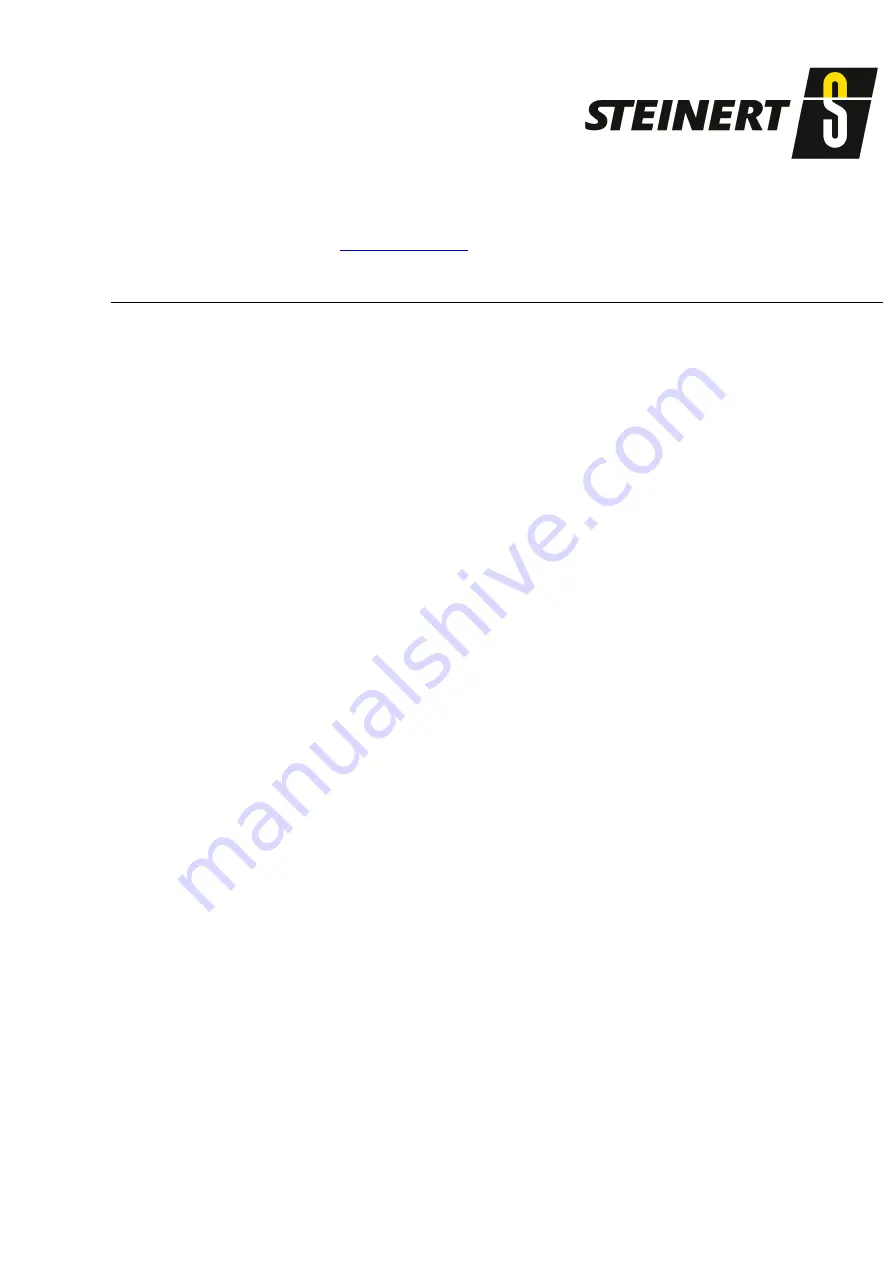
Steinert GmbH
Widdersdorfer Straße 329-331
•
D-50933 Köln
Postfach 45 11 60
•
D-50886 Köln
Phone:
Switchboard
+49-(0)221 / 49 84 - 0
Spare parts
+49-(0)221 / 49 84 - 177
Service / Repairs
+49-(0)221 / 49 84 - 132
Fax
+49-(0)221 / 49 84 - 102
www.steinert.de
INSTRUCTIONS OF INCORPORATION (EN)
Machine
Type
Serial no.
Job no.
Customer
Over-belt magnetic separator
UME 115 150 C
18 0077 0
6
0 01 + 18 0077 0
9
0 01 +
18 0077
10
0 01
A1180077
WTT B.V.
Münsterstraat 14
NL - 7575
ED Oldenzaal
KKS
no
.
1020AT203
Order no.
WTT 20180031
Order date
2018-01-24
Project name
14246 Jieyang Project
Final customer
Year of manufacture
2018
TRANSLATION OF THE ORIGINAL
Summary of Contents for UME 115 130 C
Page 2: ......
Page 8: ...Over belt magnetic separator UME C Overview 8 GB_UME 75 135 C 03 US ...
Page 60: ...Over belt magnetic separator UME C Appendix 60 GB_UME 75 135 C 03 US ...
Page 61: ......
Page 62: ......
Page 64: ...2 GB_Aufhängung AHG 02 ...
Page 66: ...Over belt magnetic separator UME C Appendix 62 GB_UME 75 135 C 03 US ...
Page 67: ...Ù Ù Ù Ù ...
Page 68: ......
Page 69: ...Over belt magnetic separator UME C Appendix 63 GB_UME 75 135 C 03 US 12 3 3 phase motor ...
Page 70: ...Over belt magnetic separator UME C Appendix 64 GB_UME 75 135 C 03 US ...
Page 71: ...Over belt magnetic separator UME C Appendix 65 GB_UME 75 135 C 03 US 12 4 Gearbox ...
Page 72: ...Over belt magnetic separator UME C Appendix 66 GB_UME 75 135 C 03 US ...
Page 74: ...Over belt magnetic separator UME C Appendix 68 GB_UME 75 135 C 03 US ...
Page 75: ...Over belt magnetic separator UME C Appendix 69 GB_UME 75 135 C 03 US 12 6 Wiring diagram ...
Page 76: ...Over belt magnetic separator UME C Appendix 70 GB_UME 75 135 C 03 US ...
Page 77: ...Over belt magnetic separator UME C Appendix 71 GB_UME 75 135 C 03 US 12 7 Spare parts list ...
Page 78: ...Over belt magnetic separator UME C Appendix 72 GB_UME 75 135 C 03 US ...
Page 80: ...2 GB_Ersatzteil UME 75 115 C 01 ...
Page 82: ...Over belt magnetic separator UME C Appendix 74 GB_UME 75 135 C 03 US ...
Page 84: ......