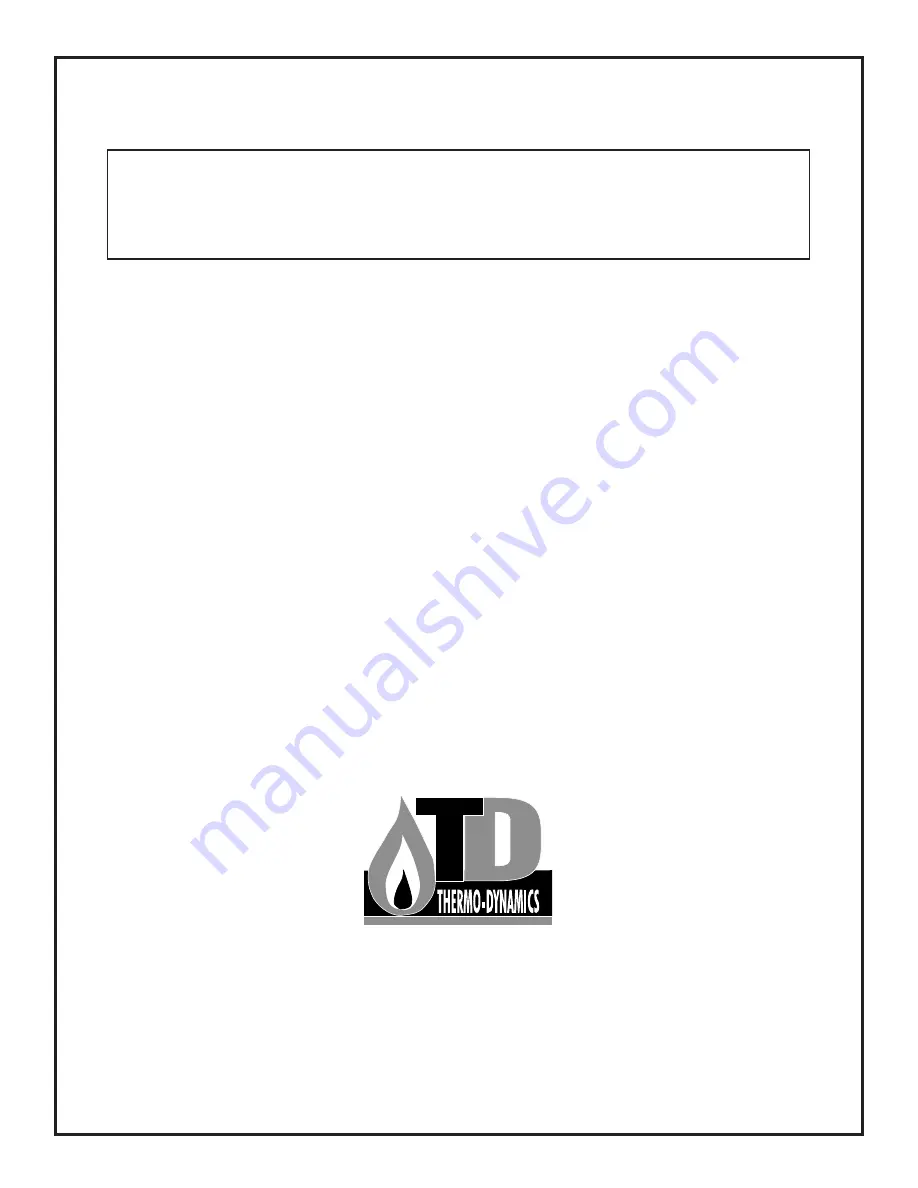
www.thermodynamicsboiler.com
Installation
Operation
Maintenance
Manual
Thermo-Dynamics Boiler Company
ROUTE 61 • P.O. BOX 325 • SCHUYLKILL HAVEN, PA 17972
TEL (570) 385-0731 • FAX (570) 385-5304
WEB www.thermodynamicsboiler.com • EMAIL [email protected]
CWL-GS Series
Models CWL GS, CWL GS DV, NCWL GS, NCWL GS DV
Gas Fired Packaged Boiler