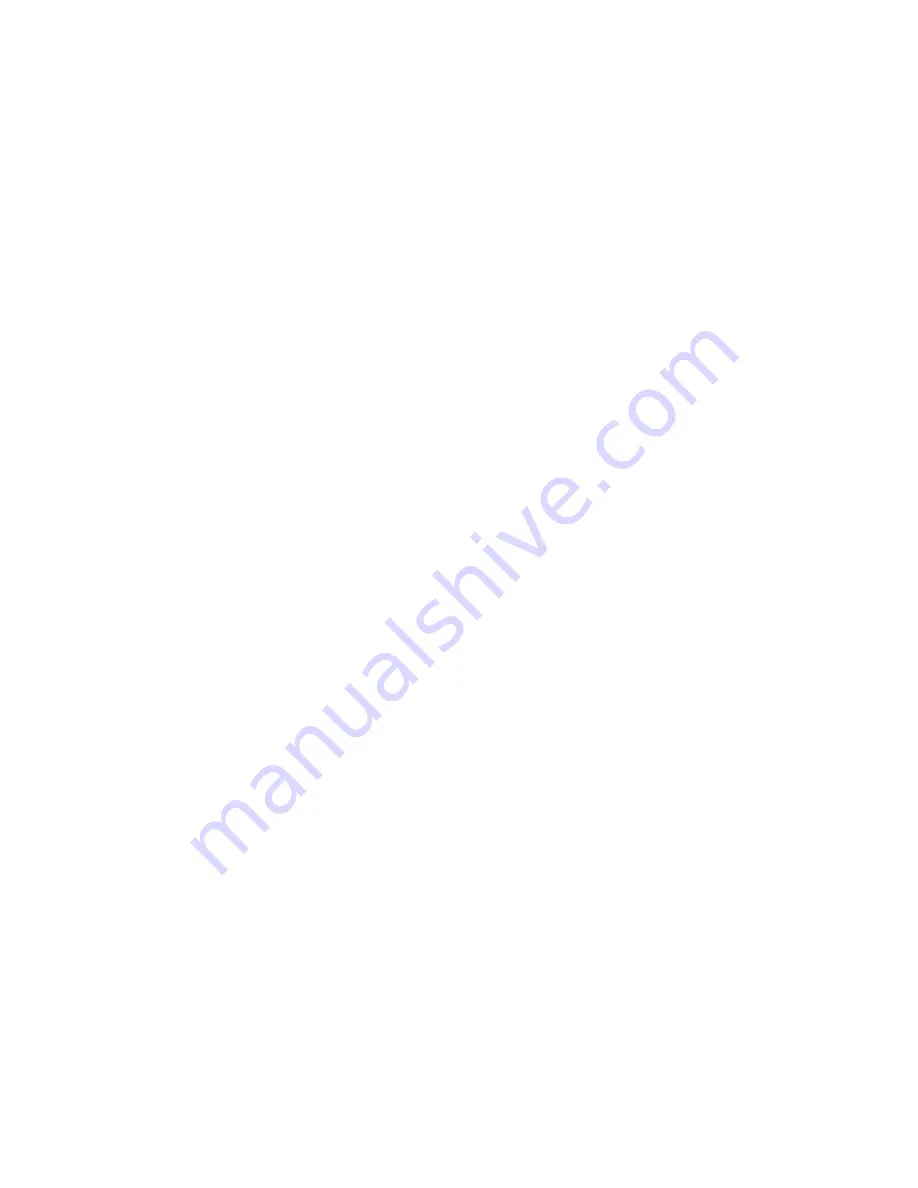
7
Replacement of Parts
NOTE: Using tools normally found in a maintenance
department, a Dodge Torque-Arm speed reducer can be
disassembled and reassembled by careful attention to the
instructions following.
Cleanliness is very important to prevent the introduction of
dirt into the bearings and other parts of the reducer. A tank
of clean solvent, an arbor press, and equipment for heating
bearings and gears (for shrinking these parts on shafts) should
be available.
The oil seals are contact lip seals. Considerable care should be
used during disassembly and reassembly to avoid damage to
the surface on which the seals rub.
The keyseat in the input shaft, as well as any sharp edges on
the output hub should be covered with tape or paper before
disassembly or reassembly. Also, be careful to remove any
burrs or nicks on surfaces of the input shaft or output hub
before disassembly or reassembly.
Ordering Parts
:
When ordering parts for reducer, specify reducer size number,
reducer model number, part name, part number, and quantity.
It is strongly recommended that, when a pinion or gear is
replaced, the mating pinion or gear also be replaced.
