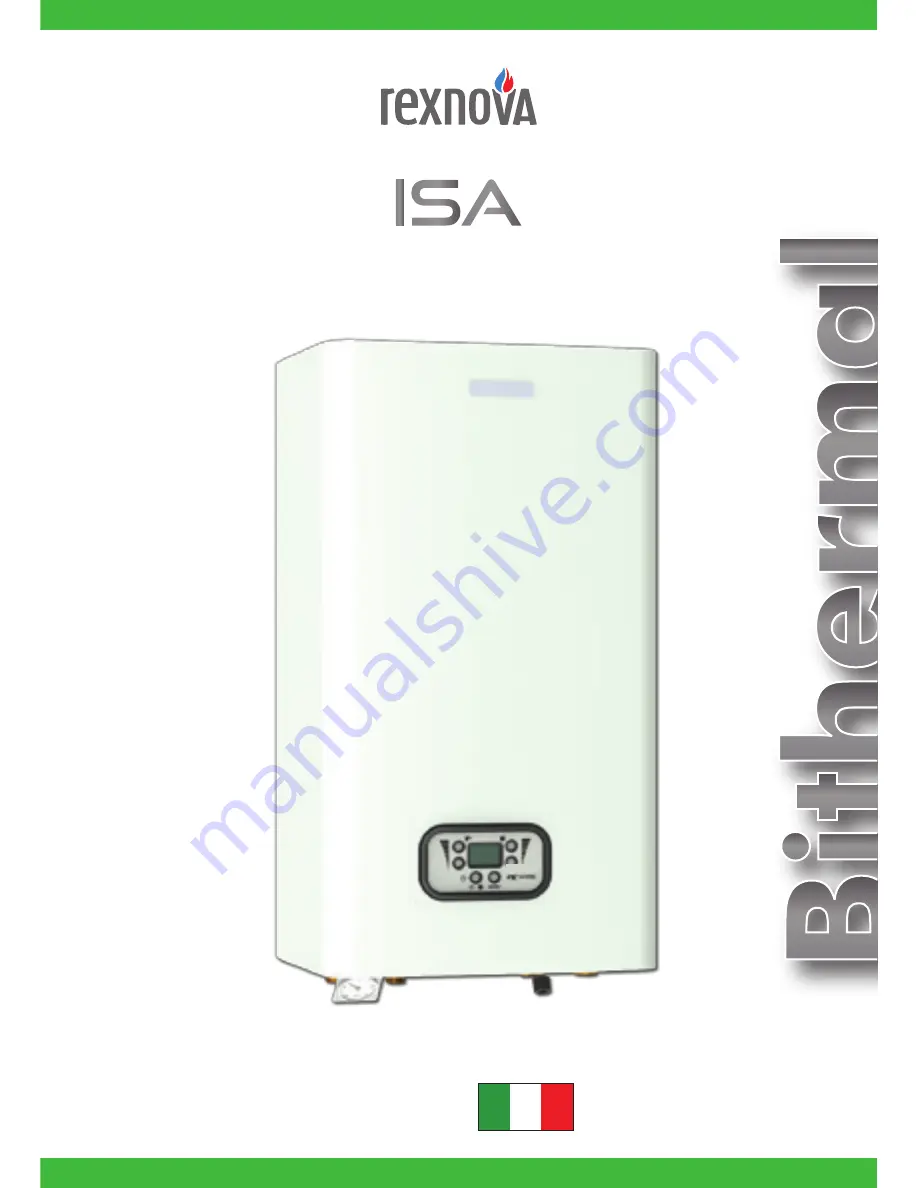
Wall-hung boiler with integrated heat exchanger
20kw Bithermal
ITALIAN DESIGN
MADE IN ITALY
INSTALLATION, COMMISSIONING, USE AND MAINTENANCE MANUAL
G20 ENGINEERING SRL Loc. Campogrande 13, 29013 CARPANETO PIACENTINO (PC), Italy
phone +39 0523 850513 - fax. +39 0523 850712 - www.aircontrol-pc.com - www.g20engineering.com
A Brand by
G20 ENGINEERING
A brand by
G20 ENGINEERING
Summary of Contents for ISA 20 BITHERMAL
Page 2: ......
Page 3: ...ISA 20 KW BITHERMAL BOILER MANUAL VERS 07 2016 REV 1 ...
Page 33: ...NOTE ...
Page 34: ...NOTE ...
Page 35: ......