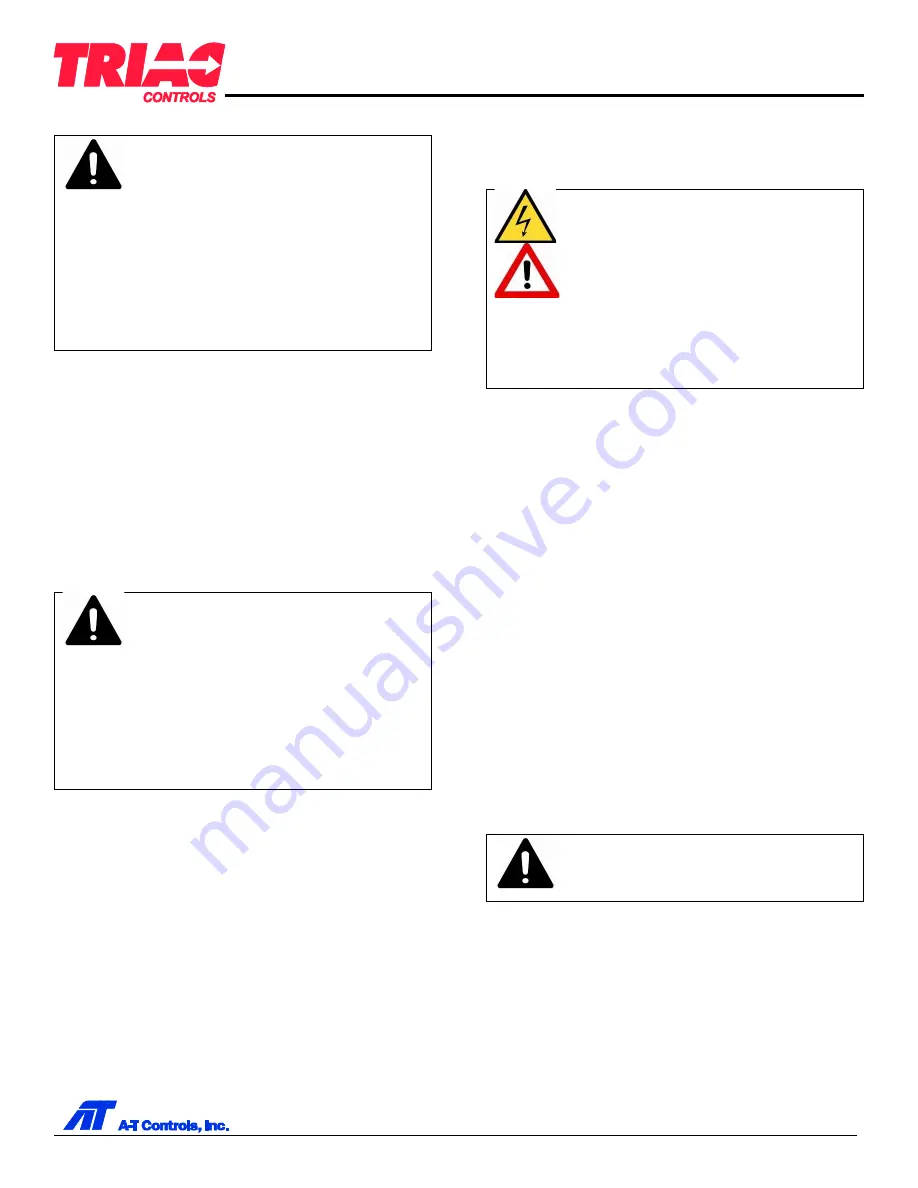
WE/XE/SE/XC Series
Quarter-Turn Electric Actuator
Installation & Maintenance Manual
12
12/17/19
www.atcontrols.com
IOM8011 REVISION 01
CAUTION:
o
Do not immediately reverse the motor
direction. A one second delay before
reversing motor direction is recommended.
o
Do not energize both actuator inputs
simultaneously.
o
If the actuator stops by the mechanical travel
stops instead of the limit switches, the motor
may overheat and go into thermal overload.
Electrical operation will not be possible until
overload resets. The motor may eventually
fail if repeatedly overheated.
6.3.2. 3 Phase and DC Voltage Actuators
A 3-phase actuator without a control module, or DC
voltage actuator without reversing control card will
require the operator to check the phase and polarity
connection prior to operation. Manually operate the
actuator to the 50% open position then apply power to
the actuator motor connections. This will rotate motor in
one direction. To reverse the direction, exchange wire 1
with wires 2 or 3 on the 3-phase voltage actuator, or
swap wires wires on DC voltage actuator.
CAUTION:
o
Energizing the motor directly risks the
actuator driving into the mechanical stops.
Verify limit switch and mechanical stop
adjustment before checking direction and
make sure to disconnect power to motor
before limit switches are activated to avoid
stalling the motor.
o
Command inputs to controller used to
reverse direction should be wired through
travel limit switches.
6.3.3. Jamming
If the actuator travels into a mechanical travel stop, the
worm gear will jam. Remove power from the command
input. Briefly apply power in the reverse direction to
release the pressure from the worm gear. The limit
switches and mechanical travel stops should be
readjusted per the instructions if jamming occurs.
7. Maintenance
WARNING:
o
Hazardous voltage. Turn off all power and
lock out service panel before performing
maintenance on the actuator.
o
Potentially high-pressure vessel. Before
removing or disassembling the actuator,
ensure that the valve or other actuator
device is isolated and not under pressure.
o
Any issue detected that may affect the safe
operation of the actuator must have
immediate action taken to repair
.
Under normal conditions, maintenance should be carried
out at six-month intervals. More frequent maintenance is
advised if operating in more severe conditions.
Ensure the actuator is properly aligned with the
valve or other actuated device.
Ensure all wiring is undamaged and insulated,
connected and terminated properly.
Ensure all screws are present and tight.
Ensure internal electrical components and devices
are clean and free from dust or debris.
Ensure cable and conduit connections are properly
installed and dry.
Check inside of housing for any signs of
condensation or moisture.
Check power to the internal heater.
Check enclosure o-rings.
Verify manual override functions properly.
Visually inspect the open/close cycle.
Inspect the identification labels for wear and replace
if necessary.
Check for damage to enclosure.
CAUTION:
Use only original factory parts for repairs and
replacement.