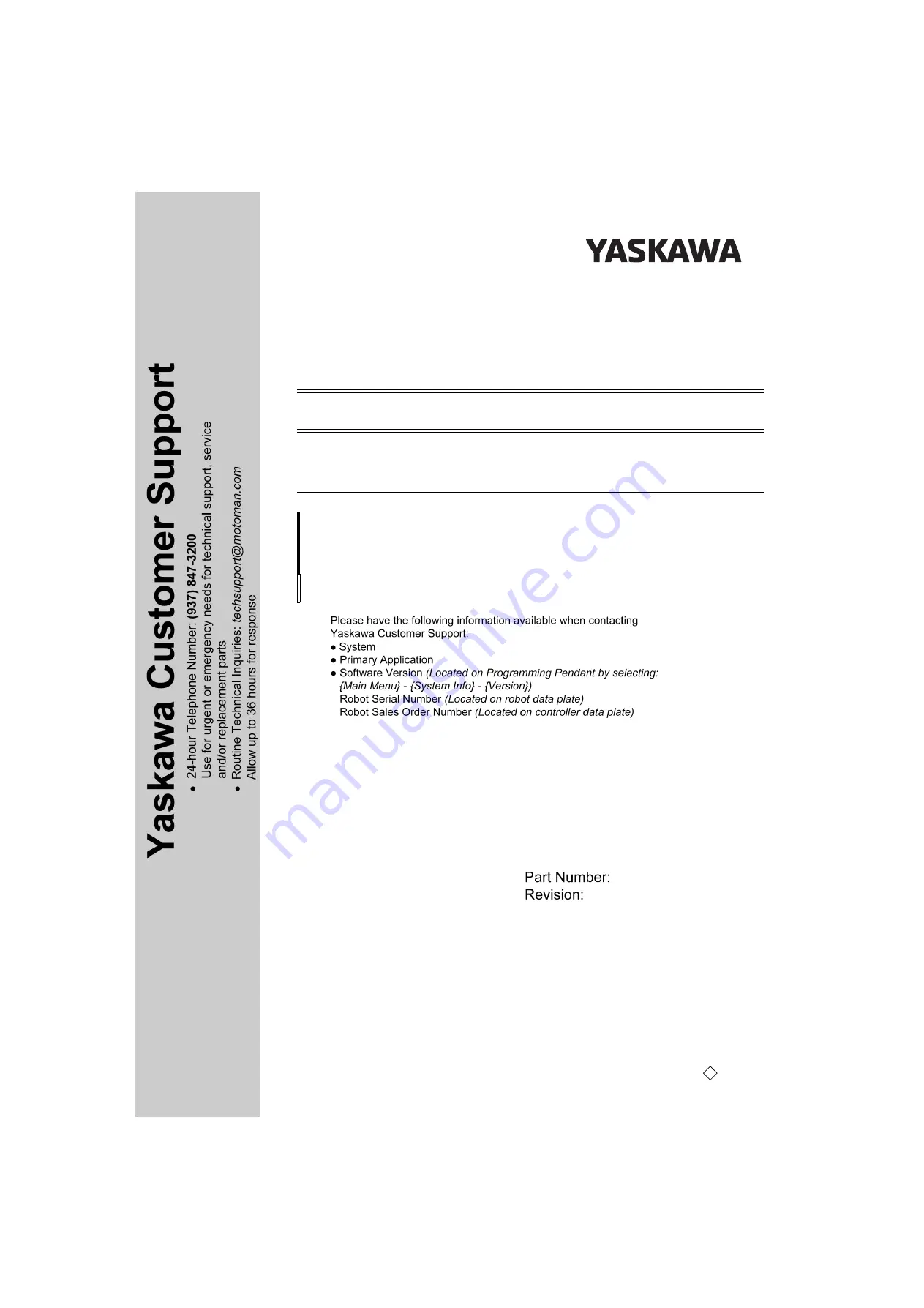
MANUAL NO.
HW1483028
2
MOTOMAN-MC2000
II
INSTRUCTIONS
TYPE
YR-MC02000-J00 (DX200 STANDARD SPECIFICATION)
Upon receipt of the product and prior to initial operation, read these instructions thoroughly, and
retain for future reference.
MOTOMAN INSTRUCTIONS
MOTOMAN-MC2000
II
INSTRUCTIONS
DX200 INSTRUCTIONS
DX200 OPERATOR’S MANUAL (for each purpose)
DX200 MAINTENANCE MANUAL
The DX200 operator’s manual above corresponds to specific usage. Be sure to use the appropriate manual.
1/69
173704-1CD
1