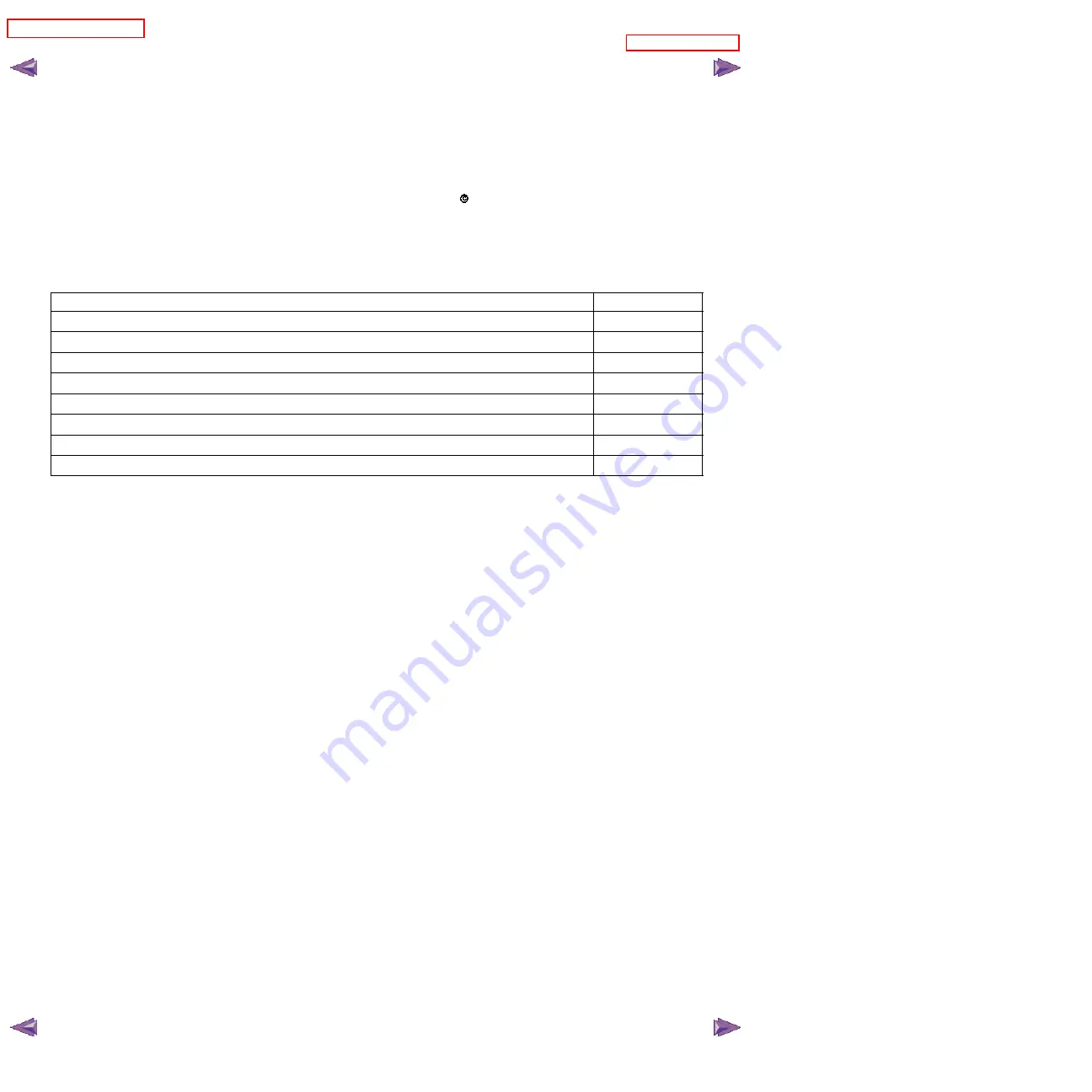
2004
TOYOTA MOTOR CORPORATION
All rights reserved. This book may not be repro-
duced or copied, in whole or in part, without the
written permission of Toyota Motor Corporation.
First Printing: Aug. 2, 2004 01--040802--00
FOREWORD
This supplement has been prepared to provide information covering general service repairs for COROLLA
which underwent changes in August, 2004.
Applicable models: NDE 120 series
For the service specifications and repair procedures of the above model other than those listed in the supple-
ment, refer to the following manuals.
Manual Name
Pub. No.
S
COROLLA Repair Manual Supplement (Jan., 2002)
RM939E
COROLLA Repair Manual Supplement (Jan., 2003)
COROLLA Repair Manual Supplement (May, 2004)
S
1ND--TV Engine Repair Manual
RM1118E
S
C53, C53A Manual Transaxle Repair Manual
RM1117E
S
COROLLA Electrical Wiring Diagram Supplement (Aug., 2004)
EWD626E
S
COROLLA New Car Featurer Supplement (May, 2004)
NCF266E
All information in this manual is based on the latest product information at the time of publication. However,
specifications and procedures are subject to change without notice.
TOYOTA MOTOR CORPORATION
CAUTION
This manual does not include all the necessary items about repair and service. This manual is made
for the purpose of the use for the persons who have special techniques and certifications. In the
cases that non--specialized or uncertified technicians perform repair or service only using this manu-
al or without proper equipment or tool, that may cause severe injury to you or other people around
and also cause damage to your customer’s vehicle.
In order to prevent dangerous operation and damages to your customer’s vehicle, be sure to follow
the instruction shown below.
S
Must read this manual thoroughly. It is especially important to have a good understanding of
all the contents written in the PRECAUTION of ”INTRODUCTION” section.
S
The service method written in this manual is very effective to perform repair and service. When
performing the operations following the procedures using this manual, be sure to use tools spe-
cified and recommended. If using non--specified or recommended tools and service method,
be sure to confirm safety of the technicians and any possibility of causing personal injury or
damage to the customer’s vehicle before starting the operation.
S
If part replacement is necessary, must replace the part with the same part number or equivalent
part. Do not replace it with inferior quality.
S
It is important to note that this manual contains various ”Cautions” and ”Notices” that must be
carefully observed in order to reduce the risk of personal injury during service or repair, or the
possibility that improper service or repair may damage the vehicle or render it unsafe. It is also
important to understand that these ”Cautions” and ”Notices” are not exhaustive, because it is
important to warn of all the possible hazardous consequences that might result from failure to
follow these instructions.
TOYOTA COROLLA REPAIR MANUAL SUPP 1129E