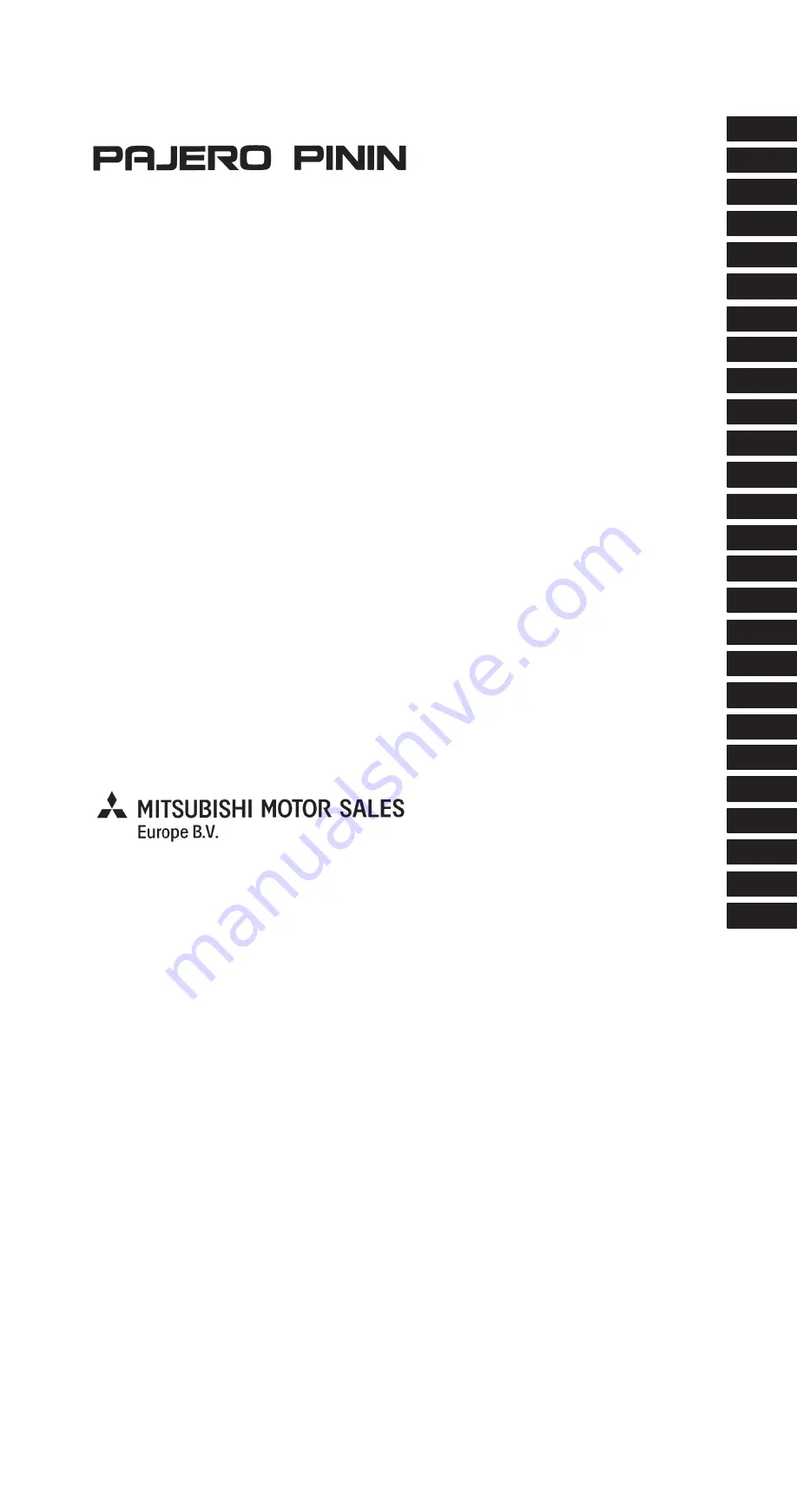
General . . . . . . . . . . . . . . . . . . . . . . . .
Engine . . . . . . . . . . . . . . . . . . . . . . . . .
Engine Lubrication . . . . . . . . . . . . . .
