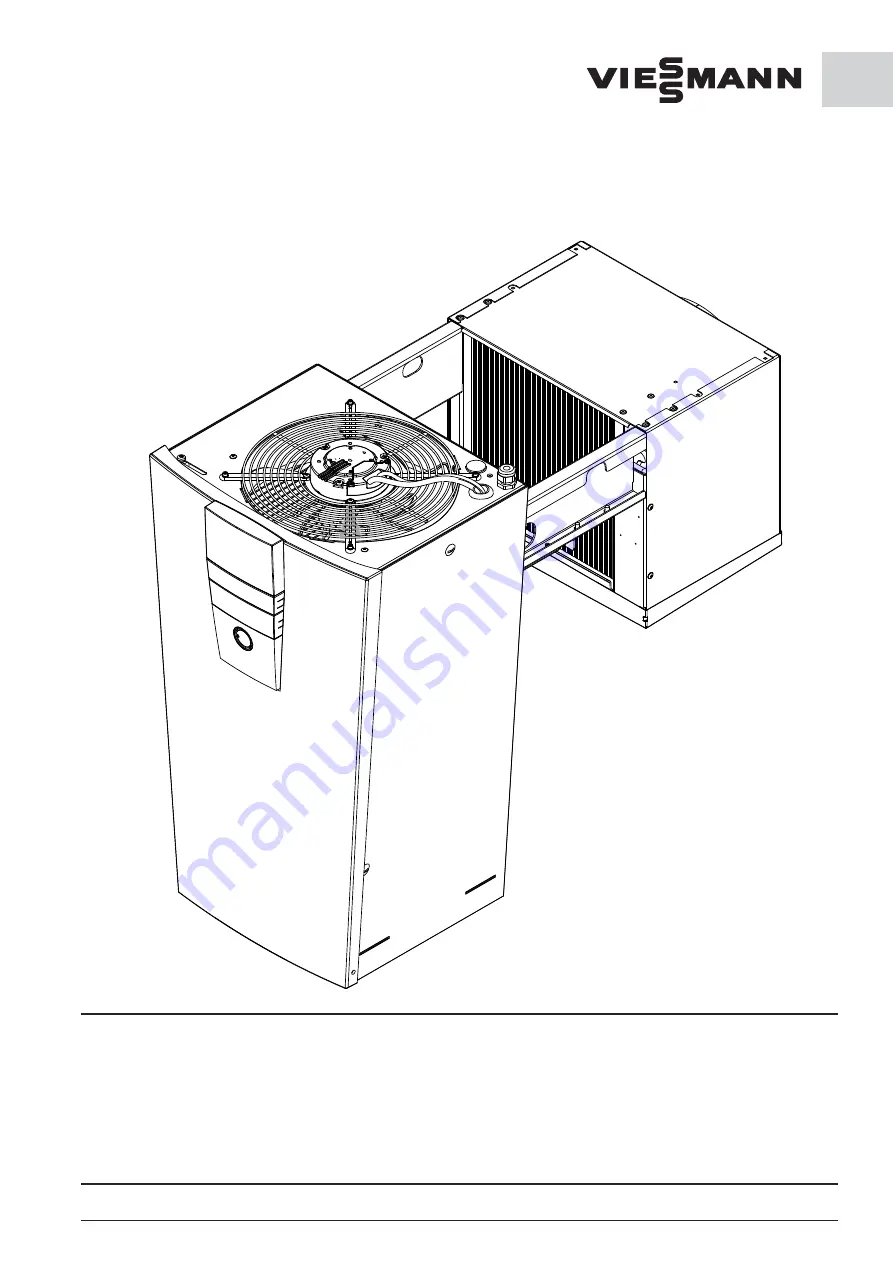
Ensure compliance with the following instructions prior to beginning work on the Refrigeration unit:
Refrigeration units EVO
-COOL®
Installation and
operating Instructions
6008309-01 GB
General notice (liability): the details of this technical documents serve for description. Consents regarding the availability of certain features or
regarding a certain purpose always require a special written agreement.
GB
We reserve the right to make technical changes! Status as of 02.15
Page 1
Installation, cleaning maintenance and repair work must be
performed only by a refrigeration specialist company.
Technical modifi cations and manipulation are prohibited.
Non-compliance will result in forfeiture of all warranty claims.
Work on the Refrigeration unit is authorised only when the mains
plug has been removed. The Refrigeration unit must be protec-
ted against unauthorized activation by appropriate means
(e.s. warning sign). The directives, VDE 0105 Part 1, for working
on electrical equipment must be complied with.