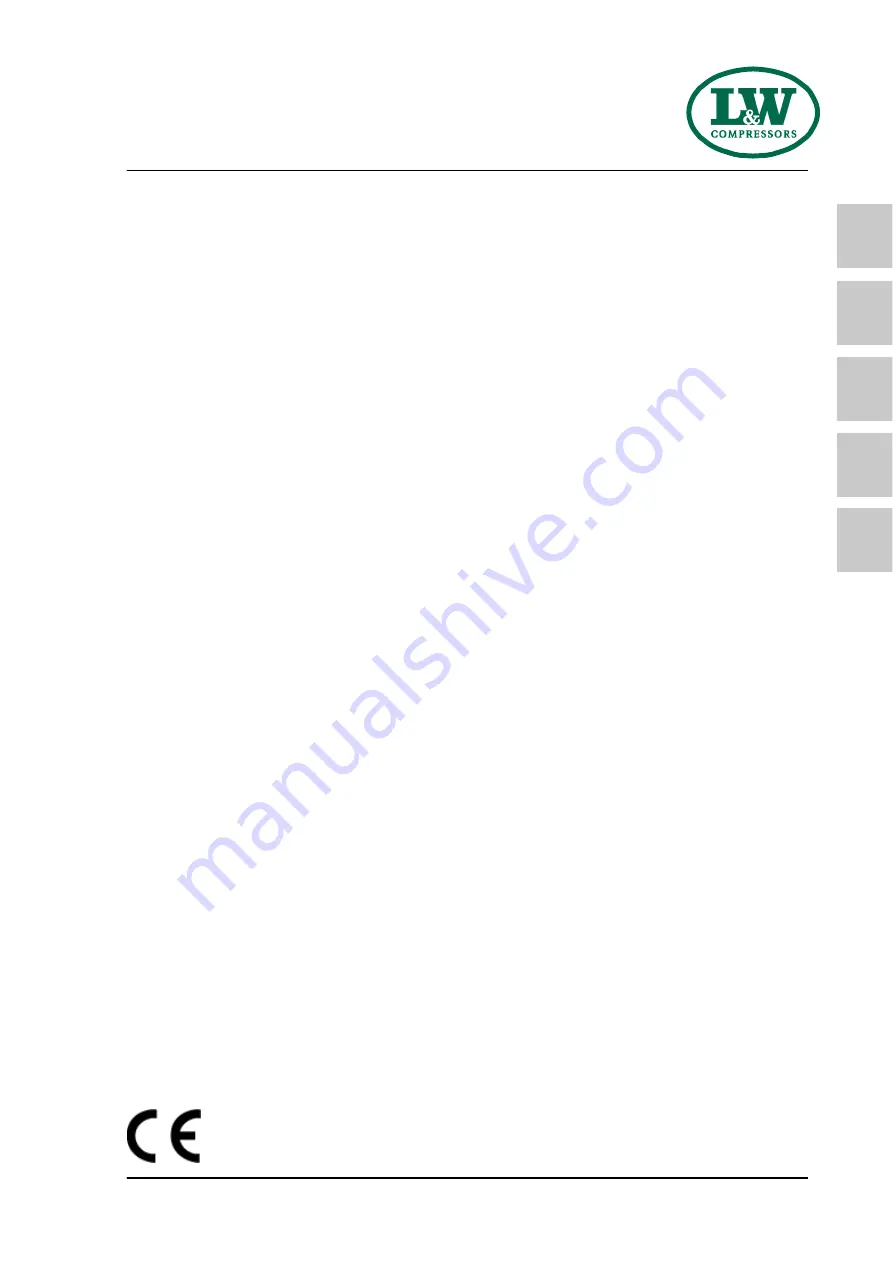
C H A P T E R O V E R V I E W
Operating Instructions
..............................................................................................................
ECC - Electronic Compressor Control (if equipped)
.........................................................
Spare Parts Lists
..........................................................................................................................
Options
(if equipped)
.................................................................................................................
Attachment
....................................................................................................................................
A
B
C
D
E
Manufacturer in terms of 97/23/EC
The full name and address of the manufacturer is:
Lenhardt & Wagner GmbH
An der Tuchbleiche 39
68623 Hüttenfeld / Germany
Phone: +49 (0) 62 56 - 85 88 0 - 0
Fax: +49 (0) 62 56 - 85 88 0 - 14
E-Mail: [email protected]
Internet: www.lw-compressors.com
Summary of Contents for LW 300 EC III
Page 3: ...A Operating Instructions Breathing Air Compressor LW 300 EC III LW 450 EC III Version 04 18 E ...
Page 12: ...A S A F E T Y P R E C A U T I O N S ...
Page 19: ...A I N S TA L L AT I O N ...
Page 26: ...A O P E R AT I O N ...
Page 34: ...A R E M E D Y I N G FA U LT S ...
Page 39: ...A M A I N T E N A N C E A N D S E R V I C E ...
Page 70: ...A M A I N T E N A N C E R E C O R D S ...
Page 78: ...B Operating Instructions ECC Electronic compressor control www uebler net Version 11 12 E ...
Page 98: ...C ERSATZTEILLISTEN SPARE PARTS LISTS DETAILANSICHTEN DETAILED VIEWS ...
Page 146: ...D O P T I O N S ...
Page 148: ...D A U T O S H U T D O W N D 1 LW 300 450 E Compact III ...
Page 153: ...D A U T O M A T I C C O N D E N S AT I O N D R A I N D 6 LW 300 450 E Compact III ...
Page 186: ...D A U T O S T A R T F U N C T I O N D 39 LW 300 450 E Compact III ...
Page 192: ...D O I L P R E S S U R E G A U G E D 45 LW 300 450 E Compact III ...
Page 195: ...D O I L P R E S S U R E M O N I T O R I N G D 48 LW 300 450 E Compact III ...
Page 201: ...D O I L T E M P E R A T U R E M O N I T O R I N G D 54 LW 300 450 E Compact III ...
Page 207: ...D I N T E R S TA G E P R E S S U R E G A U G E S D 60 LW 300 450 E Compact III ...
Page 217: ...D A I R C O O L E R C O N N E C T I O N K I T D 70 LW 300 450 E Compact III ...
Page 220: ...D C O N D E N S A T E TA N K 6 0 LT R D 73 LW 300 450 E Compact III ...