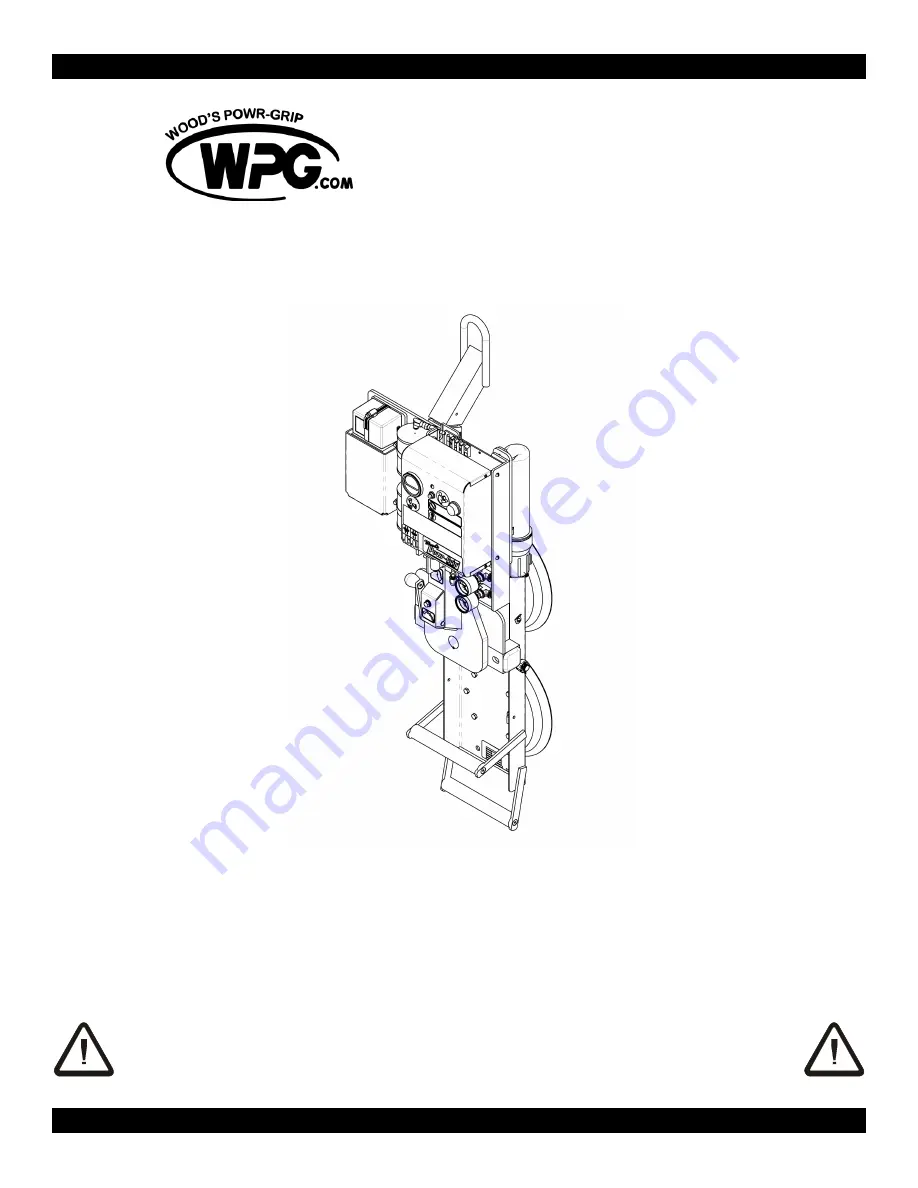
KEEP FOR FUTURE REFERENCE
INSTRUCTIONS
International Version
MODEL NUMBERS: P11002DC,
P1HV1102DC, P11102DC
SERIAL NUMBER: ____________
(please see serial label and record number here)
2-PAD CHANNEL LIFTER
DC-VOLTAGE
WITH DUAL VACUUM SYSTEM
READ ALL INSTRUCTIONS AND WARNINGS
BEFORE OPERATING THIS LIFTER
DESIGNED FOR THE MATERIALS HANDLING PROFESSIONAL
P.O. Box 368 – 908 West Main
Laurel, MT USA 59044
phone 800-548-7341
phone 406-628-8231
fax 406-628-8354
Summary of Contents for P1 COMPACT Series
Page 2: ......
Page 32: ...Rev 4 7 4 18 30 P1 02DC 35108 ...
Page 33: ...Rev 4 7 4 18 31 P1 02DC 35108 ...
Page 34: ...Rev 4 7 4 18 32 P1 02DC 35108 ...