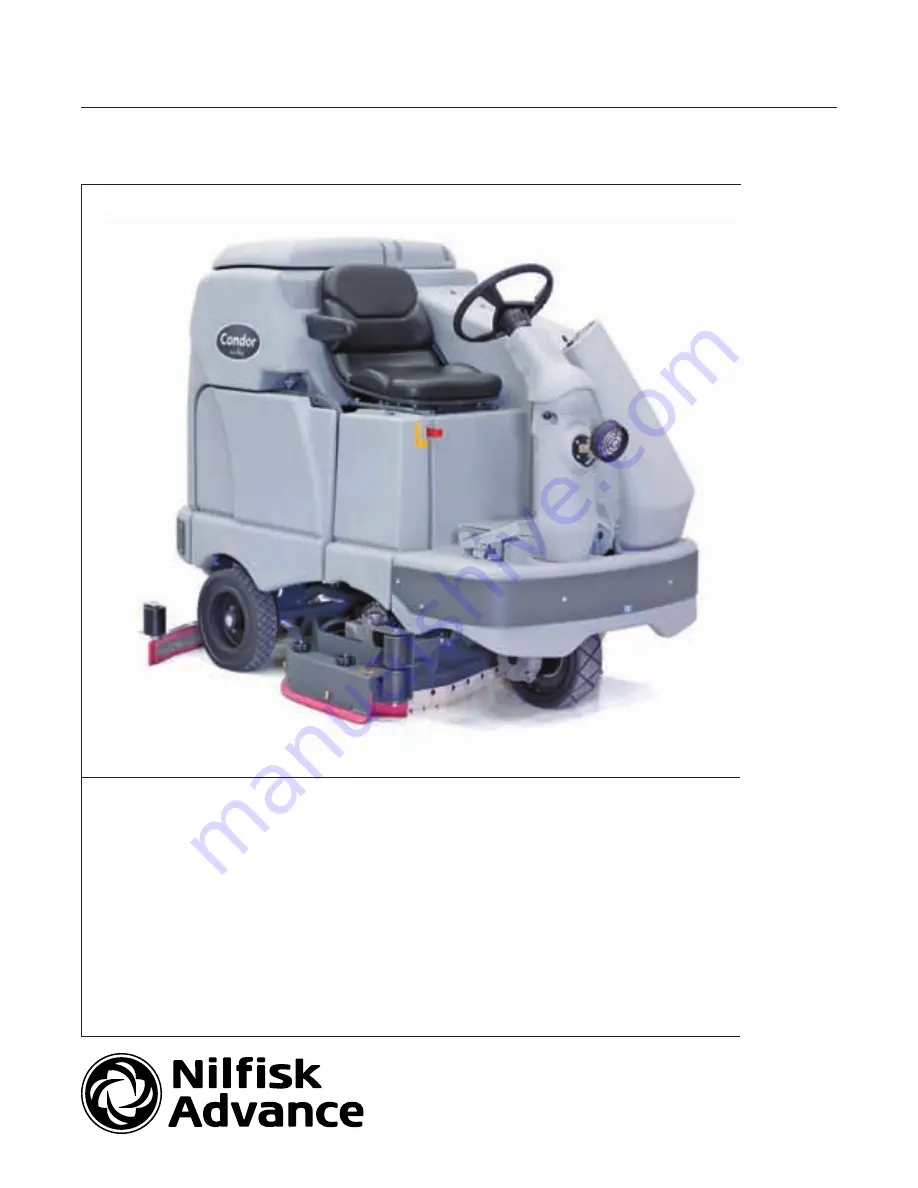
Condor
™
EcoFlex
™
, BR 1100 S/SC EcoFlex
™
, BR 1300 S/SC EcoFlex
™
7/11 Form No. 56043154
Service Manual
Advance Models:
56381032 (X4030D-EcoFlex)
56381037 (X4830C-EcoFlex w/Side Broom)
56381033 (X4030C-EcoFlex w/Side Broom)
56381043 (X4030C-EcoFlex w/o Side Broom)
56381034 (X4530D-EcoFlex)
56381044 (X4530C-EcoFlex w/o Side Broom)
56381035 (X4530C-EcoFlex w/Side Broom)
56381045 (X4830C-EcoFlex w/o Side Broom)
56381036 (X4830D-EcoFlex)
Nilfisk Models:
56413006 (BR1000 S EcoFlex w/o Side Broom) 56413007 (BR1000 S C EcoFlex w/Side Broom)
56413010 (BR1300 S EcoFlex w/o Side Broom) 56413011 (BR1300 S C EcoFlex w/Side Broom)
English