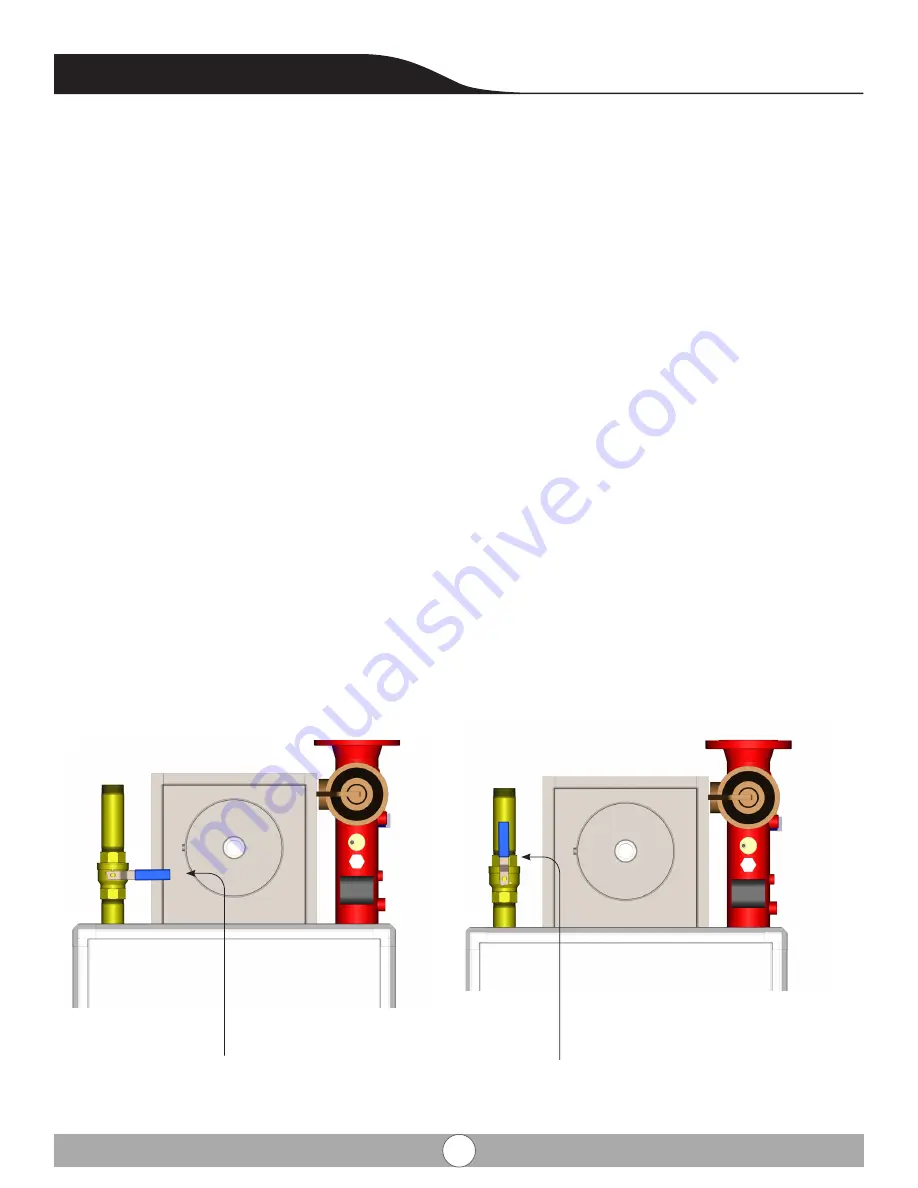
Absolute Boilers ABS 1500-2000-2500-3000-4000
50
6 Gas connection
6.1 Gas connection
The Absolute boiler is suitable for use with natural gas only. The gas connection is at the back left side of the boiler .
The boiler is fitted with a gas filter which is mounted within the mono block gas valve as standard to prevent dirt from
contaminating the gas valve or burner assembly. An isolating main gas valve must be installed in the vicinity of the
boiler, upstream of the automatic gas valve.
- A main gas shutoff valve must be connected to the 2 Inch NPT connection on the boiler, and must be readily
accessible and within hand reach.
-
When connecting the gas line ensure to use 2 sets of pipe wrenches to connect to the service. Do not apply the
tighten load to the gas line by itself, as damage can occur to the gas valve.
-
A sediment trap must be installed upstream of the main gas cocks shutoff valve.
-
The boiler fuel train does not require venting to the atmosphere, other regulators and safety shutoff valves may
require venting and relief piping to the atmosphere, consult their documentation.
-
Install a sediment trap (drip leg) and a union connection ahead of any primary manual shut off valve. Gas piping
should be installed in accordance with the National Fuel Gas code ANSI Z223.1 latest edition and any other local
codes which may apply; in Canada see CAN/CSA-B149.1, latest edition. In the commonwealth of Massachusetts,
the gas valve must be a T handle type
-
The boiler and gas line piping connection should be pressure tested and must be checked for leaks before being
placed in service. Test with inert gas or compressed air.
-
The boiler must be disconnected at the boiler manual shut off valve (located at the rear of the boiler) during any
pressure testing of the system at pressures in excess of 1/2 PSI, (14 inches W.C.)
-
Use of soap and water can cause corrosion of metallic parts, ensure these compounds are rinsed and wiped off
after testing.
6.1.2 Manual gas valve upstream of boiler
(The manual valves supplied by others)
Gas valve in open position
Gas valve in close position