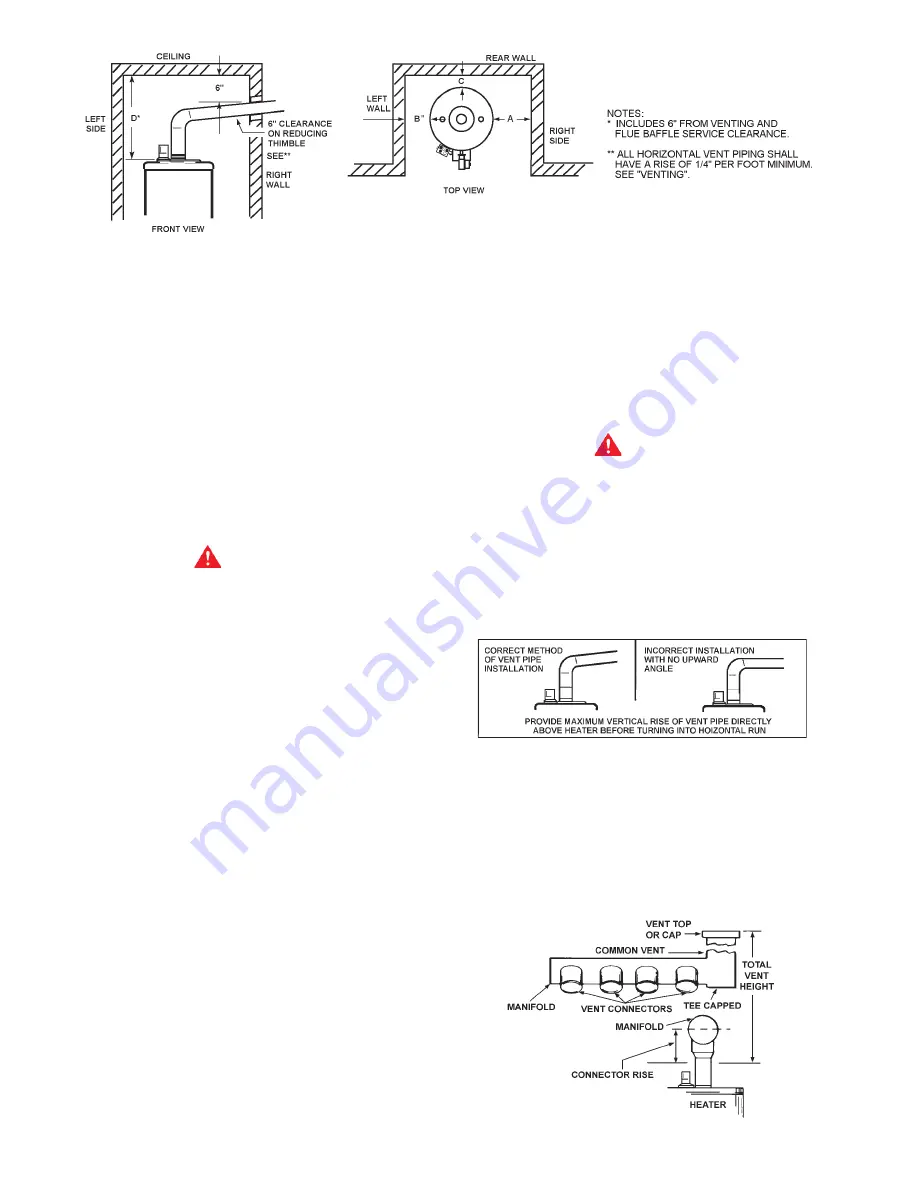
8
AND ONE IN OR WITHIN 12 INCHES (30.5cm) OF THE
ENCLOSURE BOTTOM. Each opening shall have a free area of
at least one square inch per 1000 Btuh (2,225mm
2
/kW)of the
total input of all appliances in the enclosure, but not less than
100 square inches (645 square cm).
If the confined space is within a building of tight construction, air
for combustion, ventilation, and drafthood dilution must be
obtained from outdoors. When directly communicating with the
outdoors or communicating with the outdoors through vertical
ducts, two permanent openings, located in the above manner,
shall be provided. Each opening shall have a free area of not
less than one square inch per 4000 Btuh (550mm
2
/kW) of the
total input of all appliances in the enclosure. If horizontal ducts
are used, each opening shall have a free area of not less than
one square inch per 2000 Btuh (1102mm
2
/kW) of the total input
of all appliances in the enclosure.
VENTING
WARNING
THE INSTRUCTIONS IN THIS SECTION ON VENTING MUST
BE FOLLOWED TO AVOID CHOKED COMBUSTION OR
RECIRCULATION OF FLUE GASES. SUCH CONDITIONS
CAUSE SOOTING OR RISKS OF FIRE AND ASPHYXIATION.
Heater must be protected from freezing downdrafts.
Remove all soot or other obstructions from the chimney that will
retard a free draft.
Type B venting is recommended with these heaters. For typical
venting application see TECHNICAL DATA VENTING on pages 9
and 10.
This water heater must be vented in compliance with all local
codes, the current revision of the National Fuel Gas Code
(ANSI-Z223.1) and with the Category I Venting Tables.
If any part of the vent system are exposed to ambient
temperatures below 40°F (5°C) it must be insulated to prevent
condensation.
The following steps shall be followed with each appliance
connected to the venting system placed in operation, while any
other appliances connected to the venting system are not in
operation.
1. Seal any unused openings in the venting system.
2. Inspect the venting system for proper size and horizontal pitch,
as required in the National Fuel Gas Code, ANSI Z223.1.
Determine that there is no blockage or restriction, leakage,
corrosion and other deficiencies which could cause an unsafe
condition.
3. So far as is practical, close all building doors and windows
and all doors between the space in which the water heater(s)
connected to the venting system are located and other spaces
of the building. Turn on all appliances not connected to the
venting system. Turn on all exhaust fans, such as range
hoods and bathroom exhausts, so they shall operate at
maximum speed. Close fireplace dampers.
4. Follow the lighting instruction. Place the water heater being
inspected in operation. Adjust thermostat so appliance shall
operate continuously.
5. After it has been determined that each appliance connected
to the venting system properly vents when tested as outlined
above, return doors, windows, exhaust fans, fireplace
dampers and any other gas burning appliance to their
previous conditions of use.
6. If improper venting is observed during any of the above tests,
the venting system must be corrected.
WARNING
FAILURE TO CORRECT BACK DRAFTS MAY CAUSE AIR
CONTAMINATION AND UNSAFE CONDITIONS.
• If the back draft cannot be corrected by the normal method or
if a suitable draft cannot be obtained, a blower type flue gas
exhauster must be employed to assure proper venting and
correct combustion.
• Do not connect the heater to a common vent or chimney with
solid fuel burning equipment. This practice is prohibited by
many local building codes as is the practice of venting gas
fired equipment to the duct work of ventilation systems.
FIGURE 7
• Where a separate vent connection is not available and the
vent pipe from the heater must be connected to a common
vent with an oil burning furnace, the vent pipe should enter
the smaller common vent or chimney at a point above the
large vent pipe.
MULTIPLE HEATER MANIFOLD
Figure 8 and tables on pages 9 and 10 should be used for
horizontally manifolding two or more heaters.
FIGURE 8
ILLUSTRATION OF MINIMUM COMBUSTIBLE CLEARANCES IN AN ALCOVE - FIGURE 6