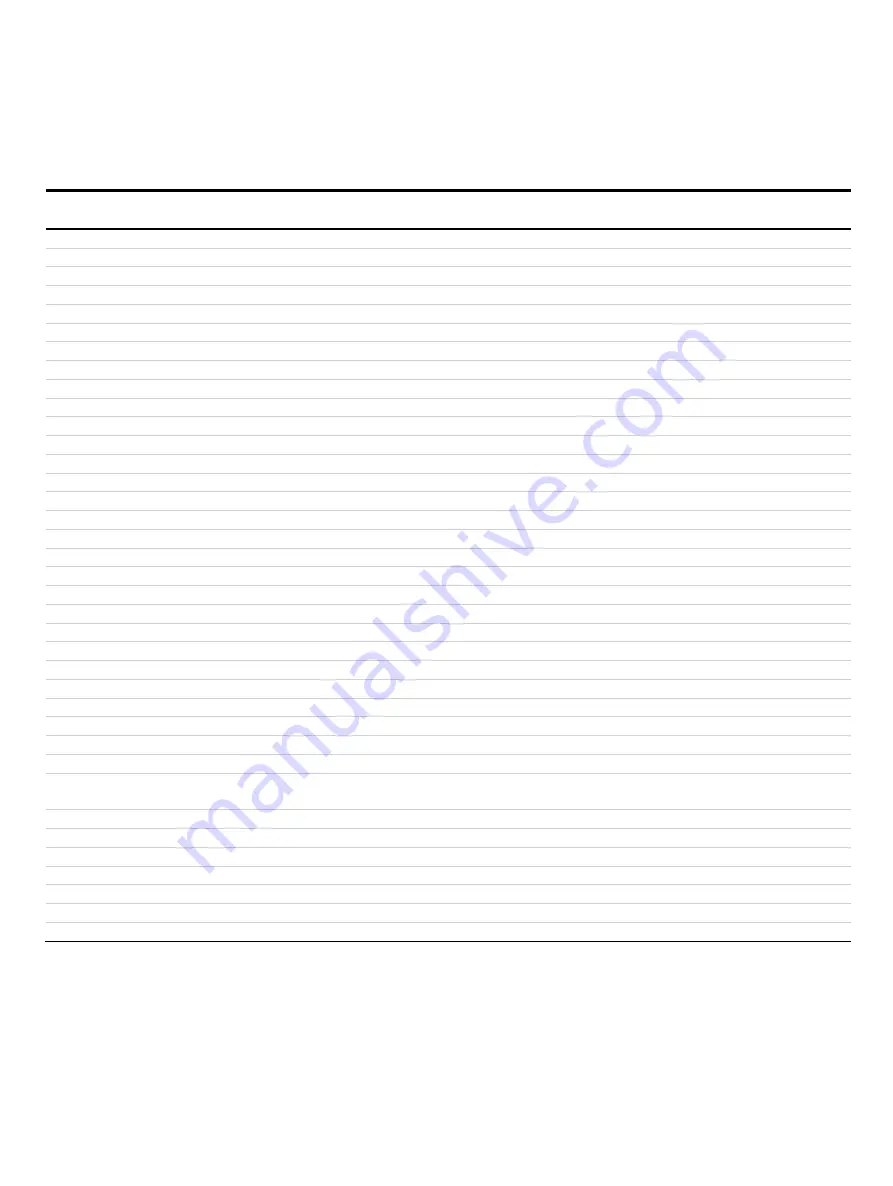
58
TZIDC-210, TZIDC-220
DIGITAL POSITIONER | OI/TZIDC-210/TZIDC-220-EN REV. G
… 10 Operation
… Parameter overview
Parameter descriptions
Para-
meter
Display
Function
Possible parameter setting
Unit
Factory setting
P1._
STANDARD
P1.0
ACTUATOR
Actuator type
Actuator type
LINEAR, ROTARY
---
LINEAR
P1.1
AUTO_ADJ
Automatic adjustment
Autoadjust
Function
---
---
P1.2
TOL_BAND
Tolerance band
Tolerance band
0.30 bis 10.00
%
0.30
P1.3
DEADBAND
DEAD BAND
Dead band
0.10 bis 10.00
%
0.10
P1.4
TEST
Test
Test
Function
---
---
P1.5*
ADRESS
Bus address
1 bis 126
---
126
P1.6
EXIT
Return
Return to operating level
Function
---
---
P2._
SETPOINT
P2.0
---
---
P2.1
---
---
P2.2
CHARACT
Charact. curve
Characteristic curve
LINEAR, 1:25, 1:50, 25:1, 50:1, USERD
---
LINEAR
P2.3
ACTION
Valve action
Direction of action
DIRECT, REVERSE
---
DIRECT
P2.4
SHUT_CLS
Shut-off value 0%
Shut-off value 0 %
OFF, 0.1 to 45.0
%
OFF
P2.5
RAMP UP
Set point ramp, up
Setpoint ramp (up)
0.1 to 999.9
sec
OFF
P2.6
RAMP DN
Set point ramp, down
Setpoint ramp (down)
0.1 to 999.9
sec
OFF
P2.7
SHUT_OPN
Shut off value 100%
Shut-off value 100%
OFF, 80.0 to 100
%
OFF
P2.8
EXIT
Return
Return to operating level
Function
---
---
P3._
ACTUATOR
P3.0
MIN_RGE
Min. of stroke range
Operating range, min.
0.0 to 100.0
%
0.0
P3.1
MAX_RGE
Max. of stroke range
Operating range, max.
