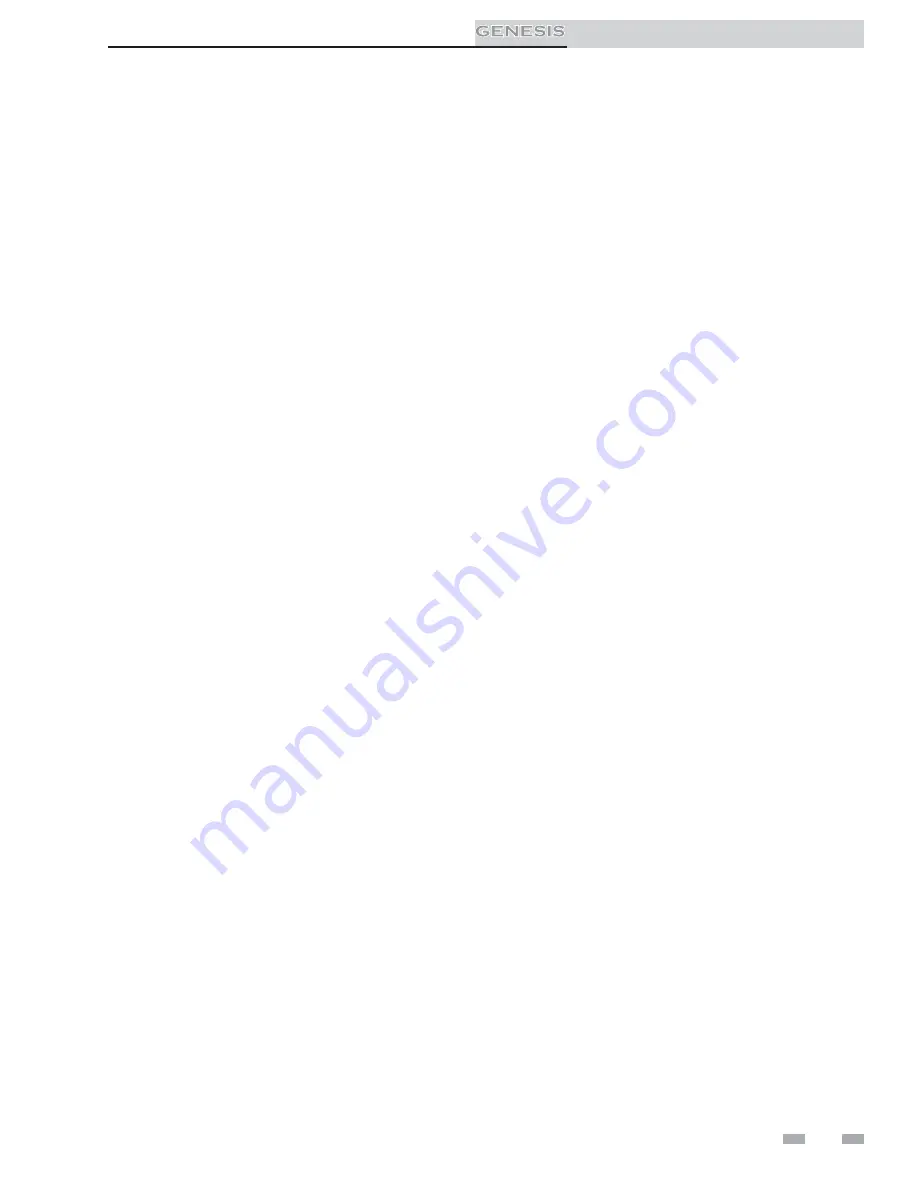
Installation & Operation Manual
5
The Genesis - How it works...
1. Heat
exchanger
The heat exchanger allows system water to flow through
specially designed tubes for maximum heat transfer. The
glass lined headers and copper fined tubing are encased in a
jacket that contains the combustion process.
2. Heat exchanger access cover
The heat exchanger access cover is a galvanized steel door which
allows access for service, maintenance, and removal of the
heat exchanger from inside the combustion chamber.
3. Blower
The blower pulls in and injects air into the individual burners
along with gas from the gas manifold where the mix is burned
inside the combustion chamber.
