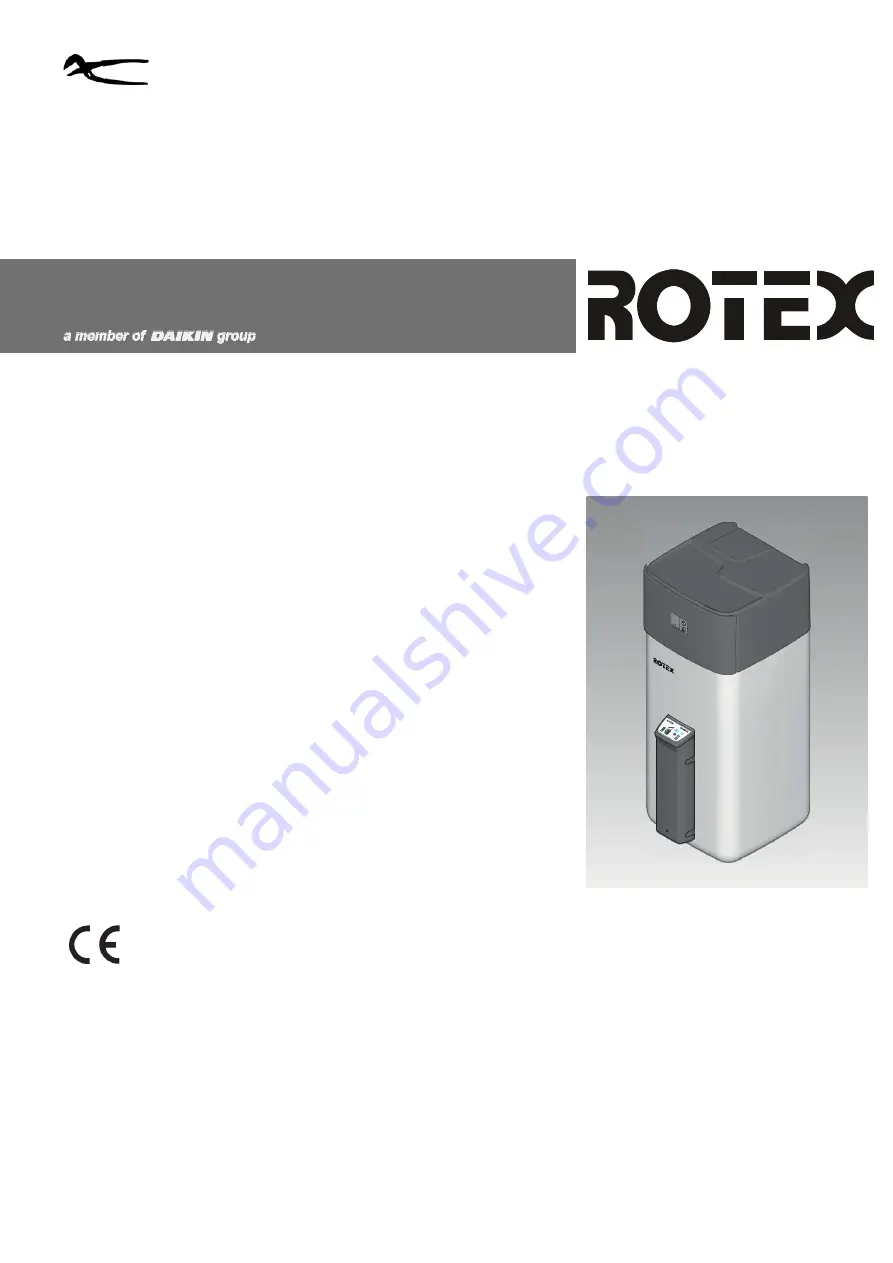
For certified companies
ROTEX
GCU compact
Installation and maintenance
instructions
Floor-standing gas condensing boiler with integrated
heat storage
Types
GCU compact 315
GCU compact 320
GCU compact 515
GCU compact 520
GCU compact 524
GCU compact 528
GCU compact 315 Biv
GCU compact 320 Biv
GCU compact 515 Biv
GCU compact 520 Biv
GCU compact 524 Biv
GCU compact 528 Biv
GB
Edition 06/2017
0063 CR 3574
Summary of Contents for GCU compact 315
Page 81: ...13 x Notes 13 Notes...
Page 82: ...13 x Notes...