If the large gear on the output hub must be replaced, it is
recommended that an output hub assembly consisting of a gear
assembled on a hub be ordered to ensure undamaged surfaces
on the output hub where the output seals rub. However, if it is
desired to use the old output hub, press the gear and bearing
off and examine the rubbing surface under the oil seal carefully
for possible scratching or other damage resulting from the
pressing operation. To prevent oil leakage at the shaft oil seals,
the smooth surface of the output hub must not be damaged.
If any parts must be pressed from a shaft or from the output
hub, this should be done before ordering parts to make sure
that none of the bearings or other parts are damaged in
removal. Do not press against rollers or cage of any bearing.
Because old shaft oil seals may be damaged in disassembly, it
is advisable to order replacements for these parts.
Removing Reducer from Shaft
:
WARNING: To ensure that drive is not unexpectedly
started, turn off and lock out or tag power source before
proceeding. Remove all external loads from drive before
removing or servicing drive or accessories. Support
reducer by external means before removing from shaft.
Failure to observe these precautions could result in bodily
injury.
Straight Bore
:
Loosen screws in both output hub collars. Remove the collar
next to end of shaft. This exposes three puller holes in output
hub to permit use of wheel puller. In removing reducer from
shaft be careful not to damage ends of hub.
Taper Bushed
:
1. Disconnect and remove belt guard, v-drive, and motor
mount as required. Disconnect torque arm rod from
reducer adapter.
2. Remove bushing screws.
3. Place the screws in the threaded holes provided in the
bushing flanges. Tighten the screws alternately and
evenly until the bushings are free on the shaft. For ease of
tightening screws, make sure screw threads and threaded
holes in bushing flanges are clean. A tap can be used to
clean out the threads. Use caution to use the proper size
tap to prevent damage to the threads.
4. Remove the outside bushing, the reducer, and then the
inboard bushing.
Disassembly
:
1. Drain all oil from the reducer.
2. Position reducer on its side and remove all housing bolts.
Gently tap the output hub and input shaft with a soft
hammer (rawhide not a lead hammer) to separate the
housing halves. Open housing evenly to prevent damage to
the parts inside.
3. Lift input shaft, all gear assemblies, and bearing
assemblies from housing.
4. Remove seals from housing.
Reassembly
:
1. Output Hub Assembly:
Heat gear to 325°F to 350°F to
shrink onto hub. Heat bearings to 270°F to 290°F to shrink
onto hub. Any injury to the hub surfaces where the oil seals
rub will cause leakage, making it necessary to use a new
hub.
2. Input Shaft Assembly:
Heat bearing cones to 270°F to
290°F to shrink on shaft.
3. Place a .010” shim on output hub seal carrier, countershaft
cover and backstop carrier for right-hand half of housing
(as viewed in drawing). Place a 1/8” diameter bead of Dow
Corning RTV732 sealant on the face around the I.D. of the
shim (seal is to be between reducer housing and shim).
Caution: If too much sealant is used it will run into bearing,
and too little sealant will result in an ineffective seal. Install
right-hand carriers and cover in housing half and torque
screws to torque values in Table 5. Place bearing cups in
right-hand housing half. Make certain the cups are properly
seated in housing and are pressed against carriers and
cover. Place housing half on blocks to allow for protruding
end of output hub.
4. Mesh output hub assembly and input assembly together
and place in housing half. Tap lightly with a soft hammer
(rawhide not a lead hammer) until bearings are properly
seated in the housing.
5. Place a 1/8” diagonal bead of Dow Corning RTV732
sealant on the flange of the housing half. Place other half of
housing (without covers or carriers installed), insert dowel
pins, and draw together evenly to prevent damage to parts.
The final torque should be per Table 5.
6. Place output bearing cup in housing and tap in place.
Install output sear carrier and draw down with two (2) bolts
180° apart to 50 inch-pounds of torque. Loosen bolts and
retighten finger tight. Measure clearance between housing
and carrier flange at each bolt and average. Add .010 to
average and make up shim pack. Install shim pack and
torque down all seal carrier bolts to 360 in-lb. Use dial
indicator to check end play. Add or remove shims until
indicator reads .001” to .003”.
7. Again using the same procedure as in step 6, adjust the
input shaft bearings to an end play of .002” to .003”.
8. Total shim thickness per carrier or cover should not include
more than .009” plastic shims. All other shims should be
metal, and each plastic shim should be inserted between
two metal shims. Place a 1/8” diagonal bead of Dow
Corning RTV732 sealant on the face around the I.D. of the
last shim and install the carriers or covers in the reducer
housings. Torque carrier bolts to torque values in Table 5.