4. Gas
valve
The gas valves (reference) have a dual purpose; changing the
gas supply pressure to manifold pressure, and the reference
side of the gas valve is designed to allow chamber pressure
to change the volume of gas through the valve and measured
as net manifold pressure. This is not a design to compensate
for gas supply pressure issues.
5. Tank temperature sensor (not shown)
When connected, this sensor monitors tank temperature.
6. Outlet
sensor
This sensor monitors the outlet water temperature.
7. Inlet
temperature
sensor
This sensor monitors inlet water temperature. If selected as
the controlling sensor and a tank sensor is not connected, the
appliance will maintain setpoint by adjusting the firing rate
of the unit according to this sensor.
8. 2-Stage
electronic
temperature
control
The 2-stage electronic temperature control consists of a Liquid
Crystal Display (LCD) for interactive prompting during
programming and display of both sensed and assigned values.
Programming is accomplished through the use of the three (3)
programming buttons -- select, (+), and (-). This 2-stage
electronic temperature control also controls the pump.
9. LED
display
board
The LED display board displays the status of the unit. LED’s
are provided for prepurge, trial for ignition, Stage 1, Stage 2,
ignition module status and alarm along with a RESET button
for resetting the ignition module.
10. Burner
The burner is a ported stainless steel construction which uses a gas
air mix to operate at a fixed input. Banks of burners turn on
or off to vary the firing rate.
11. Water outlet (system supply)
The water outlet is a 2 or 2 1/2" (depending on model) pipe
connection that supplies water to the tank with connections
for a flow switch (see #25), a relief valve (see #22).
12. Water inlet (system return)
The water inlet is a 2 or 2 1/2" (depending on model) pipe
connection that receives water from the tank and delivers it to
the heat exchanger.
13. Gas supply pipe
The gas supply pipe on this appliance is 1 1/4 or 2" (depending
on model) diameter NPT. Please reference the National Fuel
Gas Code charts for connection details.
14. Hot surface ignition module
The hot surface ignition module controls the blower(s), hot
surface igniter and gas valves. A status LED is also provided for
flash codes used for the purpose of troubleshooting the unit.
15. Air intake
Fresh air for combustion is drawn through a filter provided at the
air intake, located at either the rear or right side of the appliance.
16. Line voltage terminal strip
The line voltage terminal strip provides a location to connect
all of the line voltage (120 VAC) contact points to the unit.
17. Low voltage connection board(s)
The low voltage connection board provides a location to connect
all of the low voltage devices to the appliance. This is where most
of the external safety controls are connected.
18. Front doors - upper and lower
The front doors provide access to the gas train as well as the
blower, burners and other key components for service and
maintenance.
19. Hot surface igniter (HSI)
The hot surface igniter is a device that is used to ignite the
air/gas mixture as well as monitor the performance of the flame
during operation. This device acts as a flame sense electrode.
20. Flame inspection window (sight glass)
The flame inspection windows, located on either side of the
appliance, allow for visual inspection of the burners and flame
during operation.
21. Manual reset high limit sensor
This device monitors the outlet water temperature to ensure
safe operation. If the temperature exceeds its setting (field
adjustable), it will break the control circuit, shutting the
appliance
down.
22. Relief valve
The relief valve is a safety device that ensures the maximum
pressure of the appliance is not exceeded. Water heaters operate
on temperature and pressure and are shipped standard as 125 PSI
and 210°F (98.9°C).
23. Power switch
The power switch is used to engage and disengage power to the
appliance on the 120 VAC circuit.
24. Air pressure switch
The air pressure switch is a safety device which ensures proper
blower operation. The air pressure switch is wired in series with
the low voltage control circuit in such a way that if the fan does not
engage or shuts down prematurely the device will break the
control circuit and the unit will shut down.
25. Flow switch
The flow switch is a safety device that ensures flow through the
heat exchanger during operation. This appliance is low mass and
should never be operated without flow. The flow switch makes
contact when flow is detected and allows the unit to operate. If
flow is discontinued during operation for any reason the flow
switch will break the control circuit and the unit will shut down.
26. Drain port(s)
The drain port(s) are located underneath the front header.
27. Manual shutoff valve (not shown)
Manual valve used to isolate the unit from the gas supply.