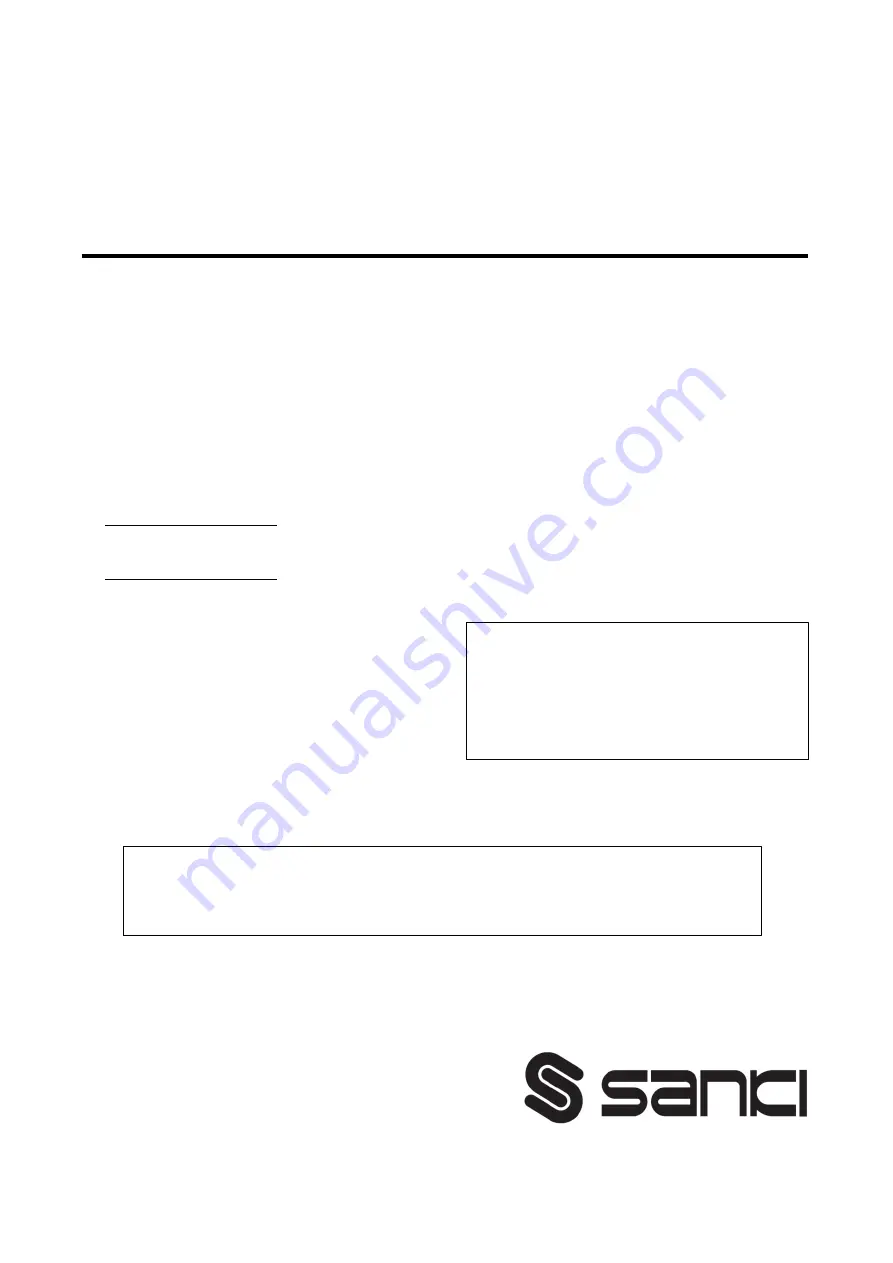
Electromagnetic Feeder Controller
Instruction Manual
【
St Feedback Type
】
MFC-S3B-F
MFC-S6B-F
This Instruction Manual is applicable to
Electromagnetic Feeder Controller version
1 and later.
Confirm the version information displayed
upon powering ON.
Read the Manual carefully beforehand to ensure the safe use of the Controller.
After reading, store the Manual within reach so as to be ready for rereading.
The dealer is requested to be sure to deliver the Manual to the end user.