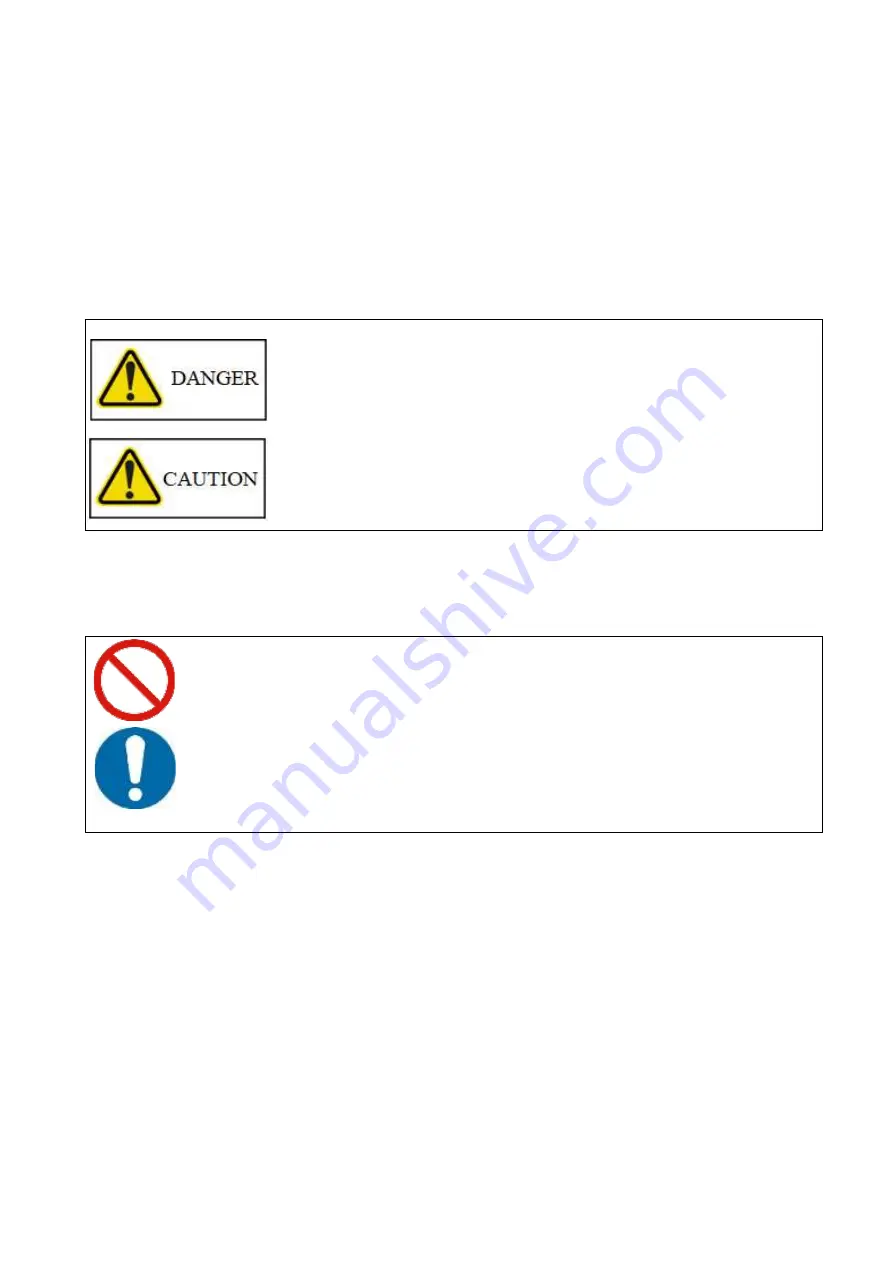
i
Safety Precautions
Thank you for purchasing Shihlin Electric product. This user manual introduces how to install,
wiring, inspect and operate Shihlin Servo Drive and Motor. Please read related items in this
user manual prior to installation and operation for safety.
■
There are 2 safety notification levels in this user manual: Danger and Caution.
It indicates that it may cause severe or fatal injuries if the
instructions are not followed.
It indicates that it may cause moderate injury or malfunction of the
product if the instructions are not followed.
Besides, for those items remark as CAUTION, it may cause bad consequences in some cases,
please follow the instructions to operate due to its importance.
■
Below symbols indicate the items should be followed.
It indicates the FORBIDDEN items.
It Indicates the MANDATORY Items.
In this user manual, NOTE indicates the cautions which may not cause malfunction of the
product, but need pay attention.
Please read this manual carefully and keep it properly to make sure the user can reach it freely.
Summary of Contents for SDP Series
Page 33: ...20 400V series DC 24V Power supply Note terminal P N cannot be grounded ...
Page 45: ...32 4 The last step is to fasten the screw of housing ...
Page 385: ...372 ...
Page 405: ...392 ...
Page 499: ...486 SME L040 SME L075 SME L100 SME L150 ...
Page 500: ...487 SME L200 SME L300 SME M100 SME M150 ...
Page 509: ...496 When the load reaches 300 the operation time is 5 51 seconds ...
Page 555: ...542 14 5 Manual version and revision history Manual version V1 00 Release month July 2022 ...