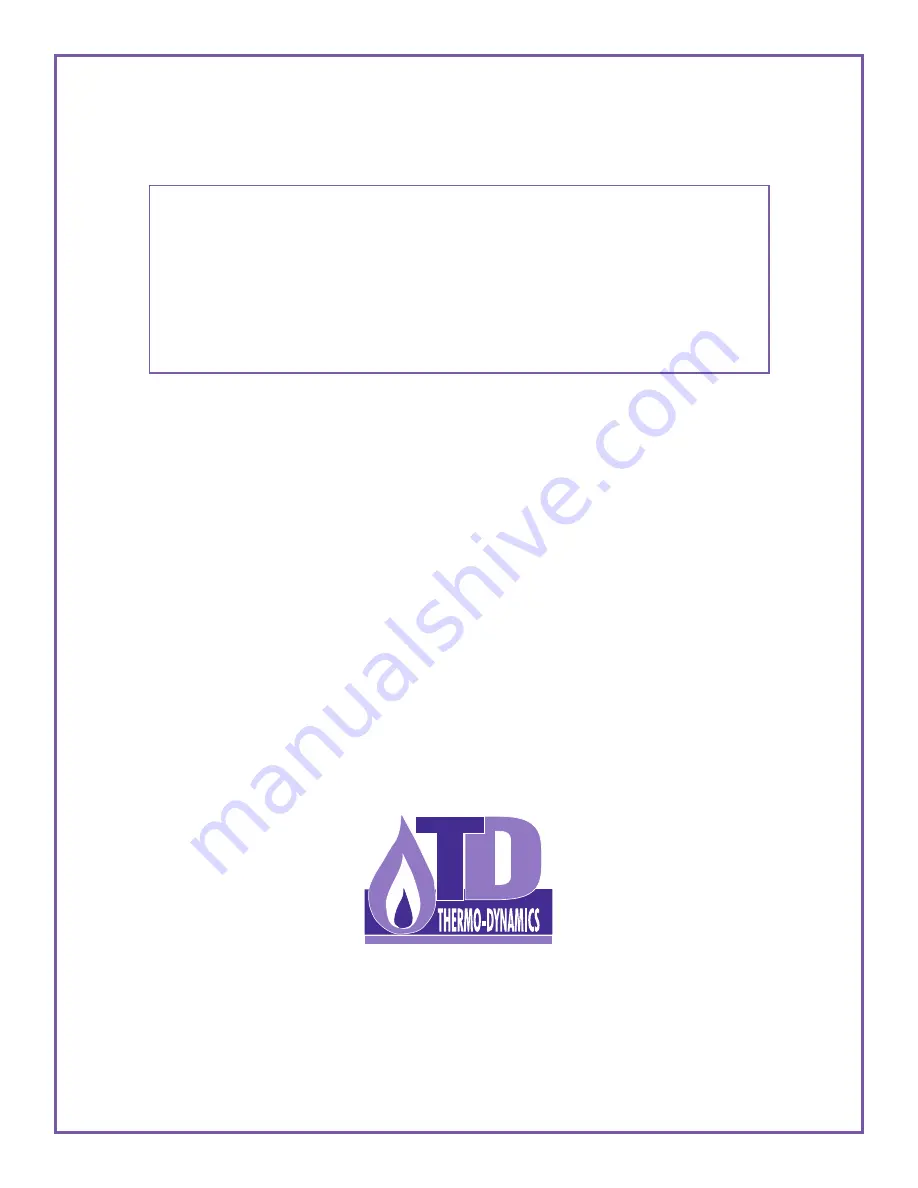
Models HT 90/100/110, HT DV 90/100/110, HT 125/135/150
HT DV 125, HT 165/175/200 and HT 225/250/275
Installation
Operation
Maintenance
Manual
Thermo-Dynamics Boiler Company
ROUTE 61 • P.O. BOX 325 • SCHUYLKILL HAVEN, PA 17972
TEL (570) 385-0731 • FAX (570) 385-5304
WEB www.thermodynamicsboiler.com • EMAIL [email protected]
HT Series