.2 and then to parameter 1.3, without in-
dicating the parameter number.
Parameter:
P 1.2
Enter winding resistance
This parameter defines the resistance (R) of the preci-
sion and main lift windings.
The resistance must be measured on the motor; the va-
lue required is the resistance in one phase. In the case
of motors with
delta circuits
, the equivalent star circuit
resistance must be entered.
Adjustment:
This parameter has two levels:
Level 1:
1. display of R (in Ohms) of precision lift winding
2. display of R (in Ohms) of main lift winding
Level 2: (can be accessed using CODE 1443)
1. entry of measured resistance (in Ohms) of preci-
sion lift winding
2. entry of measured resistance (in Ohms) of main lift
winding
Following the entry and verification of the resistance va-
lue, there may be a discrepancy between the value ent-
ered and the value displayed. This discrepancy is cau-
sed by processing in the computer but has no effect on
accuracy.
Parameter:
P 1.3
Enter current correction factor
This parameter defines the correction factor for the cur-
rent measurement modules.
The correction factor must be taken from the table ”cor-
rection factors for current measurement modules”.
Adjustment:
This parameter has two levels:
Level 1:
-
display of correction factor stored
Level 2: (can be accessed using CODE 1443)
-
entry of correction factor from table 1
Parameter:
P 2.1
Precision lift setting
This parameter can be used for reading stored values
and entering new values.
Input:
This parameter has two levels:
Level 1:
Last – 1 –
display empty hook load, precision lift
(zero load)
Po–r – 1 –
display empty hook power, precision lift
Last – 2
– display known load, precision lift
Po–r – 2 –
display known power, precision lift
Level 2: (CODE 1443 required for access)
Last – 1 –
enter empty hook load, precision lift (zero
load)
Po–r – 1 –
enter empty hook power, precision lift
Last – 2 –
enter known load, precision lift
Po–r – 2 –
enter known load power, precision lift
Last
= load on hook
Po–r
= rotating field power
– 1 –
= zero load on hook
– 2 –
= known load on hook
Parameter:
P 2.2
Main lift setting
This parameter can be selected for reading stored va-
lues and entering new values.
Input:
This parameter has two levels:
Level 1:
Last – 1 –
display empty hook load, main lift (zero
load)
Po–r – 1 –
display empty hook power, main lift
Last – 2 –
display known load, main lift
Po–r – 2 –
display known power, main lift
Level 2: (CODE 1443 required for access)
Last – 1 –
enter empty hook load, main lift (zero
load)
Po–r – 1 –
enter empty hook power, main lift
Last – 2 –
enter known load, main lift
Po–r – 2 –
enter known load power, main lift
Last
= load on hook
Po–r
= rotating field power
– 1 –
= zero load on hook
– 2 –
= known load on hook
Содержание LIS-SE
Страница 10: ...Page 10 Data 01 03 2016 Standard wiring diagram LIS SE with one hoist Figur 2...
Страница 11: ...Page 11 AN120076 000_EN Standard wiring diagram LIS SE with two hoists Figur 3 Katzumschaltung...
Страница 12: ...Page 12 Data 01 03 2016 Standard wiring diagram LIS SE with twin hoist Figur 4 schnell...