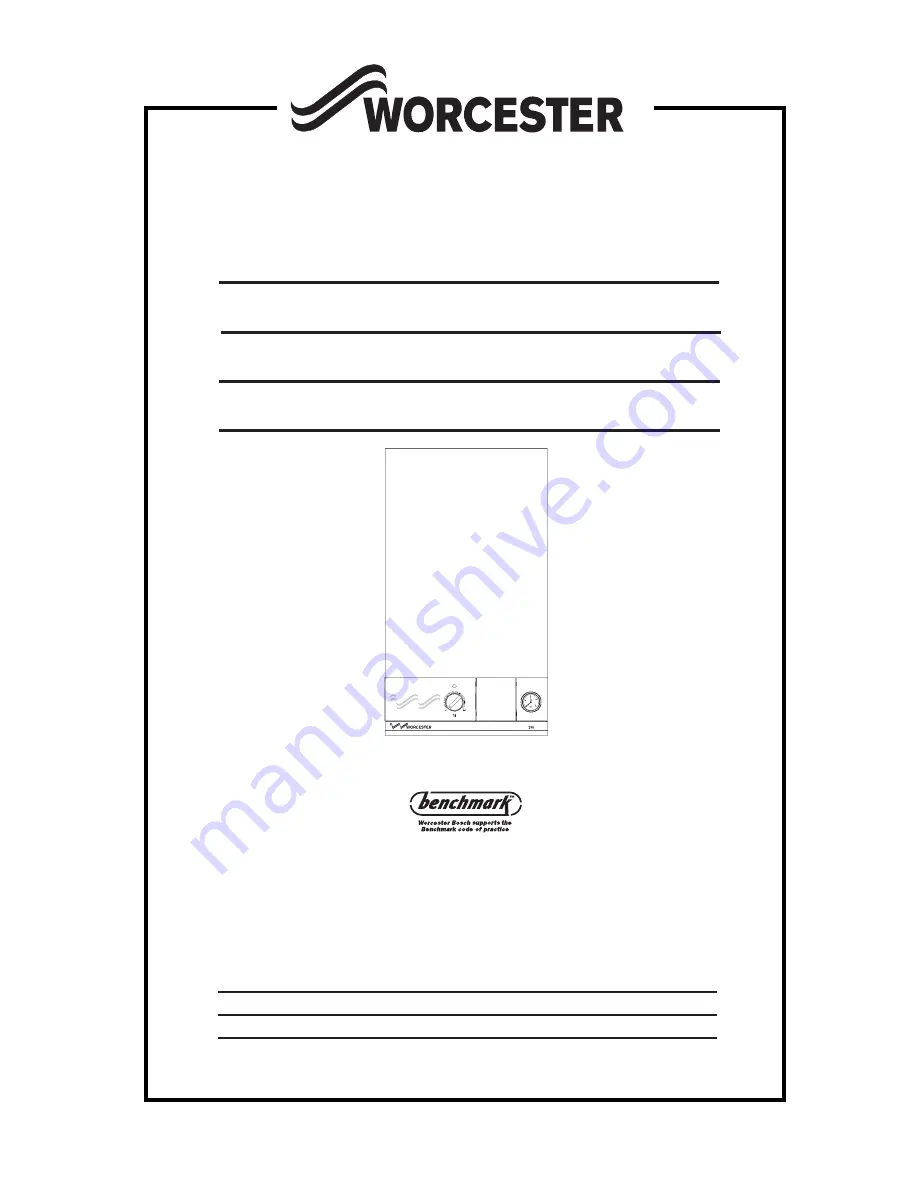
Bosch Group
24i RSF
WALL MOUNTED COMBINATION BOILER FOR CENTRAL HEATING
AND MAINS FED DOMESTIC HOT WATER
INSTALLATION AND
SERVICING INSTRUCTIONS
GC NUMBERS
N.G. 47 311 37
L.P.G. 47 311 38
BOILER OUTPUT
To Domestic Hot Water – Modulated Control
Minimum 7.5 kW (25,600 Btu/h)
Maximum 23.4 kW (80,000 Btu/h)
To Central Heating – Modulated Control\
Auto Range Rated
Minimum 7.5 kW (25,600 Btu/h)
Maximum 23.4 kW (80,000 Btu/h)
THESE INSTRUCTIONS APPLY IN THE UK ONLY
THESE INSTRUCTIONS ARE TO BE LEFT WITH THE USER OR AT THE GAS METER
This appliance must be installed by a competent person in accordance
with the Gas Safety (Installation and Use) Regulations 1994