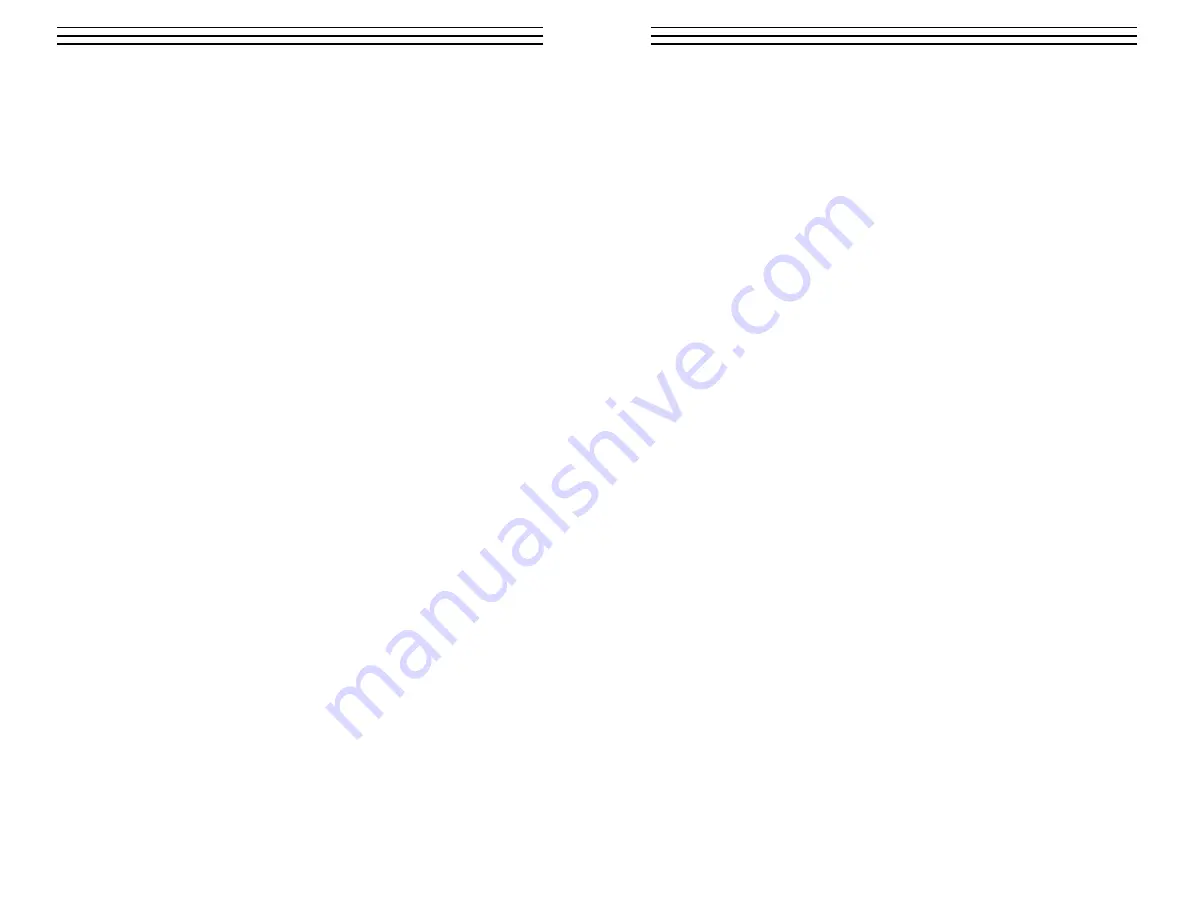
– 10 –
4.1 Condition and Preparation of Surfaces
In any ultrasonic measurement scenario, the shape and roughness of the test sur-
face are of paramount importance. Rough, uneven surfaces may limit the penetra-
tion of ultrasound through the material, and result in unstable, and therefore unre-
liable, measurements. The surface being measured should be clean, and free of
any small particulate matter, rust, or scale. The presence of such obstructions will
prevent the transducer from seating properly against the surface. Often, a wire
brush or scraper will be helpful in cleaning surfaces. In more extreme cases,
rotary sanders or grinding wheels may be used, though care must be taken to pre-
vent surface gouging, which will inhibit proper transducer coupling.
