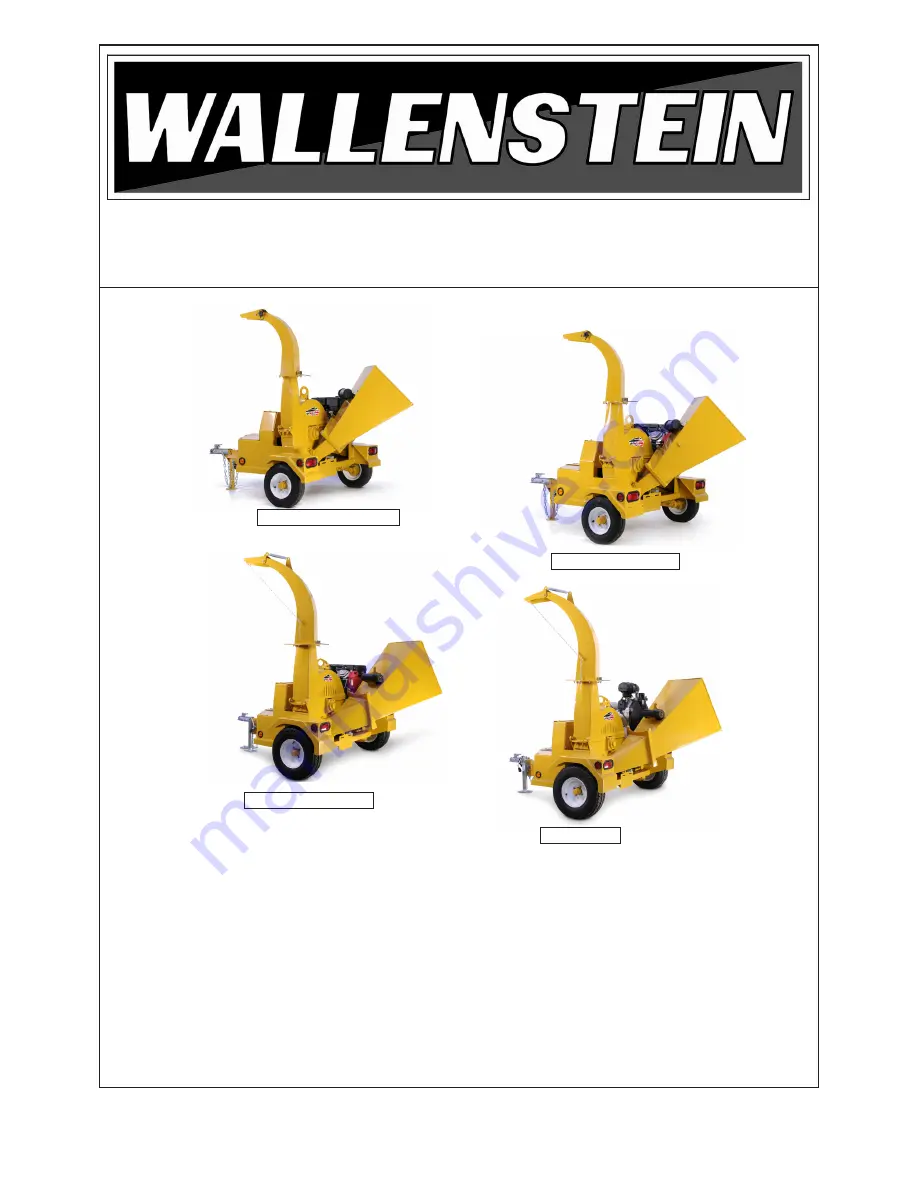
TRAILER WOOD CHIPPER
MODEL
BXT4213, BXT4214su, BXT4224,
BXT4228su, BXT6224, BXT6228su &
BXT6238
OPERATOR'S MANUAL
BY
EMB MFG INC.
PRINTED IN CANADA
Rev: 290512 PART NUMBER: Z97033
EMB Manufacturing Inc.
4144 Boomer Line · St. Clements, On · N0B 2M0 · Canada
Ph: (519) 699-9283 · Fax: (519) 699-4146
www.embmfg.com
BXT4213 / BXT4214su
BXT4224 / BXT4228su
BXT6224 / BXT6228su
BXT6238