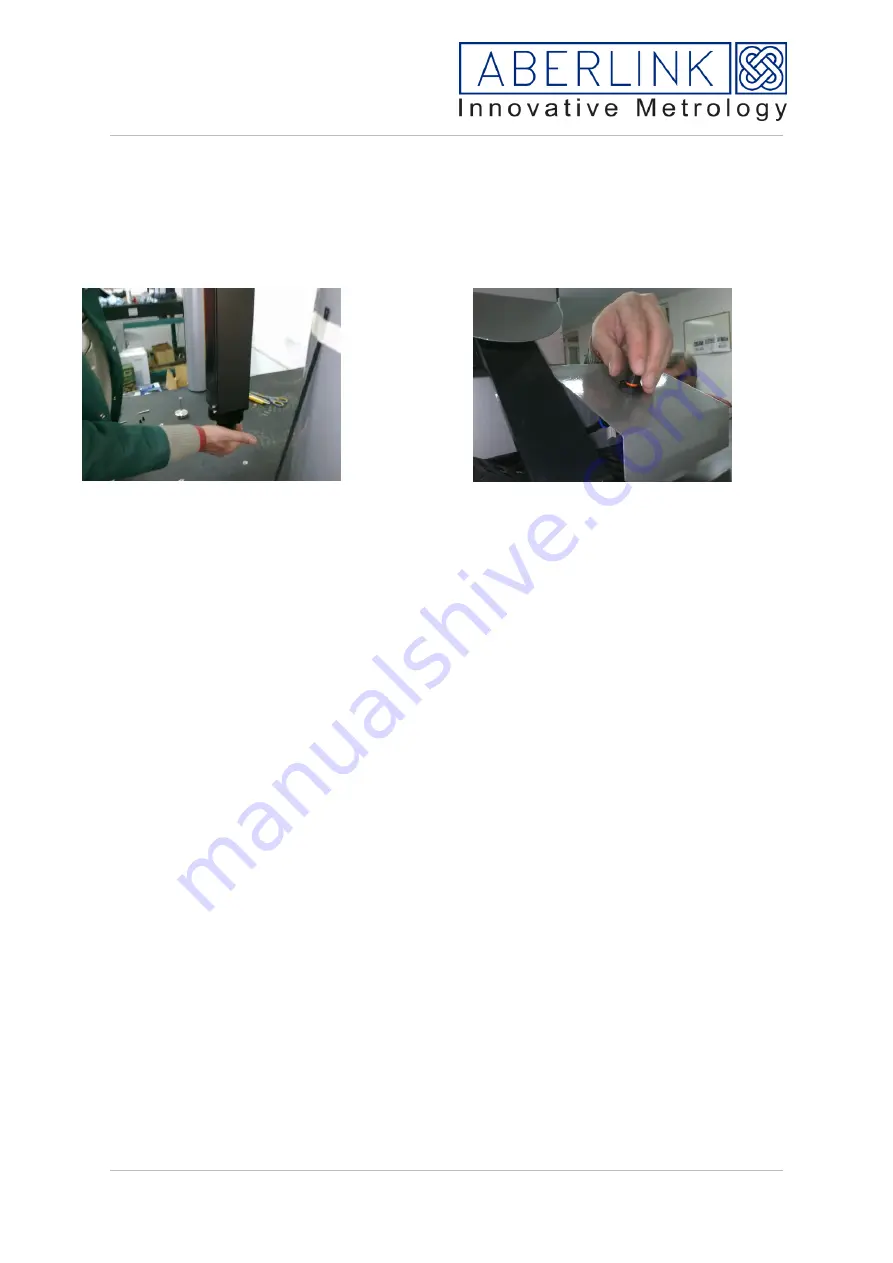
ABERLINK LTD
|
VATCH LANE
|
EASTCOMBE
|
GLOUCESTERSHIRE
|
GL6 7DY
|
UK
Tel : +44 (0)1453 884461
|
Fax : +44 (0)1453 882348
|
Email : [email protected]
|
Web : www.aberlink.com
Registered in England No. 7642245
|
VAT Registration No. GB 108 3075 37
5. Check the z balance, and adjust regulator at the back of machine (side of
bench) as necessary. Push Z to the top and check nothing is fouling. Fit back
of Z cover.
6.
Move each axis in turn and check the readheads are green for the entire travel and
that the light blicks when it passes over the reference mark (CNC).
6a.
Fit the Carriage front cover.
7.
Also check movement is ok, in terms of belts / drive rods and airbearings. If Y
floating ok, attach the Y axis belt (newer models will have a very simple belt
tensioner, use the nut to lock in position once belt is tensioned. See pic at end of
this document.
8.
Close loop on X, and datum axis.
9.
Check datum position is correct by open loop and pushing axis to the end stop and
checking position, should be within 1mm, edit axis.cfg (DATUM=) if incorrect.
10.
Set KI=0, in the PID tab, APPLY EDITS
11.
Close loop and set position 1 to
–200 and position 2 to –400. Set speed to 80 and
click on Single. Remove amp plate and adjust pot 3 (lag) for the x axis, bring lag to
within 0.004
12.
Apply a cycle move, and monitor the scale needle. Adjust pot 4 (speed) if
necessary.
13.
Check the graph for vibration or lack of dynamics, use KV and KD to best improve
graph.
14.
Set position 1 to
–100 and position 2 to –600 and speed to 250, and check no
stalling occurs, if so check mechanics of drive assembly.
15.
Set position 1 to
–500 and position 2 to –510 and speed to 5 and cycle, this
represents a probing move, and this must be stable. Use pot 1 (damping) to
improve. Reduce the amplitude of the red motion graph.
16.
Repeat for y and z, although check the maximum travel for your high speed move.
16a. Fit the Y axis cover
17.
Transfer edits from tuner into axis.cfg (c:\windows) and save.
18.
Close tuner, and open Aberlink software
19.
Reference machine.
20.
Teach ref ball
(separate document)
21.
Set RTP if necessary
(separate document)
22.
Set MCR change rack position.
(separate document)