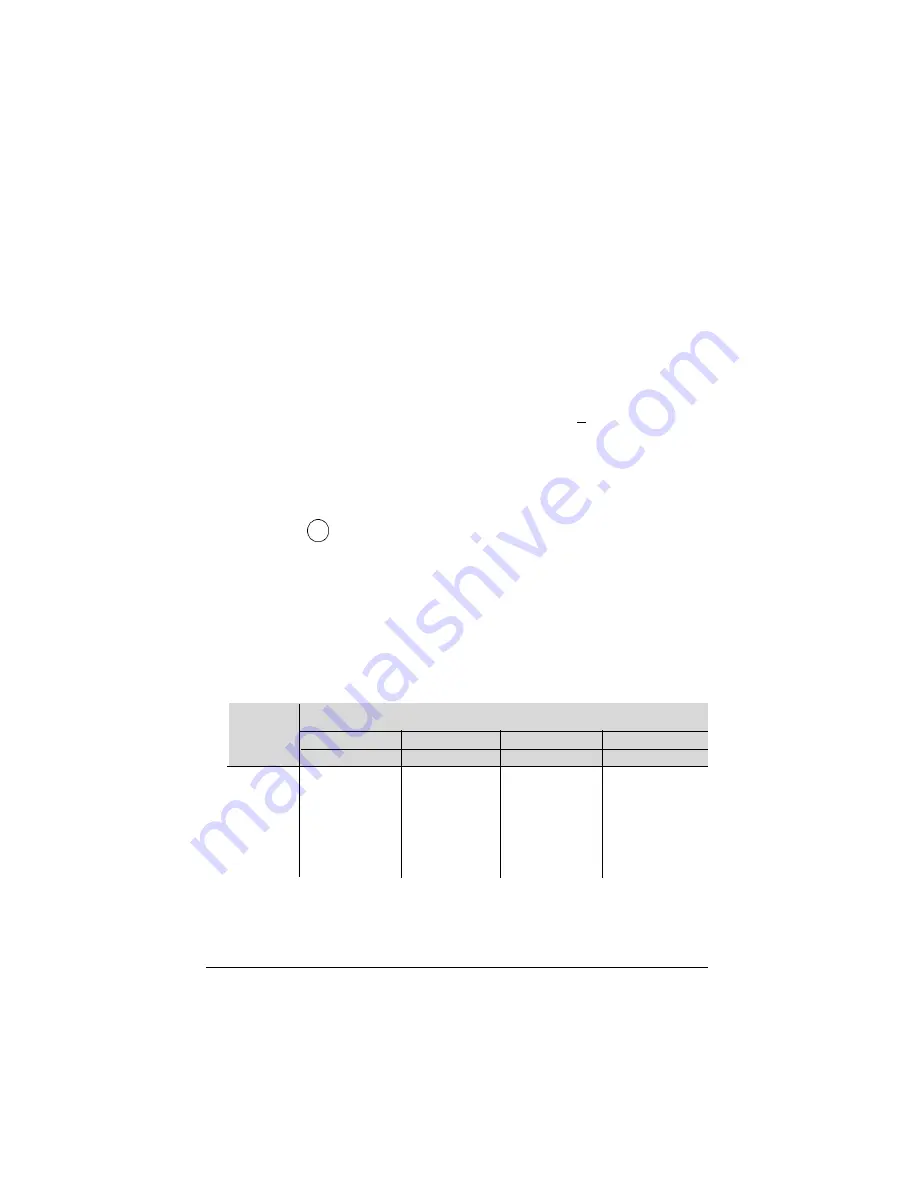
20
Pump Motors
Level 2
A.O.Smith
See that this electrical list is followed:
■
Assure proper voltage at motor terminals.
■
Follow motor connection diagram on motor nameplate.
■
Make sure motor is properly GROUNDED and complies
with local and national electrical codes.
■
See that the pump turns freely before starting motor.
FAILURE TO START
(MOTOR MAKES NO SOUND)
■
Check voltage at motor line terminals. Voltage should cor-
respond with motor nameplate rating (+10%).
■
Check all electrical connections at the motor terminal
board.
■
If no voltage is present; check fuses, timers & switches.
■
Protector tripped — wait until motor cools then restart —
check protector for continuity.
The following chart shows recommended minimum
wire sizes for pump motors. The calculations were based on
motors with the highest starting currents. Larger wire sizes
reduce the voltage drop at the motor in both the start and run
modes. A lower voltage drop means the motor will run more
efficiently (cooler) and have increased service life. In general,
and up to a certain point, the efficiency gained from one size
larger wire will have a payback of less than two years.
PUMP MOTOR RECOMMENDED MINIMUM WIRE SIZE*
*Always follow all applicable codes.
**Pump Motors with service factors greater than 1, and split phase designs.
No more than 15 volts drop at start, in worst case.
DISTANCE FROM SERVICE ENTRANCE/MAIN PANEL TO MOTOR
50 feet
100 feet
150 feet
200 feet
115V
230V
115V
230V
115V
230V
115V
230V
1/3
14
14
12
14
10
12
8
12
1/2
14
14
10
14
8
12
8
10
3/4
12
14
10
12
8
12
6
10
1
12
14
8
12
8
10
6
8
1-1/2
10
14
8
12
6
10
6
8
2
10
14
8
10
6
10
6
8
3
12
10
8
8
Motor
H.P.
**
$