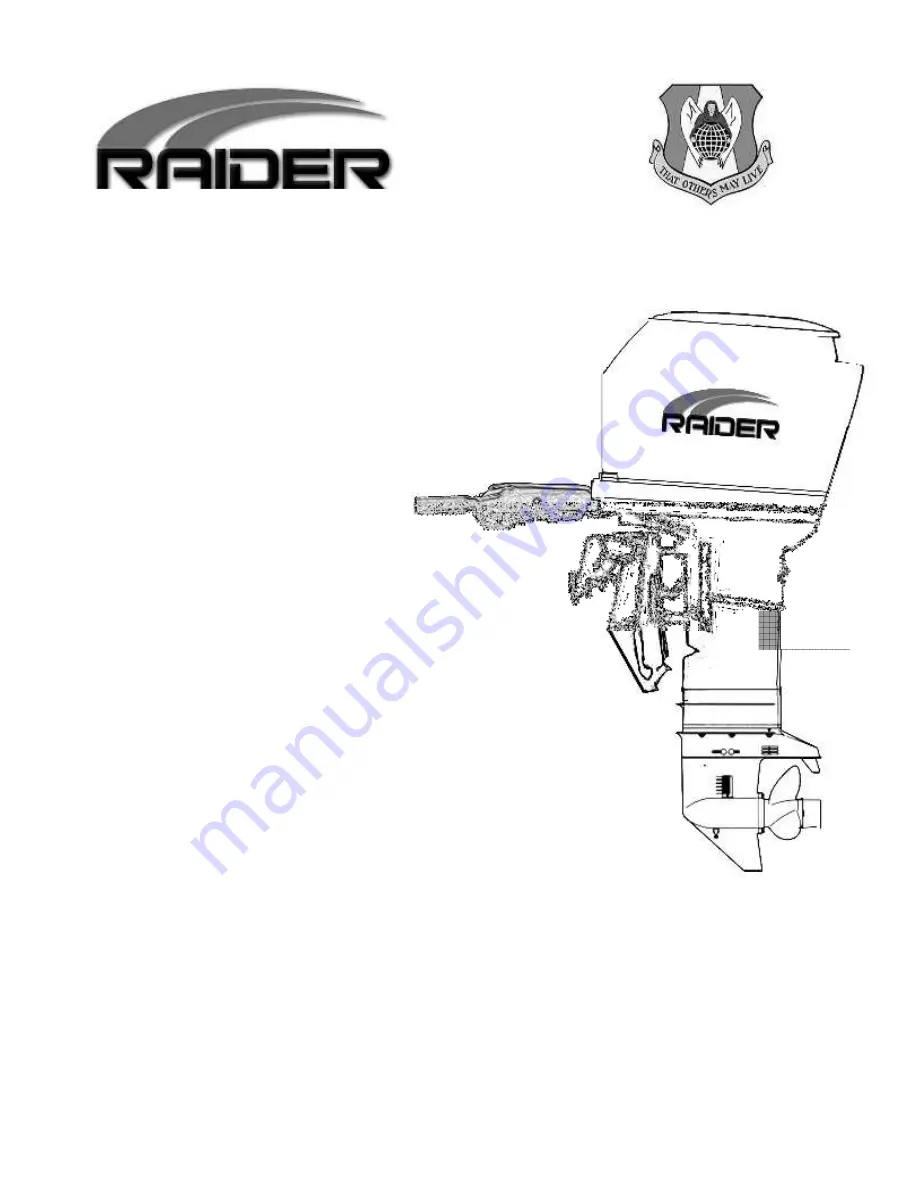
SERVICE MANUAL
•
Two stroke Low pressure
•
Direct Injection (TLDI)
•
Multi-fuel
•
Submersible
This manual has been prepared for the United States Guardian Angels for
service of the Multi-fuel, Submersible Outboard motor designed and manufactured
under Contract No. N61331⑩11⑩C-0008, dated 3/4/11. The data presented in this
manual was revised as of August 2013 representing the latest revision.
August 2013
Summary of Contents for 50 HP TLDI
Page 3: ......
Page 9: ...1 2 2 O 2 O 2 O 2 Outline Dimensions utline Dimensions utline Dimensions utline Dimensions...
Page 17: ...1 10...
Page 19: ...2 2...
Page 20: ...2 1...
Page 35: ...2 16 5 Special Tools 5 Special Tools 5 Special Tools 5 Special Tools...
Page 43: ...2 24...
Page 48: ...3 5...
Page 50: ...3 7...
Page 54: ...3 11...
Page 57: ...4 2 1 1 1 1 Power Uni Power Uni Power Uni Power Unit t t t...
Page 60: ...4 5...
Page 66: ...4 11...
Page 68: ...4 13...
Page 72: ...4 17...
Page 75: ...4 20...
Page 86: ...4 31...
Page 97: ...4 42 Piston and Crankshaft Piston and Crankshaft Piston and Crankshaft Piston and Crankshaft...
Page 106: ...4 51...
Page 111: ...5 2 1 1 1 1 Wire Routing Wire Routing Wire Routing Wire Routing...
Page 112: ...5 3...
Page 113: ...5 4...
Page 114: ...5 5...
Page 115: ...5 6...
Page 116: ...5 7 Wiring Diagram 40B 50B EPTO...
Page 117: ...5 8...
Page 118: ...5 9...
Page 119: ...5 10...
Page 120: ...5 11...
Page 121: ...5 12...
Page 126: ...5 17 Note Slash shows stripe color of cable 2 2 2 2 Assembly Assembly Assembly Assembly...
Page 127: ...5 18 Wiring around solenoid Bracket...
Page 128: ...5 19...
Page 129: ...5 20...
Page 130: ...5 21...
Page 136: ...5 27 Kill Switch Crank Sensor Oil Level Sensor Grounds Air Injector 1...
Page 137: ...5 28 Air Injector 2 Air Injector 3 Coil 1 Coil 2 Coil 3...
Page 138: ...5 29 Fuel Pump Fuse Box Regulator Stator Complete Wiring harness...
Page 140: ...6 2 1 1 1 1 Configuration Configuration Configuration Configuration GEARCASE DRIVESHAFT...
Page 141: ...6 3 GEARCASE PROPELLERSHAFT...
Page 152: ...6 14...
Page 153: ...6 15...
Page 185: ...10 20...
Page 193: ...11 8...