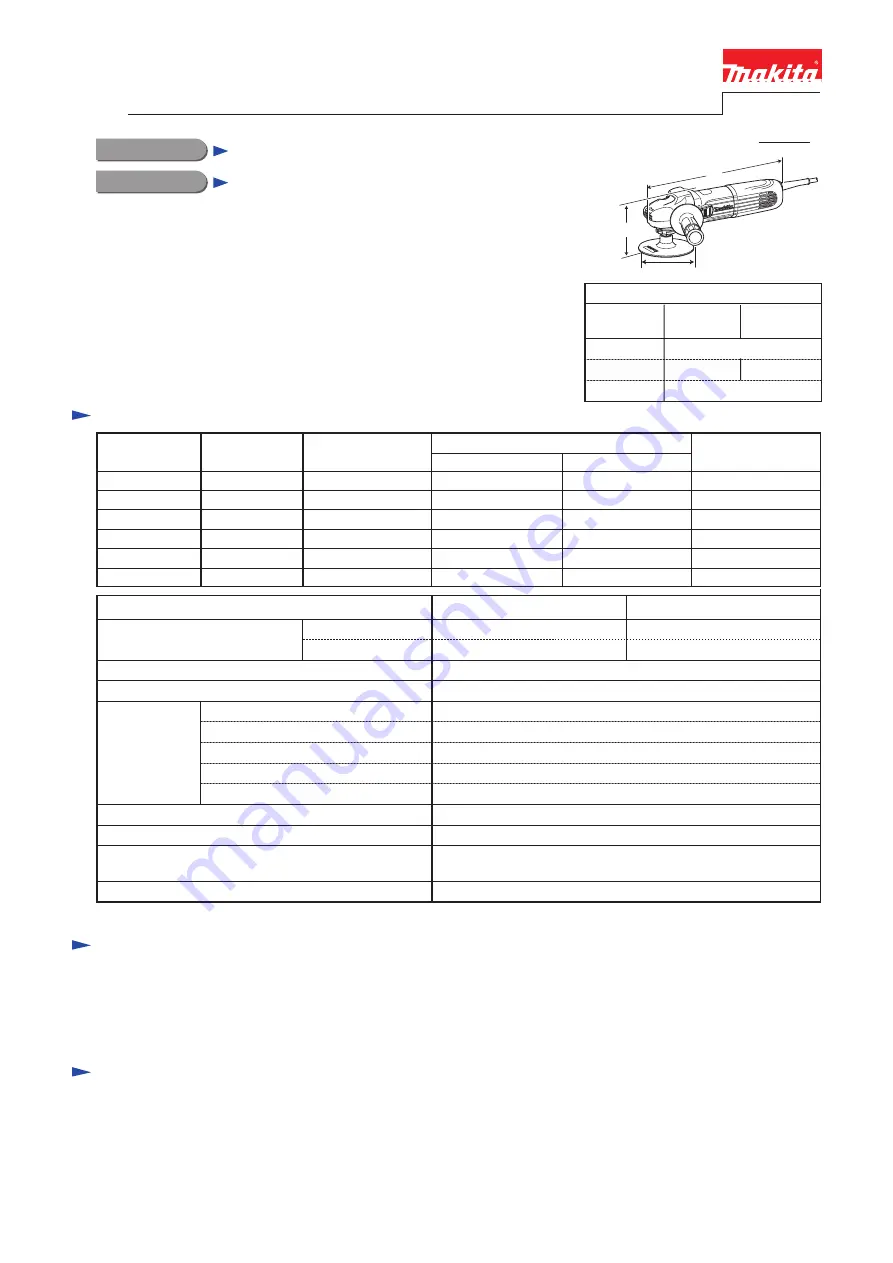
PRODUCT
P 1/ 1
2
Model No.
Description
C
ONCEPT AND MAIN APPLICATIONS
SA4540C/ SA4542C, SA5040C/ SA5042C
Angle Sanders 115mm (4-1/2"), 125mm (5")
For Models SA5040C/ SA5042C
Rubber pad 115
Lock nut 14-48
Abrasive disc 125-24, 30, 50, 80, 120
Abrasive disc (Hook and loop type) 125-40, 60, 80, 120, 180
Wire cup brush 90 set
Wheel cover for wire cup brush 90
Dust collecting wheel cover
etc.
For Models SA4540C/ SA4542C
Rubber pad 100
Lock nut 14-48
Abrasive disc 115-24, 30, 50, 80, 120
Abrasive disc (Hook and loop type) 115-40, 60, 80, 120, 180
Wire cup brush 90 set
Wheel cover for wire cup brush 90
Dust collecting wheel cover
etc.
L
H
W
1,400W Angle sander series models, SA4540C, SA4542C, SA5040C and
SA5042C are successor models of 9565CVL, featuring:
•
"
Super Joint System II
"
developed for effective vibration absorption
• Electronic current limiter, speed control and soft start
• Anti-restart function (f
or
models SA4540C, SA5040C only
)
• Re-designed durable gear housing
• Ergonomically best possible barrel grip
S
pecification
Continuous Rating (W)
Voltage (V)
Cycle (Hz)
Input
Output
840
Max. Output (W)
110
120
220
230
240
13
12
6.7
6.4
6.1
50/60
50/60
50/60
50/60
50/60
1,400
1,400
1,400
1,400
1,400
2,100
2,100
1,800
2,000
2,100
Current (A)
840
127
12
50/60
---
2,000
840
840
840
840
*1
with Side grip
Model No.
No load speed: min.
ˉ
¹=rpm
Abrasive disc
Pad
Capacity: mm (")
Protection against electric shock
Power supply cord: m (ft)
Weight according to EPTA-Procedure 01/2003
*
1
: kg (")
European countries except UK: 4.0 (13.2),
Brazil, Australia: 2.0 (6.6), Other countries: 2.5 (8.2)
2,000 - 7,800
Double insulation
115 (4-1/2)
Shock absorbing System
Mechanical brake
Super Joint System II
Yes
Yes
Yes
SA4540C, SA5040C: Yes/ SA4542C, SA5042C: No
Constant speed control
Variable speed control by dial
Soft start
Electronic current limiter
Anti-restart function
Electronic
control
Yes
No
SA5040C/ SA5042C
SA4540C/ SA4542C
125 (5)
105 (4-1/8)
115 (4-1/2)
2.4 (5.2)
S
tandard equipment
Note:
The standard equipment for the tool shown above may vary by country.
Side grip ................................ 1 (normal type or anti-vibration type)
Lock nut wrench .................... 1
Pad 115 .................................. 1 (for SA4540C/ SA4542C)
Pad 125 .................................. 1 (for SA5040C/ SA5042C)
O
ptional accessories
T
ECHNICAL INFORMATION
Dimensions: mm (")
Width (W)
Height (H)
Length (L)
105 (4-1/8)
315 (12-3/8)
Model No. SA4540C
SA4542C
121 (4-3/4)
SA5040C
SA5042C
115 (4-1/2)