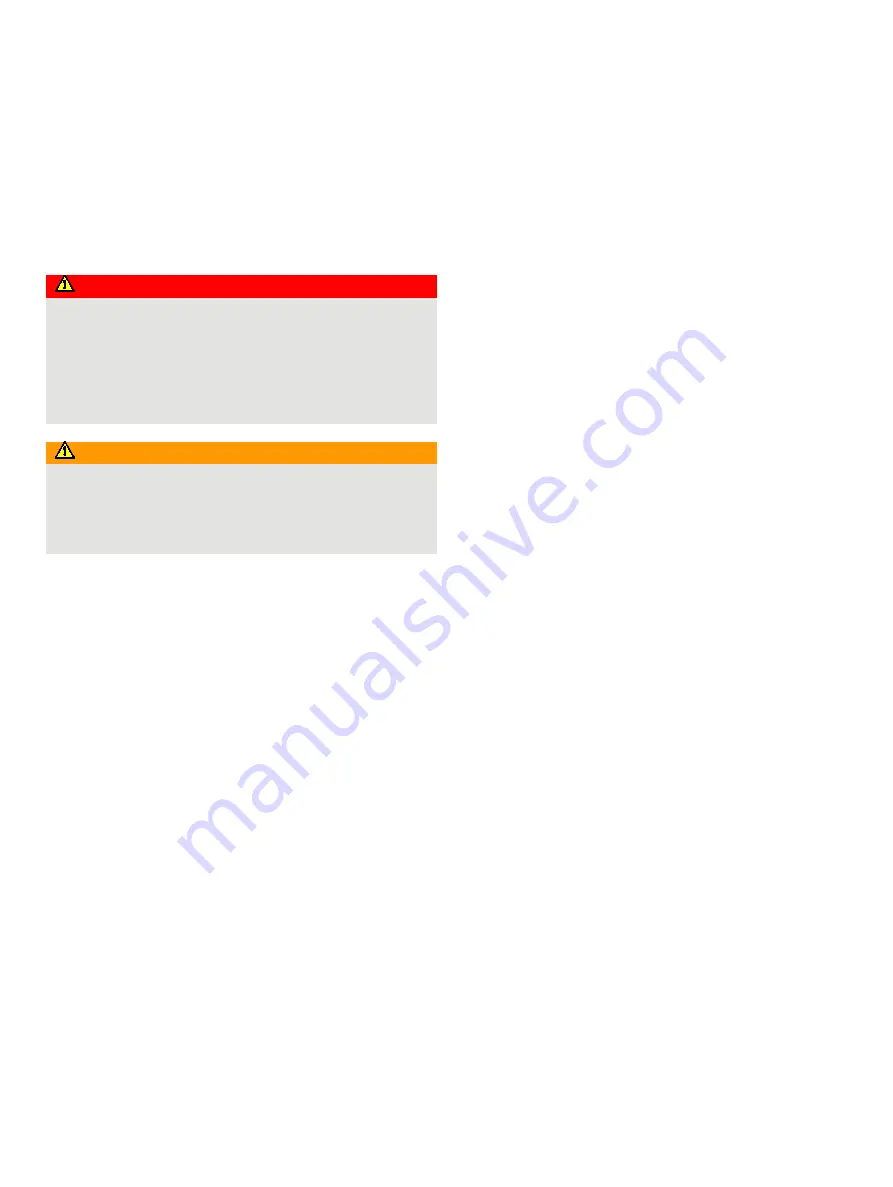
AO2000-LS25
LASER ANALYZERS | OI/AO2000-LS25-EN REV. D
13
Opening and closing the housing
This housing contains a 3 V lithium battery.
Observe the following safety instructions when opening and
closing the housing with the type of protection Ex “p” –
pressurized enclosure:
DANGER
Explosion hazard
There is a risk of explosion if the housing is opened in a
hazardous atmosphere.
Before opening the housing:
• A valid fire permit must be present.
• Make sure that there is no explosion hazard.
• Before opening the housing, switch off the power supply.
WARNING
Risk of suffocation
Risk of suffocation when using inert purging gases such as
nitrogen (N
2
).
• Before opening the housing, switch off the housing
purging.
Recommissioning after opening the housing
• Before closing the housing and recommissioning, all dust
deposits in and on the device must be removed.
• After closing the housing, the power supply must not be
restored until an initial purge duration of at least 3 minutes
at 20 l/min has elapsed.
Only original spare parts must be used to seal the housing.