0.0 to 100.0
%
100
P3.2
ZERO_POS
Zero position
Zero position
CLOCKWISE, CTCLOCKWISE
---
CTCLOCKWISE
P3.3
EXIT
Return
Return to operating level
Function
---
---
P4._, P5._
---
---
P6._
MAN_ADJ
P6.0
MIN_VR
Min. valve range
Operating range, min.
0.0 to 100.0
%
0
P6.1
MAX_VR
Max. valve range
Operating range, max.
0.0 to 100.0
%
100
P6.2
ACTUATOR
Actuator type
Actuator type
LINEAR, ROTARY
---
LINEAR
P6.3
SPRNG_Y2
Spring action (Y2)
Spring action (Y2)
CLOCKWISE, CTCLOCKWISE
---
CTCLOCKWISE
P6.4
ADJ_MODE
Auto adjust mode
Dead angle 0 %
FULL, STROKE, CTRL_PAR,
ZERO_POS, LOCKED
---
FULL
P6.5
EXIT
Return
Return to operating level
Function
---
NV_SAVE
P7._
CTRL_PAR
P7.0
KP UP
KP value, up
KP value (up)
1.0 to 100.0
---
1.0
P7.1
KP DN
KP value, down
KP value (down)
1.0 to 100.0
---
1.0
P7.2
TV UP
TV value, up
TV value (up)
0 to 1000
msec 100
P7.3
TV DN
TV value, down
TV value (down)
0 to 1000
msec 100
P7.4
GOPULS UP
Go pulse, up
0 to 200
msec 0
Содержание TZIDC-210
Страница 31: ...TZIDC 210 TZIDC 220 DIGITAL POSITIONER OI TZIDC 210 TZIDC 220 EN REV G 31 Page 2 of 5 ...
Страница 33: ...TZIDC 210 TZIDC 220 DIGITAL POSITIONER OI TZIDC 210 TZIDC 220 EN REV G 33 Page 4 of 5 ...
Страница 66: ...66 TZIDC 210 TZIDC 220 DIGITAL POSITIONER OI TZIDC 210 TZIDC 220 EN REV G Notes ...
Страница 67: ...TZIDC 210 TZIDC 220 DIGITAL POSITIONER OI TZIDC 210 TZIDC 220 EN REV G 67 Notes ...