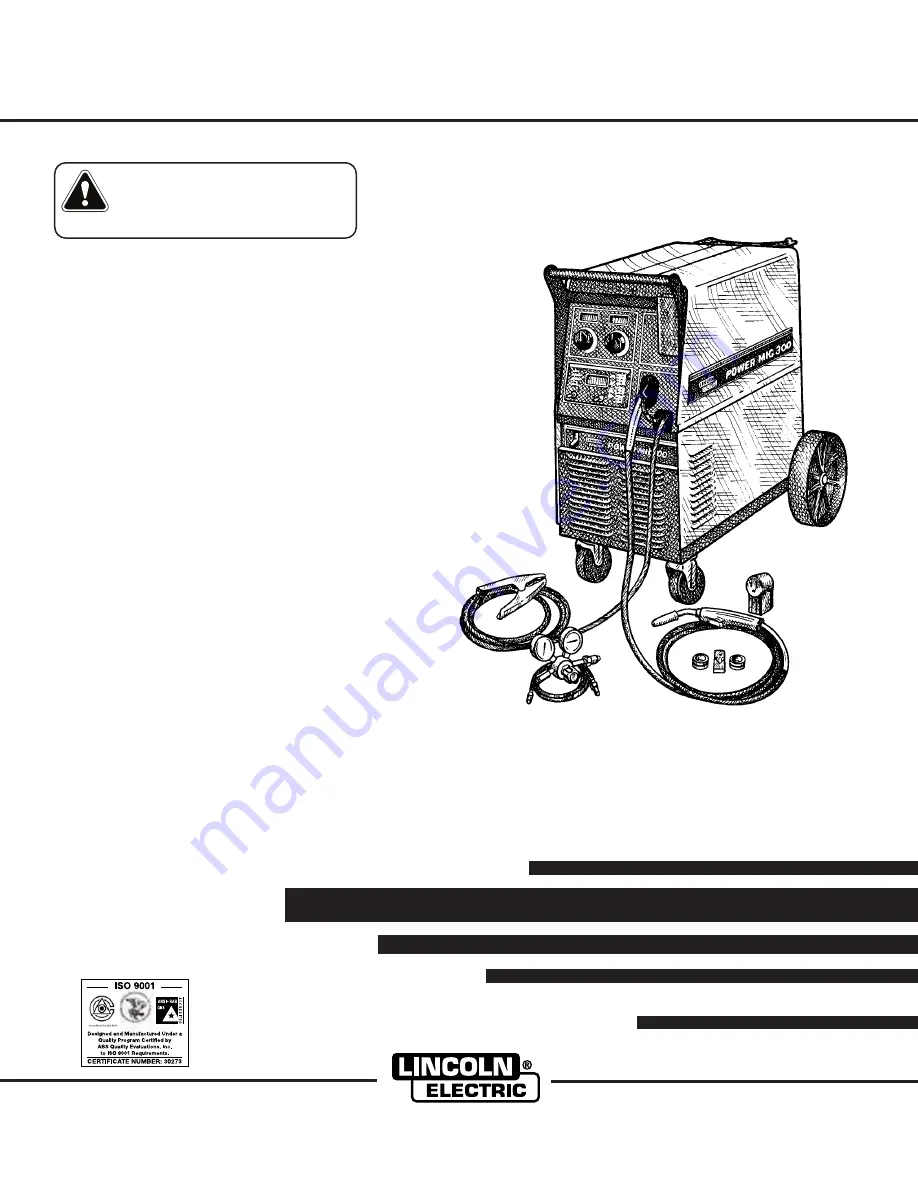
POWER MIG
™
300
OPERATOR’S MANUAL
IM736-D
February, 2004
Safety Depends on You
Lincoln arc welding and cutting
equipment is designed and built
with safety in mind. However, your
overall safety can be increased by
proper installation ... and thought-
ful operation on your part.
DO
NOT INSTALL, OPERATE OR
REPAIR THIS EQUIPMENT
WITHOUT READING THIS
MANUAL AND THE SAFETY
PRECAUTIONS CONTAINED
THROUGHOUT.
And, most
importantly, think before you act
and be careful.
For use with machine Code Numbers: 10562, 10952, 10958, 11000, 11097, 11098
For use with machine
• Sales and Service through Subsidiaries and Distributors Worldwide •
Cleveland, Ohio 44117-1199 U.S.A. TEL: 216.481.8100 FAX: 216.486.1751 WEB SITE: www.lincolnelectric.com
• World's Leader in Welding and Cutting Products •
Copyright © 2004 Lincoln Global Inc.
This manual covers equipment which is no
longer in production by The Lincoln Electric Co.
Specifications and availability of optional
features may have changed.
Summary of Contents for POWER MIG 300
Page 43: ...DIMENSION PRINT F 5 POWER MIG 300 F 5 3 00F M19231 ...
Page 44: ...NOTES POWER MIG 300 ...
Page 45: ...NOTES POWER MIG 300 ...