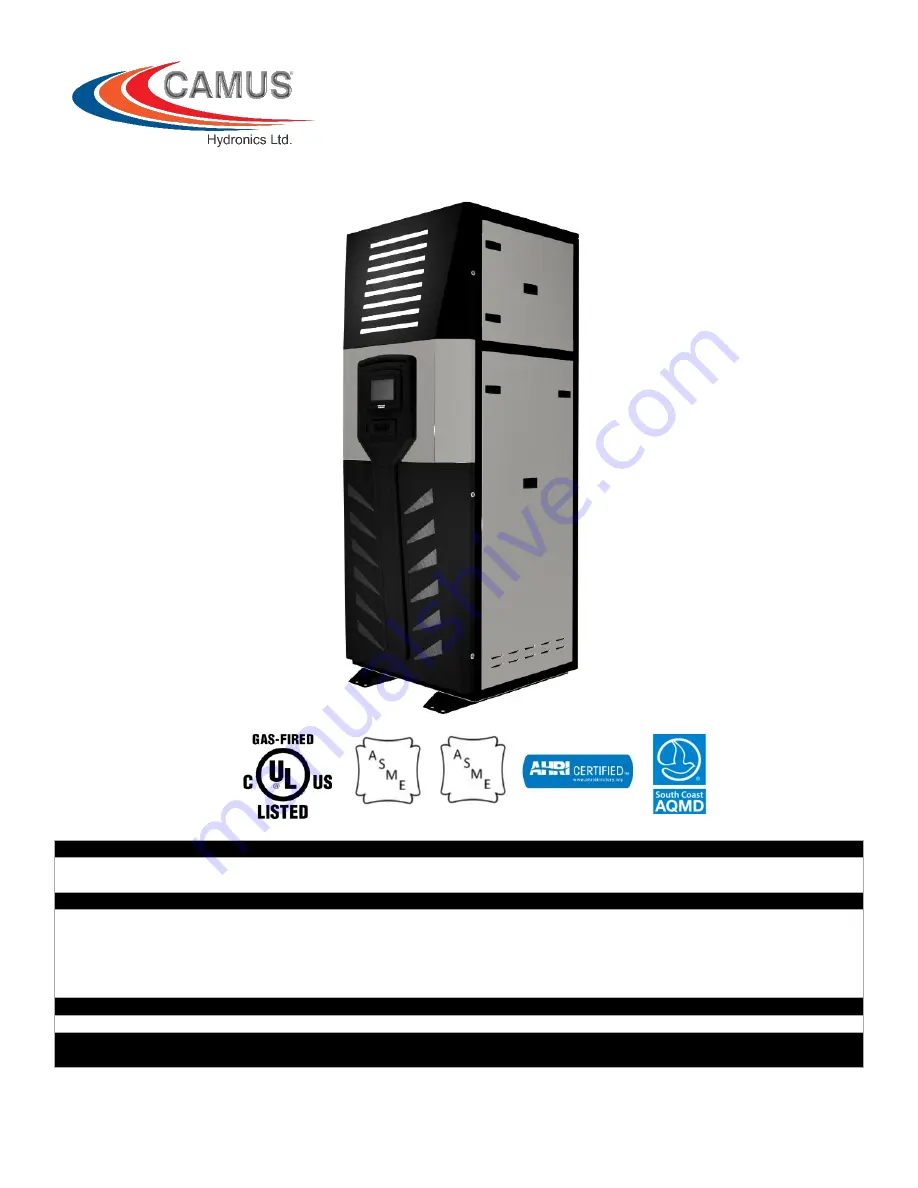
99-0600 Rev.03
Avenger® Series
Installation, Operation and Service Manual
Gas Fired Commercial Condensing Stainless Steel Boilers
Hydronic Heating Models ARH1000 thru ARH4000
Hot Water Heater Models ARW1000 thru ARW4000
WARNING
If the information in these instructions is not followed exactly, a fire or explosion may result causing property damage, personal injury
or death.
WHAT TO DO IF YOU SMELL GAS
•
Do not try to light any appliance,
•
Do not touch any electrical switch; do not use any phone in your building,
•
Immediately call your gas supplier from a neighbour’s phone. Follow the gas supplier’s instructions,
•
If you cannot reach your gas supplier, call the fire department.
A Qualified installer, service agency or the gas supplier must perform installation and service.
WARNING
Do not store or use gasoline or other flammable vapours and liquids in the vicinity of this or any other appliance.
TO THE INSTALLER:
After installation, these instructions must be given to the end user or left on or near the appliance.
TO THE END USER:
This booklet contains important information about this appliance. Retain for future reference.
H
HLW
Summary of Contents for Avenger Series
Page 2: ......
Page 35: ...30 Figure 21 Recommended Piping with Reverse Return and Variable Primary Flow...
Page 84: ...79 Figure B BLOWER BURNER ASSEMBLY...
Page 87: ...82 Figure C TYPICAL GAS TRAIN AR1000 AR3000 Figure D TYPICAL GAS TRAIN AR3500 AR4000...
Page 89: ...84 Figure E CONTROL BOARD ASSEMBLY...
Page 92: ...87 PART 13 ELECTRICAL DIAGRAMS...
Page 93: ...88...
Page 94: ...89...
Page 95: ...90...
Page 96: ...91...
Page 97: ...92...
Page 98: ...93...
Page 99: ...94...
Page 100: ...95...
Page 101: ...96...
Page 102: ...97...
Page 103: ...98...
Page 104: ...99...
Page 105: ...100...
Page 106: ...101...