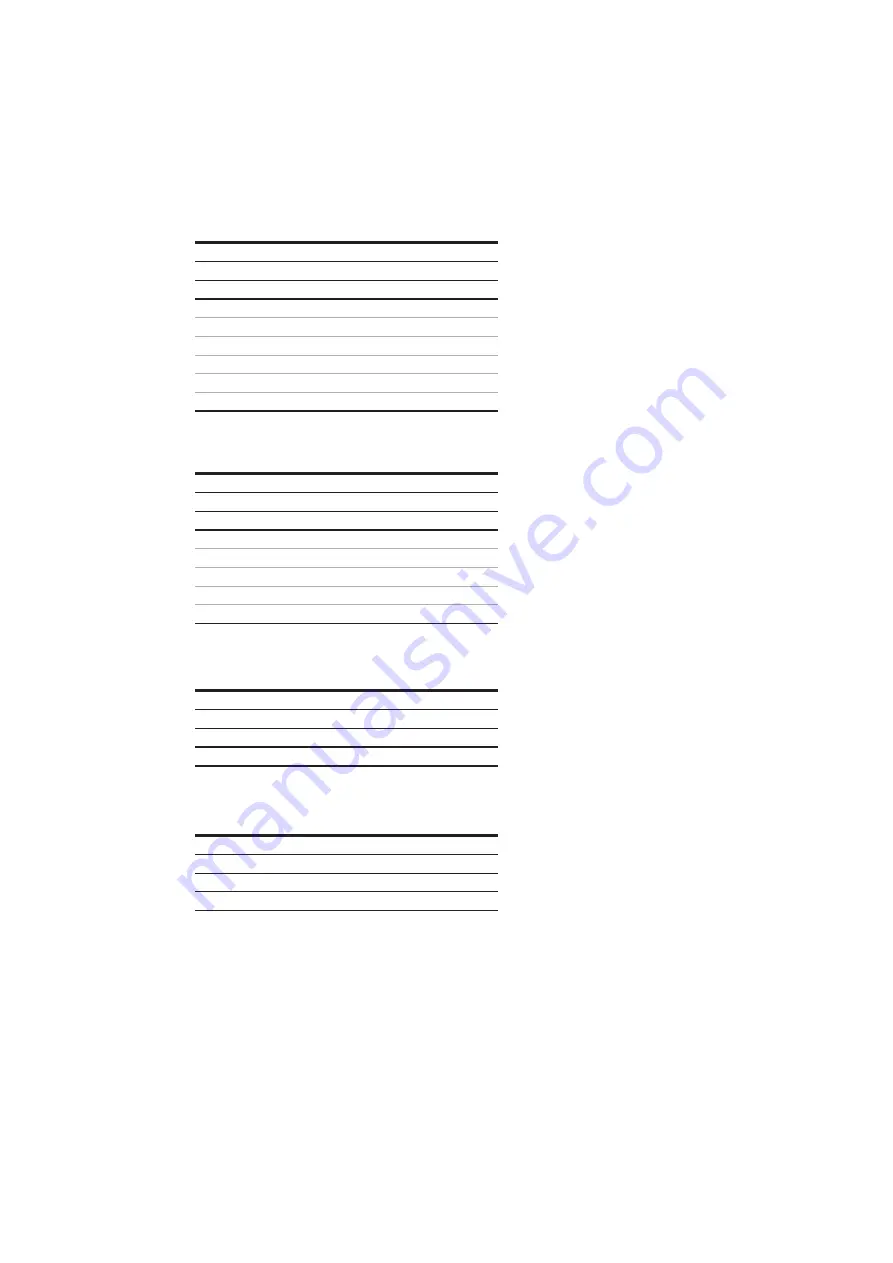
27
A S S E M B L Y O F T H E S W I T C H G E A R O N S I T E
5.3 Assembly of the switchgear panels
Use screws of tensile class 8.8. The maximum
recommended tightening torques based on type
of connection are given in the following tables.
The tightening torques for copper bars or
busbars connections together.
The tightening torques for copper bar
connections combined with epoxy insulators.
The tightening torques for copper bar
connections combined with ABB CTs.
The tightening torques for copper bar or cable
connections combined with ABB VTs.
Any tightening torques that deviate from those
in the general tables (e.g. for contact systems or
device terminals) must be taken into account as
stated in the detailed technical documentation.
It is recommended that the threads and head
contact surfaces of bolts should be lightly oiled
or greased so as to achieve the precise rated
tightening torque.
The individual installation stages are as follows:
•
Remove the withdrawable parts from the
switchgear panels and store them with suitable
protection
•
Dismantle the lifting eyebolts
•
Transport the switchgear panels to the prepared
installation point, following the sequence shown
on the switchgear plan
•
Remove the vertical partitions in front of the
busbar compartments by releasing the fixing
screws
•
Release the fixing screws and draw out the
horizontal partition below the withdrawable
part travel rails
•
Release and remove the floor cover
•
Remove the covers from the vertical control
wiring ducts, positioned on the right- hand
left-hand sides of the panel front
Fit and screw down the lids.
•
Correctly position and vertically align the
switchgear panels along the floor frame - the
panel edges must not deviate by more than 2
mm from the vertical, especially at the front -
and bolt the panels together. It is advisable to
start from the centre when assembling
switchgears with more than ten panels
•
When the switchgear has been properly
assembled, fix the panels to the concrete floor
using plugs, or weld or adequately bolt them
to the foundation frame
Thread
3)
M5
4)
M6
4)
M8
M10
M12
M16
-
-
-
-
-
-
-
8
20
40
69
170
Maximum recommended tightening torque
1)
Nm
Lubricant
2)
Without (η=0,14)
Oil or grease (η=0,10)
Thread
3)
M8
M10
M12
M16
M20
15
32
45
110
220
-
-
-
-
-
Maximum recommended tightening torque
1)
Nm
Lubricant
2)
Without (η=0,14)
Oil or grease (η=0,10)
Thread
3)
M12
70
-
Maximum recommended tightening torque
1)
Nm
Lubricant
2)
Without (η=0,14)
Oil or grease (η=0,10)
Thread
3)
M10
20
-
Maximum recommended tightening torque
1)
Nm
Lubricant
2)
Without (η=0,14)
Oil or grease (η=0,10)
1) The recommended maximum tightening torques are based on a
coefficient of friction for the thread of 0.14 (without lubrication) or
0.10 (with lubrication).
2) Thread and head contact surface lubricated.
3) The tightening torques are recommended for screws ISO 4014-4018
and ISO 4762 (tensile class 8.8). In case of usage of other types of
screws contact please ABB for clarification.
4) Applicable only for fixing of subsidiary covers or terminal connections.