Extremely rough surfaces, such as the pebble-like finish of some cast iron, will
prove most difficult to measure. These kinds of surfaces act on the sound beam
like frosted glass on light:, the beam becomes diffused and scattered in all direc-
tions.
In addition to posing obstacles to measurement, rough surfaces contribute to
excessive wear of the transducer, particularly in situations where the transducer is
“scrubbed” along the surface. Transducers should be inspected on a regular basis,
for signs of uneven wear of the wearface. If the wearface is worn on one side
more than another, the sound beam penetrating the test material may no longer be
perpendicular to the material surface. In this case, it will be difficult to exactly
locate tiny irregularities in the material being measured, as the focus of the sound-
beam no longer lies directly beneath the transducer.
4.2 Probe Zero
Setting the Zero Point of the TI-25M-MMX is important for the same reason that
setting the zero on a mechanical micrometer is important. If the gauge is not
“zeroed” correctly, all of the measurements the gauge makes will be in error by
some fixed number. When the TI-25M-MMX is “zeroed”, this fixed error value is
measured and automatically corrected for in all subsequent measurements. The
TI-25M-MMX may be “zeroed” by performing the following procedure:
Performing a Probe-Zero
1. Make sure the TI-25M-MMX is on.
2. Plug the transducer into the TI-25M-MMX. Make sure that the connectors
are fully engaged. Check that the wearface of the transducer is clean and free
of any debris.
3. The metal probe-disc is on the top end of the TI-25M-MMX. Apply a single
droplet of ultrasonic couplant to the face of this disc.
4. Make sure that the TI-25M-MMX is in P-E ( pulse-echo mode) by pressing the
Dual-Multi key to toggle the modes.
Note
: The Probe-Zero feature is not used in Echo-Echo Thru-Paint mode, and
has been disabled. If the PRB-0 key is pressed, while in this mode, “nO”
followed by “Prb0” will be displayed
– 19 –
1 0 .0 T RAN SDU CER SELECT I ON
The TI-25M-MMX is inherently capable of performing measurements on a wide
range of materials, from various metals to glass and plastics. Different types of
material, however, will require the use of different transducers. Choosing the
correct transducer for a job is critical to being able to easily perform accurate
and reliable measurements. The following paragraphs highlight the important
properties of transducers, which should be considered when selecting a transducer
for a specific job.
Generally speaking, the best transducer for a job is one that sends sufficient
ultrasonic energy into the material being measured such that a strong, stable echo
is received by the TI-25M-MMX. Several factors affect the strength of ultrasound
as it travels. These are outlined below:
10.1 Initial Signal Strength
The stronger a signal is to begin with, the stronger its return echo will be. Initial
signal strength is largely a factor of the size of the ultrasound emitter in the trans-
ducer. A large emitting area will send more energy into the material being meas-
ured than a small emitting area. Thus, a so-called “1/2-inch” transducer will emit
a stronger signal than a “1/4-inch” transducer.
10.2 Absorption and Scattering
As ultrasound travels through any material, it is partly absorbed. If the material
through which the sound travels has any grain structure, the sound waves will
experience scattering. Both of these effects reduce the strength of the waves, and
thus, the TI-25M-MMX’s ability to detect the returning echo.
Higher frequency ultrasound is absorbed and scattered more than ultrasound of a
lower frequency. While it may seem that using a lower frequency transducer
might be better in every instance, low frequencies are less directional than high
frequencies. Thus, a higher frequency transducer would be a better choice for
detecting the exact location of small pits or flaws in the material being measured.
10.3 Geometry of the Transducer
The physical constraints of the measuring environment sometimes determine a
transducer’s suitability for a given job. Some transducers may simply be too large
to be used in tightly confined areas. Also, the surface area available for contacting
with the transducer may be limited, requiring the use of a transducer with a small
wearface. Measuring on a curved surface, such as an engine cylinder wall, may
require the use of a transducer with a matching curved wearface.