Fuel . . . . . . . . . . . . . . . . . . . . . . . . . . . .
Engine Cooling . . . . . . . . . . . . . . . . .
Intake and Exhaust . . . . . . . . . . . . .
Engine Electrical . . . . . . . . . . . . . . . .
Engine and Emission Control . . . .
Clutch . . . . . . . . . . . . . . . . . . . . . . . . . .
Manual Transmission . . . . . . . . . . . .
Automatic Transmission . . . . . . . . .
Propeller Shaft . . . . . . . . . . . . . . . . . .
Front Axle . . . . . . . . . . . . . . . . . . . . . .
Rear Axle . . . . . . . . . . . . . . . . . . . . . . .
Wheel and Tyre . . . . . . . . . . . . . . . . .
Power Plant Mount . . . . . . . . . . . . . .
Front Suspension . . . . . . . . . . . . . . .
Rear Suspension . . . . . . . . . . . . . . . .
Service Brakes . . . . . . . . . . . . . . . . . .
Parking Brakes . . . . . . . . . . . . . . . . .
Steering . . . . . . . . . . . . . . . . . . . . . . . .
Body . . . . . . . . . . . . . . . . . . . . . . . . . . .
Exterior . . . . . . . . . . . . . . . . . . . . . . . .
Chassis Electrical . . . . . . . . . . . . . . .
WORKSHOP MANUAL
FOREWORD
This Workshop Manual contains procedures for
service mechanics, including removal, disassembly,
inspection, adjustment, reassembly and installation.
Use the following manuals in combination with this
manual as required.
TECHNICAL INFORMATION MANUAL
IKRE00E1
WORKSHOP MANUAL
ELECTRICAL WIRING
EKRE00E1
BODY REPAIR MANUAL
BKRE00E1
ENGINE GROUP
PWEE9502-E
PARTS CATALOGUE
I603F509D
j
All information, illustrations and product descriptions
contained in this manual are current as at the time
of publication. We, however, reserve the right to
make changes at any time without prior notice or
obligation.
ªGDIº is a trade mark which Mitsubishi Motors
Corporation holds.
E
Mitsubishi Motors Corporation
August 1999
Interior and Supplemental
Restraint System (SRS) . . . . . . . .
Heater, Air Conditioner and
Ventilation . . . . . . . . . . . . . . . . . . . . .
Summary of Contents for Pajero Pinin 1999
Page 32: ...NOTES ...
Page 73: ...13A 1 FUEL CONTENTS GASOLINE DIRECT INJECTION GDI 13A FUEL SUPPLY 13B ...
Page 190: ...NOTES ...
Page 191: ...13B 1 FUEL SUPPLY CONTENTS FUEL TANK 2 Fuel Pump Module 4 ...
Page 214: ...NOTES ...
Page 222: ...NOTES ...
Page 256: ...NOTES ...
Page 274: ...NOTES ...
Page 282: ...NOTES ...
Page 360: ...NOTES ...
Page 412: ...NOTES ...
Page 443: ...32 1 POWER PLANT MOUNT CONTENTS ENGINE MOUNTING 2 TRANSMISSION MOUNTING 3 ...
Page 446: ...NOTES ...
Page 447: ......
Page 448: ......
Page 449: ......
Page 450: ......
Page 451: ......
Page 452: ......
Page 453: ......
Page 454: ......
Page 455: ......
Page 456: ......
Page 457: ......
Page 458: ......
Page 459: ......
Page 460: ......
Page 461: ......
Page 467: ...NOTES ...
Page 468: ...BASIC BRAKE SYSTEM 35A ANTI SKID BRAKING SYSTEM ABS 4WD 35B 35A 1 SERVICE BRAKES CONTENTS ...
Page 499: ...NOTES ...
Page 531: ...NOTES ...
Page 541: ...NOTES ...
Page 649: ...NOTES ...
Page 728: ...54A 1 CHASSIS ELECTRICAL CONTENTS CHASSIS ELECTRICAL 54A SMART WIRING SYSTEM SWS 54B ...
Page 883: ...NOTES ...
Page 919: ...NOTES ...