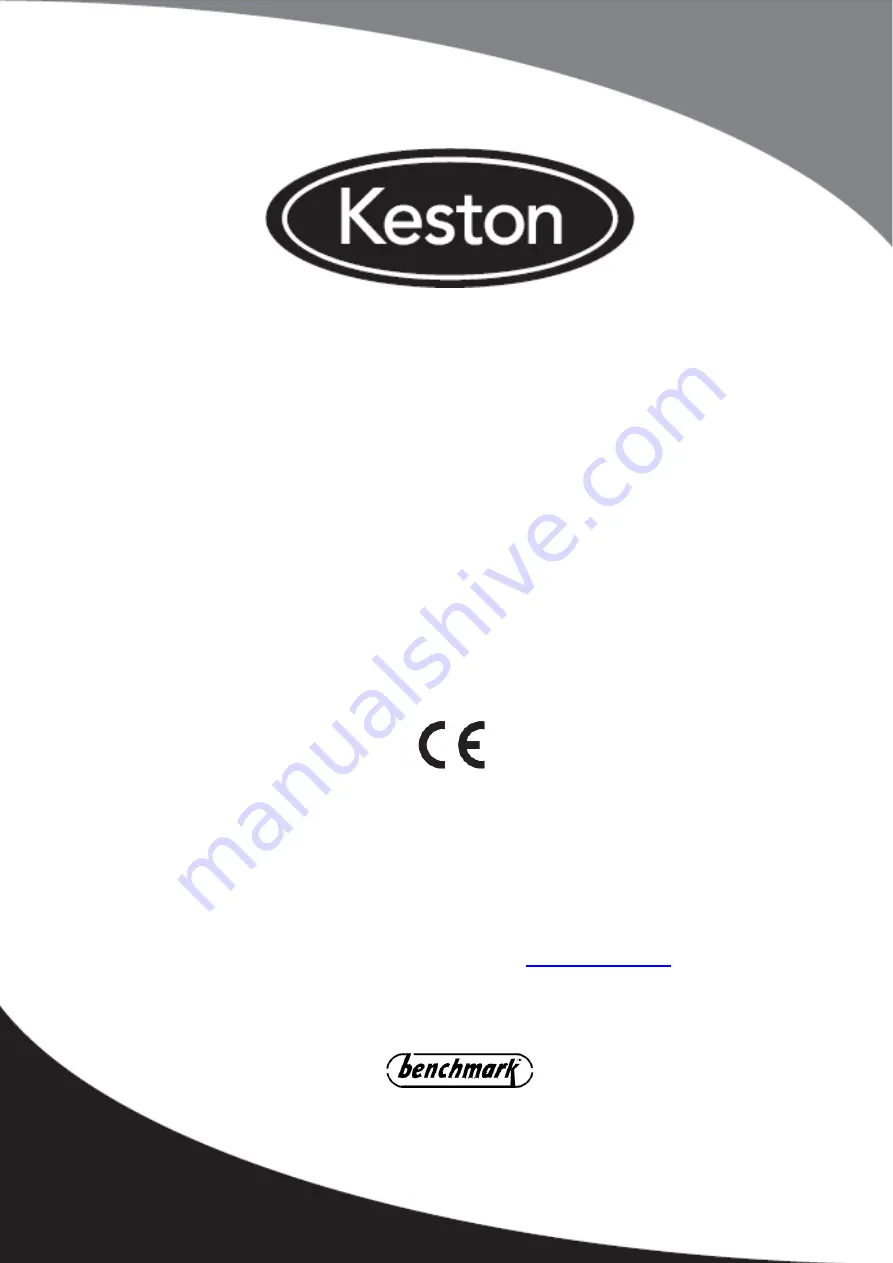
C36 Combi
User, Installation and Servicing
Instructions
FAN POWERED HIGH EFFICIENCY
MODULATING DOMESTIC CONDENSING
GAS COMBINATION BOILER
CE/PI No. 86-CM-44
C36 Combi - GC No. 47-930-01
C36P Combi – GC No. 47-930-02
These instructions must be left either with the
user or next to the site gas meter.
Keston Heating
PO Box 103, National Avenue, Kingston Upon Hull, HU5 4JN
Tel. +44 (0) 1482 443005 Fax. +44 (0) 1482 467133
email : [email protected] web :
www.keston.co.uk
COMPLIANT WITH BUILDING REGULATION PART L1 & L2
SEDBUK A RATED
W D 3 8 8
i s s u e 6 - 2 0 1 1