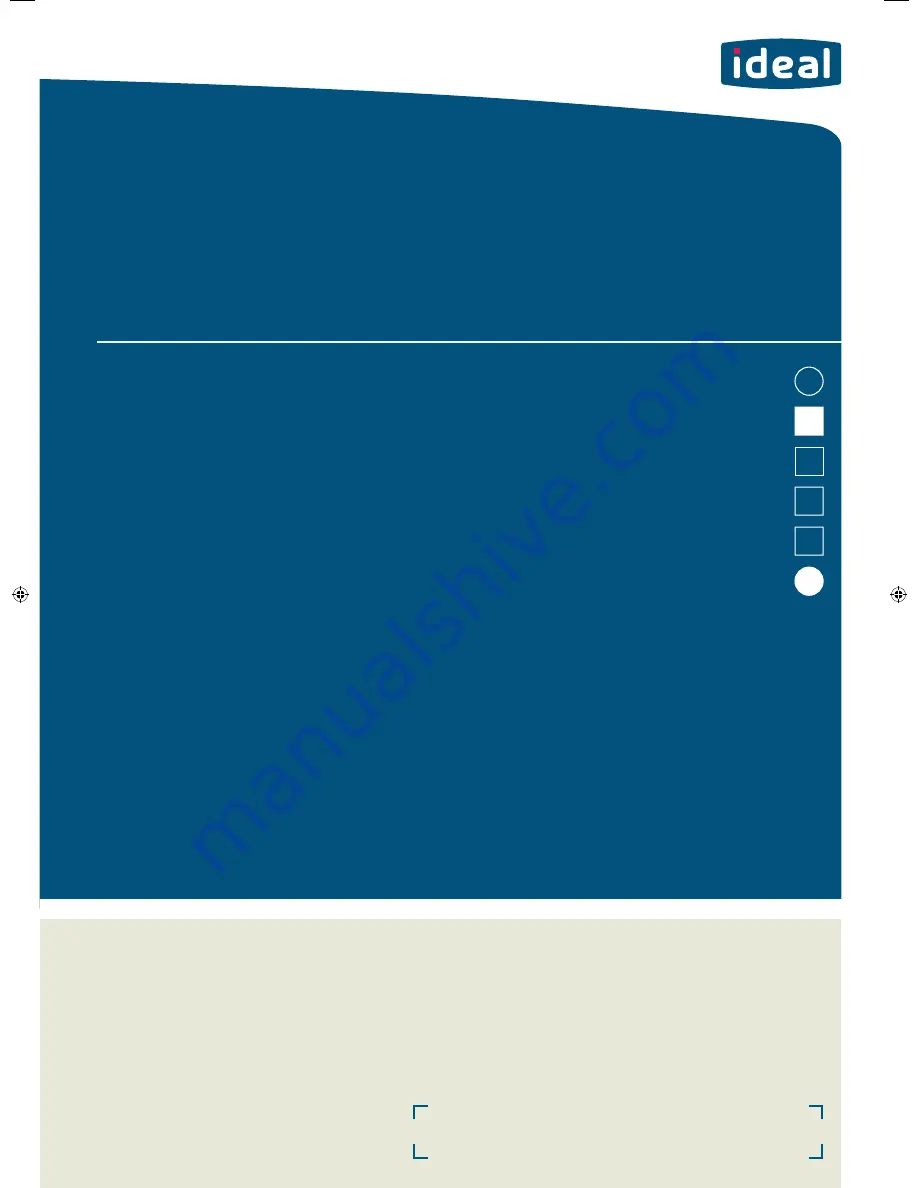
INSTALLATION
AND SERVICING
LOGIC + Combi
24, 30, 35
For details of document amendments, refer to page 3
When replacing any part on this appliance, use only spare parts that you can be
assured conform to the safety and performance specification that we require.
Do not use reconditioned or copy parts that have not been clearly authorised by Ideal.
For the very latest copy of literature for specification and maintenance practices visit our
website www.idealheating.com where you can download the relevant information in PDF format.
October 2010
UIN 204978 A04
204978-4.indd 1
20/10/2010 14:04:29