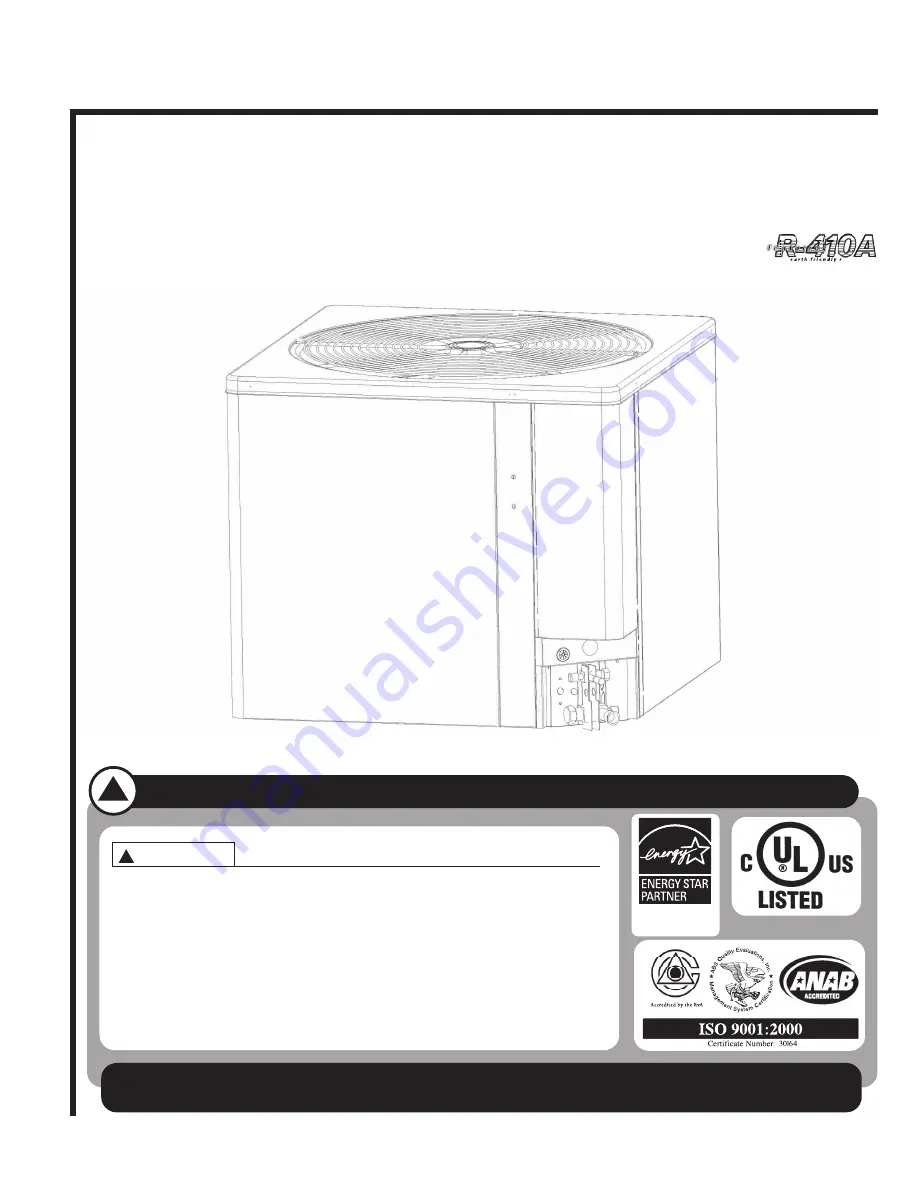
92-21354-78-01
SUPERSEDES 92-21354-78-00
13 & 14.5 SEER SERIES
CONDENSING UNITS
1
1
⁄
2
- 5 TONS FEATURING
EARTH-FRIENDLY R-410A REFRIGERANT
R-410
INSTALLATION INSTRUCTIONS
RECOGNIZE THIS SYMBOL AS AN INDICATION OF IMPORTANT SAFETY INFORMATION!
!
DO NOT DESTROY THIS MANUAL
PLEASE READ CAREFULLY AND KEEP IN A SAFE PLACE FOR FUTURE REFERENCE BY A SERVICEMAN
THESE INSTRUCTIONS ARE INTENDED AS AN AID TO
QUALIFIED, LICENSED SERVICE PERSONNEL FOR PROPER
INSTALLATION, ADJUSTMENT AND OPERATION OF THIS UNIT.
READ THESE INSTRUCTIONS
THOROUGHLY
BEFORE
ATTEMPTING INSTALLATION OR OPERATION. FAILURE TO FOL-
LOW THESE INSTRUCTIONS MAY RESULT IN IMPROPER
INSTALLATION, ADJUSTMENT, SERVICE OR MAINTENANCE
POSSIBLY RESULTING IN FIRE, ELECTRICAL SHOCK,
PROPERTY DAMAGE, PERSONAL INJURY OR DEATH.
WARNING
!
NOTE:
Appearance of unit may vary.
r e f r i g e r a n t
(13 & 14.5 SEER
MODELS IN CERTAIN
MATCHED SYSTEMS)