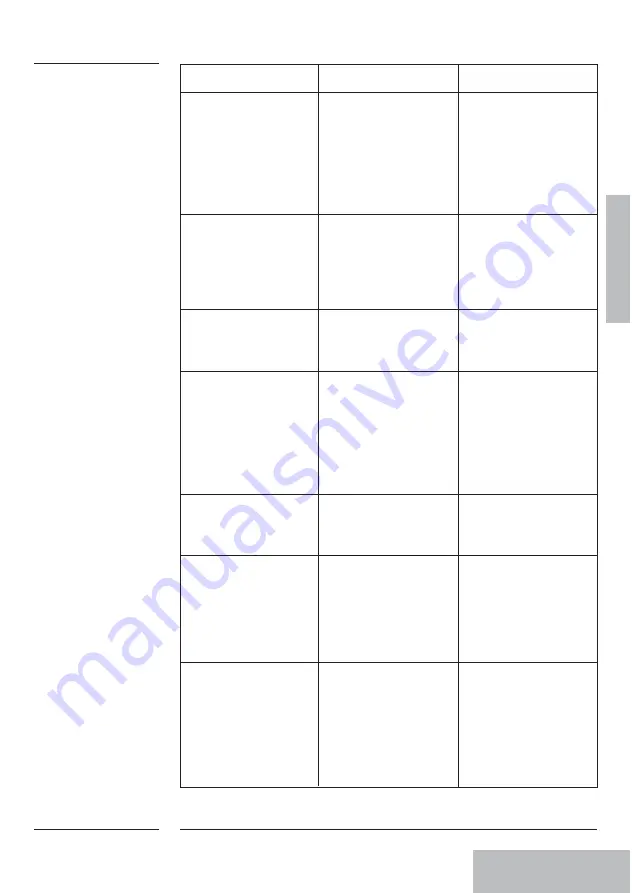
29
English
Problem
Torch becomes too hot.
No switch function.
Wire burnt-back in the
contact tip.
Irregular wire feed.
Short arc between the
gas nozzle an the
workpice.
Variable arc.
Porous Welds.
Cause
• Contact tip/ collet chuck
not tight enough.
• Current connection on
the torch side and to
the workpiece are
loose.
• Too little coolant flow.
• Control line interrupted/
faulty.
• Flow control instrument
in the circulating coo-
ling unit has triggered.
• False parameter setting.
• Worn contact tip.
• Liner blocked.
• Contact tip and wire
diameter do not match
• Wrong pressure set on
the wire feeding unit.
• Spatter bridge between
the contact tip and the
gas nozzle.
• Contact tip does not
match the wire diameter
or the contact tip is worn.
• False welding
parameters.
• Liner worn.
• Large amount of spatter
in the gas nozzle.
• Insufficient or total lack
of gas shield.
• Draught is disturbing
the shield gas.
Solution
– Check and tighten.
– Check and tighten.
– Check coolant system.
– Check / Repair
– Check level of coolant
and fill up if necessary.
– Check or correct
setting.
– Replace!
– Blow through in both
directions.
– Replace contact tip.
– Correct according to
manufacturers instruc-
tions.
– Clean and spray the insi-
de of the gas nozzle.
– Check and replace
contact tip.
– Correct welding
parameters.
– Replace wire guide.
– Clean the gas nozzle.
– Check contents of the
gas cylinder and the
pressure setting.
– Shield welding area with
protective walls.
12. Troubleshooting
(continuation)
Содержание ABIMIG
Страница 59: ...59 Español ...