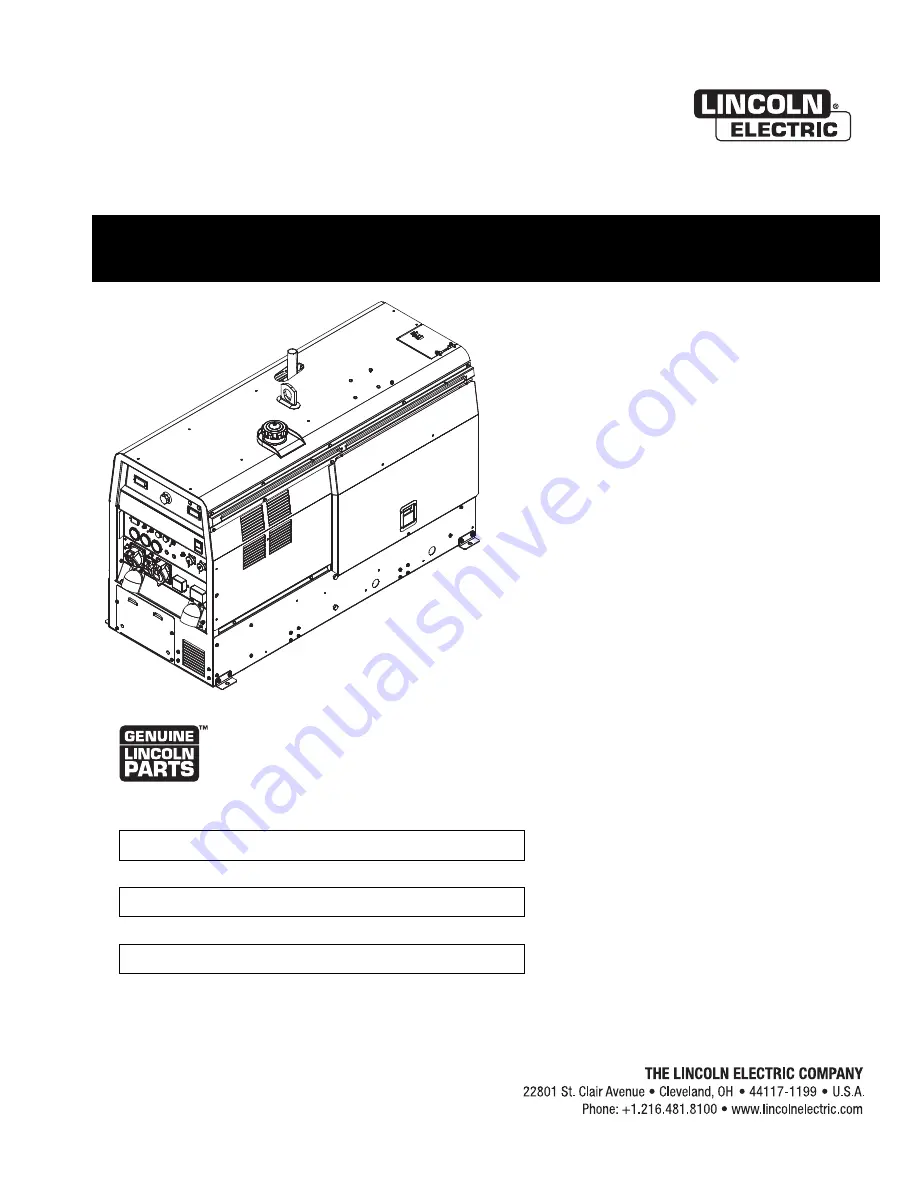
Operator’s Manual
Vantage
®
500 (CE)
Register your machine:
www.lincolnelectric.com/register
Authorized Service and Distributor Locator:
www.lincolnelectric.com/locator
IM894-F
| Issue D ate Oct-16
© Lincoln Global, Inc. All Rights Reserved.
For use with machines having Code Numbers:
11298, 11299, 11524, 11525,
11574, 11575, 11963, 12196,
12333, 12364, 12657
Need Help? Call 1.888.935.3877
to talk to a Service Representative
Hours of Operation:
8:00 AM to 6:00 PM (ET) Mon. thru Fri.
After hours?
Use “Ask the Experts” at lincolnelectric.com
A Lincoln Service Representative will contact you
no later than the following business day.
For Service outside the USA:
Email: [email protected]
Save for future reference
Date Purchased
Code: (ex: 10859)
Serial: (ex: U1060512345)
Summary of Contents for Vantage 500 CE
Page 33: ...F 1 DIAGRAMS F 1 VANTAGE 500 CE ...
Page 34: ...F 2 DIAGRAMS F 2 VANTAGE 500 CE ...
Page 35: ...F 3 DIAGRAMS F 3 VANTAGE 500 CE ...
Page 36: ...F 4 DIAGRAMS F 4 VANTAGE 500 CE ...
Page 41: ...NOTES VANTAGE 500 CE ...