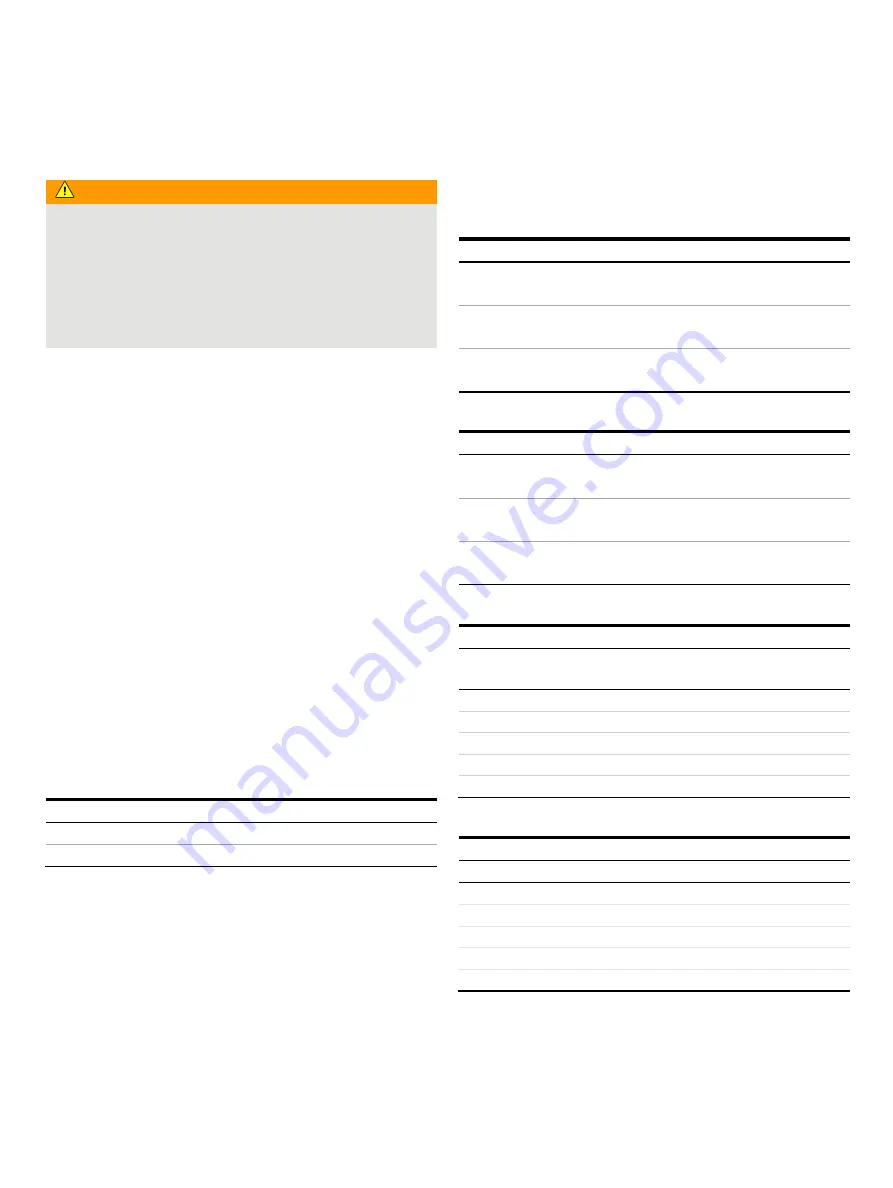
26
RHDE250 to RHDE4000 (Contrac)
ELECTRICAL ROTARY ACTUATOR | OI/RHDE250_4000-EN REV. B
Change from one to two columns
7
Electrical connections
Safety instructions
WARNING
Risk of injury due to live parts!
Risk of death or serious injuries due to electricity and
unexpected machine movements. In automatic mode the
motor is always under power, even at standstill.
• When working on the actuator or the related subassembly,
switch off the supply voltage for the electronic unit and
separate anti-condensation heater (option), and take
precautions to prevent unintentional switch-on.
The electrical connection may only be established by authorized
specialist personnel.
Notices on electrical connection in this instruction must be
observed; otherwise, electric safety and the IP-rating may be
adversely affected.
Safe isolation of electric circuits which are dangerous if touched
is only guaranteed when the connected devices fulfill the
requirements of EN 61140 (basic requirements for secure
separation).
To ensure safe isolation, install supply lines so that they are
separate from electrical circuits which are dangerous if touched,
or implement additional isolation measures for them.
Each actuator requires a suited Contrac electronic unit with
installed actuator-specific software. Observe the information in
the operating instruction. The specifications on the name plates
of the electronic unit and actuator must match to guarantee
correct hardware and software allocation.
Conductor cross-section on control
actuator
Screw terminals
Motor/brake
max. 2.5 mm
2
(14 AWG)
Signals
max. 2.5 mm
2
(14 AWG)
Conductor cross-section on electronic unit
Note
Detailed information on separate electronic units can be found
in the corresponding data sheets.
EBN853 – Screw terminals
Motor/brake
rigid: 0.2 to 6 mm
2
(24 to 10 AWG)
flexible: 0.2 to 4 mm
2
(24 to 12 AWG)
Mains
rigid: 0.5 to 6 mm
2
(20 to 10 AWG)
flexible: 0.5 to 4 mm
2
(20 to 12 AWG)
Signals
rigid: 0.5 to 4 mm
2
(20 to 12 AWG)
flexible: 0.5 to 2.5 mm
2
(20 to 14 AWG)
EBN861 – Screw terminals
Motor / brake
rigid: 0.2 to 6 mm
2
(24 to 10 AWG)
flexible: 0.2 to 4 mm
2
(24 to 12 AWG)
Mains
rigid: 0.5 to 6 mm
2
(20 to 10 AWG)
flexible: 0.5 to 4 mm
2
(20 to 12 AWG)
Signals
rigid: 0.5 to 4 mm
2
(20 to 12 AWG)
flexible: 0.5 to 2.5 mm
2
(20 to 14 AWG)
EBS852 – Clamping connection
Suited for cable Ø Terminals for conductor
cross-section
Mains cable
13 mm (0.51 in)
max. 4 mm
2
(12 AWG)
Signal cable (DCS)
8 mm (0.31 in)
max. 1.5 mm
2
(16 AWG)
Transmitter (option)
8 mm (0.31 in)
max. 1.5 mm
2
(16 AWG)
Motor cable
13 mm (0.51 in)
max. 4 mm
2
(12 AWG)
Sensor cable
8 mm (0.31 in)
max. 1.5 mm
2
(16 AWG)
EBS862 – Clamping connection
Terminals for conductor cross-section
Mains cable
max. 6 mm
2
(10 AWG)
Signal cable (DCS)
max. 4 mm
2
(12 AWG)
Transmitter (option)
max. 4 mm
2
(12 AWG)
Motor cable
max. 6 mm
2
(10 AWG)
Sensor cable
max. 4 mm
2
(12 AWG)