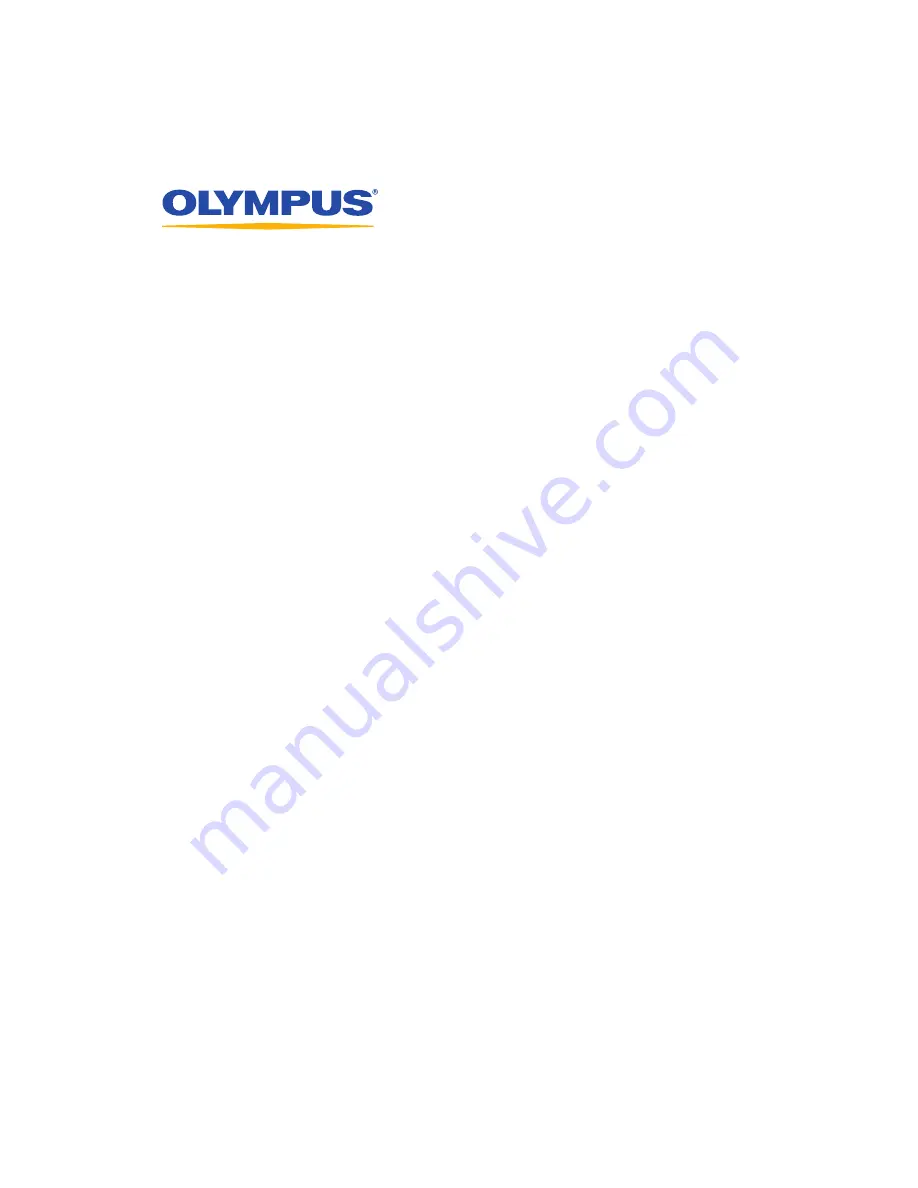
DMTA069-01EN — Rev. D
March 2017
ChainSCANNER
Chain-Link Mounted Scanner
User’s Manual
This instruction manual contains essential information on how to use this Olympus product safely and effectively.
Before using this product, thoroughly review this instruction manual. Use the product as instructed.
Keep this instruction manual in a safe, accessible location.
Summary of Contents for ChainSCANNER
Page 5: ...DMTA069 01EN Rev D March 2017 Table of Contents v Index 87 ...
Page 6: ...DMTA069 01EN Rev D March 2017 Table of Contents vi ...
Page 8: ...DMTA069 01EN Rev D March 2017 List of Abbreviations viii ...
Page 18: ...DMTA069 01EN Rev D March 2017 Important Information Please Read Before Use 10 ...
Page 20: ...DMTA069 01EN Rev D March 2017 Introduction 12 ...
Page 28: ...DMTA069 01EN Rev D March 2017 Chapter 1 20 ...
Page 64: ...DMTA069 01EN Rev D March 2017 Chapter 5 56 ...
Page 74: ...DMTA069 01EN Rev D March 2017 Chapter 6 66 ...
Page 78: ...DMTA069 01EN Rev D March 2017 Chapter 7 70 ...
Page 84: ...DMTA069 01EN Rev D March 2017 Appendix A 76 ...
Page 94: ...DMTA069 01EN Rev D March 2017 List of Tables 86 ...